Decking is a strong and durable material based on steel sheet. Such a product is used for finishing roofing systems, for creating fences and fences, installing small outbuildings, for decorating walls and solving many other economic and construction problems. Of course, the material won the greatest popularity precisely as a roof covering. This is due to its high performance, because subject to the installation technology, profiled sheets will reliably protect the structure from negative weather factors for a fairly long time and withstand high loads in winter. In addition, the coating is easy to install even without much experience in roofing works and not having a professional set of tools. You can also note a wide design variety, which concerns not only the choice of material colors, but also the available sheet profile. And the last factor that probably increases the popularity of corrugated board among consumers is its low cost.
Performing the installation of the roof with your own hands, it is these qualities that become decisive when choosing profiled sheets as a covering. At the same time, often, when purchasing material, the main attention is paid only to the quality of the flooring. However, this approach can lead to the fact that in the very near future the products will begin to rust and fall off. Low-grade components are to blame for this behavior of the material, this is especially true of fixing elements, that is, rivets or screws. It is important not only to buy fasteners with excellent characteristics, but also to know how to calculate the required number of elements. To find out the consumption of self-tapping screws on corrugated board, you should get an idea of \u200b\u200bwhat the required number of products can change.
Features of fastening corrugated board
Not in all conditions, the number of self-tapping screws for fixing the profiled sheets to the roof sheathing will be the same. The most important factors in determining this parameter are:
- wind force, which can be determined from the table of wind loads in a particular region;
- the amount of snow cover, it is also easy to find the value for a specific area in special tables.
The larger each of the parameters, the greater the consumption of self-tapping screws per 1m2 of the profiled sheet. This rule should not be neglected, since in the case of an incorrect calculation, the roof will not be able to withstand the loads placed on it and, at best, its deformation will occur, and at worst, the flooring will be torn off. roofing cake and all installation work have to start over. To understand how many screws are required for fastening, it is worth considering the installation diagram. Since the corrugated board is made on the basis of rolled steel, its length can vary from 40 cm to 14.5 m. That is, consumers can use sheets equal in length to the height of the slope. In this case, you only need to lay one row of material.
However, with self-assembly, it is easier to work with shorter sheets, and therefore the installation will be done in 2-3 rows. The procedure begins with the eaves in the left corner. That is, the first sheet in the bottom row is laid, and the second is mounted on top of it. At the same time, it is important to overlap, at least in one wave. The specific value depends on the angle of inclination of the roof:
- from 5-10 degrees the size of the overlap is 2 waves;
- at an inclination of more than 10 degrees - 1 wave overlap.
Further, the laid corrugated board is aligned along the line of the cornice and fixed in the lowest lathing strip in each wave, and the sheets are connected to each other with special rivets. The next sheet of the second row is also installed on the left side. The corrugated board is laid with both longitudinal and transverse overlap. The specific amount of overlap will also depend on the angle of inclination of the slopes:
- tilt 5-10 degrees - 30 cm overlap;
- tilt 10-15 degrees - 20 cm overlap;
- tilt 15-30 degrees - 17 cm overlap;
- an inclination of more than 30 degrees - an overlap of 10-15 cm.
In places where the sheets overlap, it is required to install fixing elements in each wave. On the main part of the sheet, the screws are screwed in after 1-2 waves in a checkerboard pattern, while the distance between them should not exceed 50 cm.On this basis, we can conclude that the number of screws per 1m2 of the profiled sheet will be 4-8 pieces. Of course, in each case, this parameter is individual and before purchasing all the components and materials, it is recommended to make a plan for the location of the sheets on the roof and calculate the number of fasteners.
Calculation of self-tapping screws for fixing corrugated board
It is not so difficult to make your own calculation of self-tapping screws for corrugated board. It is enough to count the required number of whole sheets for the entire roof or for individual slopes. To do this, it is enough to calculate the area of \u200b\u200bthe roof, that is, measure its length, width and multiply the values, and then divide by the area of \u200b\u200bthe profiled sheet, which is also calculated by multiplying the sides, read also:. The next thing to do is to calculate the number of screws or rivets per sheet. It is worth starting from parameters such as the number of screws for attaching the top, bottom edge and central part. As an example, you can take a sheet with a length of 8 m and a standard width of 110 cm. That is, in this case, 1 row of corrugated board is laid. For the upper and lower edges, you will need 5 self-tapping screws, which will be screwed into each wave, as well as 8 self-tapping screws for the central part, with a step of attachment to the crate of 50 cm.This means that you will need about 18 self-tapping screws per sheet of corrugated board with these dimensions. To understand how many fasteners are needed, it is enough to multiply the resulting number by the number of sheets required.
You can also take the average value, at which the manufacturer's recommended number of screws per 1m2 of the roof is taken into account - 4-8 pcs. That is, knowing the total area, it is enough to multiply the values. Of course, the calculation may differ in each case. For example, at more than 30 degrees, it is recommended to reduce the fastening step, that is, the consumption of screws will also increase. Also, an increased number of fasteners will be needed in case of high wind and snow loads. In addition, more screws are required for the end part of the roof and, if there are many end faces, then the consumption of fixing elements will be increased. It is important to keep in mind that no matter what figure is obtained as a result of the calculations, a 5-10% stock of fasteners should be added to the total. Such a stock may be required both in case of detection of low-quality self-tapping screws, and, if necessary, add fasteners in certain places for the most reliable fixation. Do not forget about the fastening of additional elements, for this you need 3-5 self-tapping screws per running meter.
It should be borne in mind that when buying hardware it is not at all necessary to calculate the screws individually. After all, the exact weight of products with various parameters is known. For example, roofing screw with a diameter of 48 mm and a length of 2.5 cm will weigh 3.5 kg / 1000 pieces, and products with parameters 6.3x152 mm per 1000 pieces will weigh 45 kg. Therefore, it is quite easy for manufacturers to pack self-tapping screws, knowing their weight, in packages from 100 to 6000 pieces, read also:.
Fastening profiled flooring and calculation of self-tapping screws
All of us during the roofing with profiled flooring (corrugated board) faced the questions: how many self-tapping screws are needed and how to fix it correctly, what is the consumption of self-tapping screws per 1 m 2 of profiled sheet and how to choose them correctly.
The scheme of fastening the profiled sheet to the roof with self-tapping screws. The number of screws that are needed per one square meter covering, is from five to six pieces when installing the fence and from six to eight for the roof.
When fastening a profiled sheet, you need to take into account its thickness, dimensions, for a better connection and to avoid unnecessary consequences. In this article, we will analyze how to correctly calculate the number of self-tapping screws and for which profiled sheets it is correct to use them.
When equipping roofs with profiled decking, it is required correct selection length, so that it is larger than the roof slope. We fasten the corrugated board to the wooden crate with self-tapping screws. You can also use a metal crate, because self-tapping screws drill through the metal when screwing in. For the roof, hardware is used manufactured by Hilli, EKT, SFS, Fischer, the diameter of which should be 4, 8, 5.5, 6.3 mm, with a length of 19-250 mm. You can also buy products from domestic manufacturers with a diameter of at least 6.3 mm.
The selection of self-tapping screws and their number for the roof is made so that the length of the threaded part of the screw is greater than the length of the package to be connected, at least 3 mm.
When buying self-tapping screws, you need to take into account their quantity with a margin, as well as their quality. The installation of high quality self-tapping screws can be done without previously drilled holes. With the correct method of fixing them and calculating the amount of corrugated board, they are used both for roofing roofs and for walls inside and outside the building.
There are three main commonly used types of corrugated board:
Roofing has a great height and is used for roofing the roof. Wall - with less volume. Carrier - used for load-bearing structures due to its great thickness. Moreover, the forms are completely different and require a special approach to fastening.
Rules for fixing corrugated board
An example of the correct screwing in of self-tapping screws. When manually tightening, it is necessary to control the effort so that it does not overtighten (this is fraught with damage to the insulating layer).
For fastening, a properly prepared surface must be present. The corrugated board is attached at the point where the trapezium wave of the corrugated board adheres to the crate. With this method, there is no lever between the point of imposition of forces on the screw and the attachment point. To reduce the wind loads of each trapezoid wave, the corrugated board is attached to the lower and upper purlins, and from the side of the wind bar they are attached to each purlins. Profiled decking with a width of 1100 mm and a length of 8000 mm with a lathing step of 500 mm requires a distance between screws of no more than 500 mm. Conclusion: at the top there are 2 screws, at the bottom 2, plus the wind side - 16 pieces. In total, we need 20 self-tapping screws per sheet of material. Before installation, a hole is drilled in the profiled sheet 0.3-0.5 mm larger than the diameter of the screw. Screws are screwed at an angle of 90 degrees. This is necessary to eliminate the possible appearance of through holes in the roof.
- Drills - only with low rpm chuck.
- The screwdriver is a simple and reliable manual method.
Using any other or these tools requires a lot of skill and safety.
Laying of corrugated board with a thickness of 0.5 to 1 mm and a length of 2 to 12 meters begins from the right or left end. At the edges, the profiled sheet should protrude 40 cm. We install the first profiled sheet and fix it with one screw on the ridge. Then we attach the second one to the ridge with one screw. All the time we make sure that the edges of the sheets lie on one line and the profiled sheet does not skew. At the top of the wave, we fasten the overlap of the sheets with one screw. Thus, we attach the other three sheets. After aligning their bottom edge, we firmly fasten them along the entire length. A horizontal overlap of sheets is allowed from 10 cm. Thus, from 4 to 8 screws are consumed per 1 m2.
Features of installation of wall sheeting
Mounting it to the wall starts from the right corner. Before installing on the wall, check the surface for unevenness. Then we fix a wooden lathing or crossbar. To ensure good sheet adhesion and good fastening, the distance of the crossbar is controlled. It should be about 0.5 mm. The subsequent profiled sheet is attached to the previous one with an overlap. Thus, the capillary groove of the first profiled sheet is covered. During work, careful control is required to avoid distortions. At the bottom, you need to leave a gap of 2 to 4 cm for ventilation of the space under the corrugated board. If desired, the space between the profiled sheet and the crate is filled with thermal insulation or sound insulation. We start fixing the corrugated board from the bottom corner and go to the top. During fastening, a minimum distance must be left between the screws and the supporting structure. With the dimensions of the profiled sheet 1250 mm wide and 10,000 mm long, 45 screws are required. On average, a profiled sheet of 1 m 2 requires from 5 to 8 pieces.
Here is another way to calculate the number of self-tapping screws for attaching a profiled sheet
Take the layout of the corrugated board. For example, a profiled sheet 1000 mm wide, 12 200 mm long. In each case, you need to know exactly the data in order to avoid inaccuracies. The profiled sheet is attached to the extreme supports with each wave and through one wave - to the intermediate ones. The sheets are fastened together with self-tapping screws with a distance of 1 m from the support, the pitch of which is 250, 500 and 1000 mm. We will multiply the number of sheets, add extreme hardware plus a percentage for scrap. We count the bottom screws. The total is 6-9 pieces per 1 m 2.
http://kryshikrovli.ru
When calculating the number of necessary parts, it is imperative to take into account the impact of the external environment and atmospheric phenomena. The more dangerous they are, the more screws will be required for mounting the roof. And you also need to take into account the thickness and dimensions of the parts in order to hedge the appearance of defects in the work. The hardest thing is to calculate how many parts will be needed for 1m 2. Below are several calculation methods that will help answer this question.
Basically, 1m 2 of profiled sheet requires from eight to nine self-tapping screws. Guided by these data, you can easily calculate how many parts are needed to install the entire roof.
We take the length of one sheet of material and subtract the transverse overlap, which is 15 to 20 cm. The resulting value must be multiplied by the useful width of the sheet. Thus, we get the working area of \u200b\u200bone sheet of material. Then we multiply the resulting figure by 9 and the result is the approximate number of screws we need for the roof for 1m 2.
From the above calculations, we consider the total number of parts required to install the entire roof. These calculations have already taken into account those self-tapping screws that will be required for the installation of cornices, chimneys, ventilation systems and other important elements.
2 way
It is necessary to take a plan for the installation of a profiled sheet. For example, material: width - 100 cm, length - 1 220 cm. It is required to approach very responsibly in determining the size of the material in order to prevent errors. Each extreme wave is mounted, and the intermediate ones - through the wave. Profiled sheets are fastened between themselves with self-tapping screws every 25, 50 and 100 cm. It is required to multiply all the profiled sheets, taking into account the edges and possible damage to the material. We consider the screws that will be located below. The result is about 6-9 pieces. for 1m 2.
3 way
It is necessary to add the reliability factor (one or two parts), as well as the margin (one or two parts) to the very minimum value of the screws. Defective products, loss of work and more are in stock. As a result, we find that about 6-8 self-tapping screws are required for 1m 2 of material.
When buying self-tapping screws, you do not need to count every little thing, because each part has its own weight. There is a size ruler, which indicates the weight of the screw. For example, 1000 pcs. parts with a diameter of 4.8 mm and a length of 25 mm weighs three and a half kilograms, when 1000 parts with a diameter of 6.3 mm and a length of 152 mm: 45 kilograms. Because of this, manufacturers pack up small self-tapping screws for the roof in packages of one hundred, two hundred, two hundred fifty, five hundred, one thousand, two thousand and six thousand pieces, and the largest number of parts of huge self-tapping screws is one thousand pieces.
Choose self-tapping screws and the required number of them in such a way that the length of the thread of the screw part is at least three millimeters longer than the length of the connecting package.
In the event that the self-tapping screws are purchased of high quality, then their installation can be carried out without first making holes.
There is another option for determining the quantity required material: you can build on the recommendations of the manufacturer. For each building material, fastener standards are prescribed. It is they who determine how many self-tapping screws are required for 1m 2 of professional sheet for the roof. If the recommended number of parts is violated, then it will be impossible to make claims for the formation of various kinds of defects and damage.
Because of this, it is worth carefully studying the packaging. building materials and follow the manufacturer's suggested values. Many suppliers have an established manufacturing process in such a way that they themselves are engaged in the production of fasteners. Because of this, a reasonable option would be to purchase a whole set: profiled sheet, fasteners and additional elements.
There are established standards for the consumption of fasteners for different kinds materials. But this does not mean that you need to strictly follow them, since the norm is the minimum. therefore the best way - buy more, as they say "in reserve", you never know where it breaks, is lost or found a marriage.
Based on the above methods for determining the number of screws for work, we can conclude: the average consumption of screws per 1m 2 is 6-9 pieces.
This value can vary depending on various factors. For example, if the roof is installed with a gentle slope. With an increase in the angle of inclination, the likelihood of a threat of wind increases, so it is required to increase the number of fasteners.
Watch this video, from which you will find out how many screws are required for 1m2.
Fastening profiled flooring and calculation of self-tapping screws
All of us during the roofing with profiled flooring (corrugated board) faced the questions: how many self-tapping screws are needed and how to fix it correctly, what is the consumption of self-tapping screws per 1 m 2 of profiled sheet and how to choose them correctly.
The scheme of fastening the profiled sheet to the roof with self-tapping screws. The number of self-tapping screws that are needed per square meter of coverage is from five to six pieces when installing the fence and from six to eight for the roof.
When fastening a profiled sheet, you need to take into account its thickness, dimensions, for a better connection and to avoid unnecessary consequences. In this article, we will analyze how to correctly calculate the number of self-tapping screws and for which profiled sheets it is correct to use them.
When equipping roofs with profiled decking, the correct selection of length is required, so that it is larger than the roof slope. We fasten the corrugated board to the wooden crate with self-tapping screws. You can also use a metal crate, because self-tapping screws drill through the metal when screwing in. For the roof, hardware is used, produced by Hilli, EKT, SFS, Fischer, the diameter of which should be 4, 8, 5.5, 6.3 mm, with a length of 19-250 mm. You can also buy products from domestic manufacturers with a diameter of at least 6.3 mm.
The selection of self-tapping screws and their number for the roof is made so that the length of the threaded part of the screw is greater than the length of the package to be connected, at least 3 mm.
When buying self-tapping screws, you need to take into account their quantity with a margin, as well as their quality. The installation of high quality self-tapping screws can be done without previously drilled holes. With the correct method of fixing them and calculating the amount of corrugated board, they are used both for roofing roofs and for walls inside and outside the building.
There are three main commonly used types of corrugated board:
- roofing;
- wall;
- carrier.
Roofing has a great height and is used for roofing the roof. Wall - with less volume. Load-bearing - used for load-bearing structures due to its large thickness. At the same time, the forms are completely different and require a special approach to fastening.
Rules for fixing corrugated board
An example of the correct screwing in of self-tapping screws. When manually tightening, it is necessary to control the effort so that it does not overtighten (this is fraught with damage to the insulating layer).
For fastening, a properly prepared surface must be present. The corrugated board is attached at the point where the trapezium wave of the corrugated board adheres to the crate. With this method, there is no lever between the point of imposition of forces on the screw and the attachment point. To reduce the wind loads of each trapezoid wave, the corrugated board is attached to the lower and upper purlins, and from the side of the wind bar they are attached to each purlins. Profiled decking with a width of 1100 mm and a length of 8000 mm with a lathing step of 500 mm requires a distance between screws of no more than 500 mm. Conclusion: at the top there are 2 screws, at the bottom 2, plus the wind side - 16 pieces. In total, we need 20 self-tapping screws per sheet of material. Before installation, a hole is drilled in the profiled sheet 0.3-0.5 mm larger than the diameter of the screw. Screws are screwed at an angle of 90 degrees. This is necessary to eliminate the possible appearance of through holes in the roof.
- Drills - only with low rpm chuck.
- The screwdriver is a simple and reliable manual method.
Using any other or these tools requires a lot of skill and safety.
Laying of corrugated board with a thickness of 0.5 to 1 mm and a length of 2 to 12 meters begins from the right or left end. At the edges, the profiled sheet should protrude 40 cm. We install the first profiled sheet and fix it with one screw on the ridge. Then we attach the second one to the ridge with one screw. All the time we make sure that the edges of the sheets lie on one line and the profiled sheet does not skew. At the top of the wave, we fasten the overlap of the sheets with one screw. Thus, we attach the other three sheets. After aligning their bottom edge, we firmly fasten them along the entire length. A horizontal overlap of sheets is allowed from 10 cm. Thus, from 4 to 8 screws are consumed per 1 m2.
Installation of roofing and wall materials made of profiled metal requires the use of special types of fasteners.
Self-tapping screws for profiled sheet differ in design from standard fasteners.
Design and appearance features
Even a layman can distinguish special self-tapping screws for attaching a profiled sheet in appearance.
The main distinguishing features of this fastener are as follows:
- Due to the fact that these self-tapping screws are intended for fastening profiled metal coatings with polymer coatings, manufacturers offer a wide range of colors of fasteners corresponding to various colors of the profiled sheet. This makes the fasteners less visible and increases the aesthetic value of the structure. In addition, such a coating of the self-tapping screw provides additional protection against weathering.
- For the production of self-tapping screws, durable carbon or stainless steel is used, which significantly increases the service life of the fastener.
- The tip of the self-tapping screw is made in the form of a drill (drill) that allows tightening without preliminary drilling of the profiled sheet.
- Due to the fact that a significant torque acts on the self-tapping screws for fastening the profiled sheet at the time of installation, the use of screwdriver heads (Phillips or straight) is not practiced. These self-tapping screws have a hexagonal bolt head; they are tightened with a special nozzle using a screwdriver or other power tool.
- In order to prevent moisture from getting under the screw head (this is especially important when installing the roof), the fasteners are completed with a metal washer with a neoprene gasket, which seals the hole created when screwing.
Varieties of self-tapping screws for profiled sheet
All existing self-tapping screws for a profiled sheet can be divided into three main categories:

Dimensions of screws
Self-tapping screws of various sizes are used to fasten the profiled sheet. In this case, the parameters of the fasteners should be determined based on the value of the expected load.
The manufacturer offers the following sizes of self-tapping screws for the profiled sheet:
- Diameter 4.8-6.3 mm. Thicker self-tapping screws must be used to fasten a profiled sheet based on galvanized steel (0.5-0.6 mm) with a more powerful polymer coating... The weight of such a sheet is significantly greater.
- The length of the screws can vary from 19 to 250 mm. Their choice is based on the thickness of the materials to be joined, the shape of the profile. It is believed that the fasteners should be 3-5 mm longer than the total thickness of the parts (excluding the drill), this provides a more reliable fastening.
Calculation of the required number of screws
First of all, you need to look at the manufacturer's recommendations. It is he who determines how many screws per 1 m 2 of the profiled sheet are required. In case of violation of the standards required by the manufacturer, it will not be possible to present him with claims in the event of a structural failure. Therefore, build on the values \u200b\u200bsuggested by the supplier, do not save on the number of fasteners.
The average need for fasteners is 5-6 units per square meter of surface.
But this value can change in different conditions:
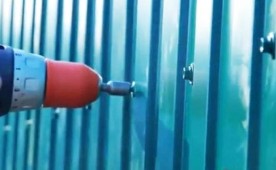
Installation rules
Before installation, it is necessary to make sure that the profiled sheet adheres throughout the entire area to the supporting structures.
When tightening self-tapping screws, the following rules must be observed:
- The self-tapping screw must be screwed in strictly perpendicular to the sheet. Any misalignment will lead to a violation of the sealing, which is especially important when installing the roof.
- When screwing in the self-tapping screw, it is not allowed to pinch and deform the pressure washer with a neoprene gasket. It is necessary to tighten with such force as to only press the washer.
- The installation step of self-tapping screws must comply with the manufacturer's recommendations.
It is the self-tapping screws for the profiled sheet that are able to guarantee high-quality fastening of coatings on any objects.
Most manufacturers have also set up production of their own fasteners, so it is advisable to purchase a complete set of sheets, fasteners and additional elements.
This, subject to the installation technology, will ensure the maximum quality of the coating.