They make it possible to perform various tasks in the field of the construction industry.
When driving pile pillars, it is necessary to control the quality of the work performed, compliance with all project requirements, including tolerances installed piles (SNiP 2.02.03-85 and SNiP 3.02.01-87).
Reinforced concrete piles
The type of piles depends on several parameters:
- From the material for their manufacture are from concrete, reinforced concrete, metal and wood.
- By the shape of the rod: square, rectangular (solid or hollow), round, with an annular section.
- On the method of mounting piles: screw, driven, bored.
When preparing for the installation of a pile structure, a number of factors must be taken into account:
- Geological characteristics of the construction site and technical specifications equipment used;
- Hydrometeorological conditions at the time of work, especially with bored piles;
- Layout of electrical cables in the work area, underground structures, nearby buildings in order to prevent their damage.
What errors can occur when installing piles
Serious errors can occur when installing piles yourself. To prevent this, you should figure out where problems can arise.
- The first thing you need to pay attention to is the wrong location. It is necessary that the installation takes place specifically along the intended line of the foundation placement scheme. That is, the piles may not be located in a straight line, but deviated to the left or right of the axis. Improper placement can lead to uneven load distribution and further subsidence or distortion of the building.
- The next mistake is the deviation of the vertical position of the mounted structure. If the rod is tilted even at a small angle relative to the vertical axis, then this is a gross violation. This error cannot be corrected with further immersion. The verticality of the structure must be constantly monitored, starting from the first stage and up to the stop point.
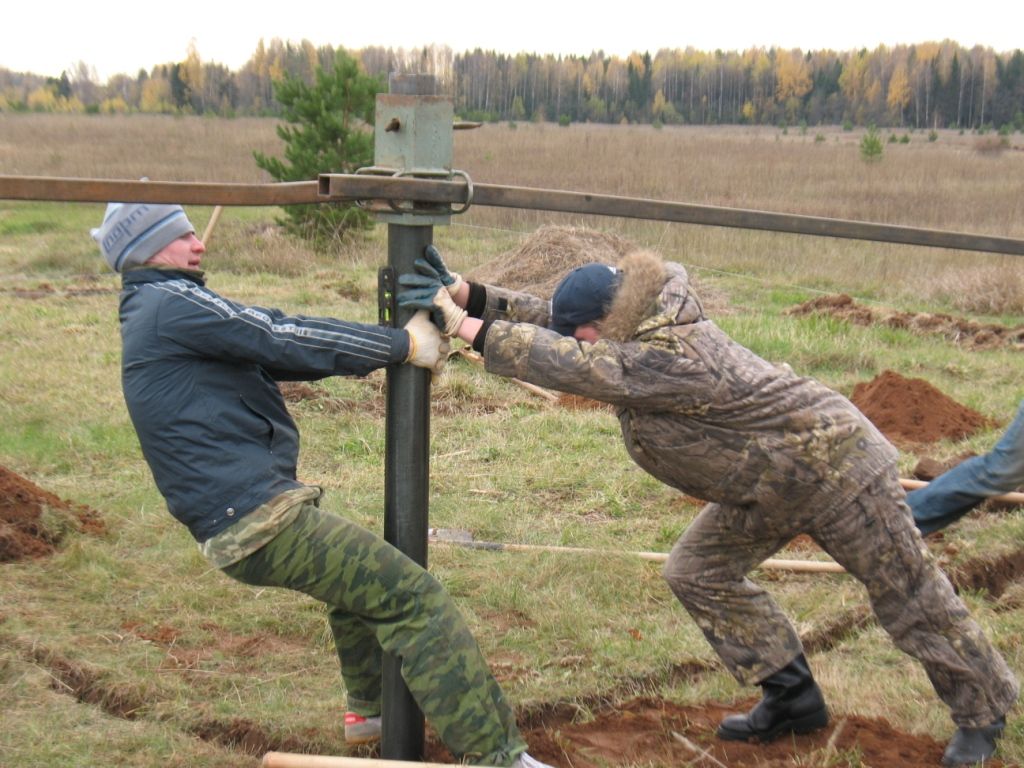
The permissible vertical deviation of the pile is up to 2 degrees. Otherwise, a placement error will lead to instability of the structure, which will cause a loss of its rigidity.
- Errors are often made when leveling bars horizontally. Some, simplifying their work, align the horizontal by unscrewing the pillars. It is correct to do this by cutting off the excess length with a grinder. When unscrewing the pile, the degree of rigidity is lost. This is fraught with subsidence of the structure, instability and unsteadiness.
- If the pillars are not submerged to the required depth, then this also entails a gross error. A correctly installed pile is when its base rests against that high-density soil. This is what provides the structure with high rigidity and increases its bearing capacity.
The pile should be screwed in to a depth equal to the depth of freezing of the soil plus 10–20 cm. On clay and peat soils until it fully rests on solid soil layers.
- The next mistake, refusal to pour concrete on the pillars. In this case, moisture will accumulate in its cavity, which will lead to rust and the destruction of the structure.
- Placing piles in relation to each other at a distance of more than three meters is also a gross mistake.
Tolerances
Twisting the pile
Unlike others, the installation of piles according to its technology involves some deviations from the design indicators in the horizontal and vertical planes. The gradual screwing in of the piles requires constant checking of all levels.
Even if the structure is aligned perfectly at the beginning of the process, deviations may occur at any time during immersion. The reason for this may be soil heterogeneity or any other obstacle.
When carrying out work on the installation of piles, you should constantly monitor the levels. It is necessary to take into account the possibility of deviations from the axis, so that they do not exceed the tolerances.
Here are some indicators of permissible deviations when deepening piles. During the installation of rectangular and square rods, hollow, as well as round driven rods with a diameter of less than 50 cm, permissible deviations when located in one row are along the row axis - 0.3d, across - 0.2d (d is the diameter of a pile with a circular cross-section or length the smaller side of the bar rectangular). For single rods - 5 cm, for columns - 3 cm.If the rods are arranged in several rows, in the so-called cluster or tape method, then the permissible deviations are:
- for the extreme: along the axis of the row - 0.3d, at the intersection of the row - 0.2d;
- for the rest: along the axis of the row - 0.3d, at the intersection of the row - 0.3d.
Deviations for hollow cores with a diameter of 0.5-0.8 m and bored piles with a diameter exceeding 0.5 meters:
- with tape placement: along the axis of the row - 15 cm, at the intersection of the row - 10 cm;
- with bush placement: along the axis of the row - 15 cm, at the intersection of the row - 15 cm.
For hollow round rods for columns, the permissible deviations are 8 cm.
The total number of piles with deviations from their number under the project should not exceed:
- with tape placement - no more than a quarter of all piles used;
- with piles - 5% of all installed piles.
Such deviations are not considered critical and are almost completely eliminated during the installation of the piping or attachment of the heads. The vertical placement of the rods needs to be done much more accurately.
Deviations in the placement of bored piles
Bored piles are poured after studying the soil, transferring the layout and preparation of wells to the site. The volume of the well must be up to 10% of the volume of the casing that is lowered into the well. Watch the video on how to place piles without errors.
The volume of the casing is calculated by the outside diameter.
The level of penetration into a solid layer of soil ranges from 20 cm to 50 cm. The greater the density of the soil, the shallower the depth. The tolerances for the placement of bored piles in the absence of design ones are:
- tape placement: across the row - 0.2d, but should not exceed 0.1 m, along the row - 0.3d, but not more than 0.15 m;
- cluster placement - in both types 0.3d, but not more than 0.15 m;
- single piles for columns - 0.15d, but not more than 0.08 m.
If wells are drilled on soft soils or in the presence of a large accumulation groundwater, then casing drilling mechanisms should be used. In the absence of such, the walls of the wells are strengthened with a pressure of water with high pressure. This method is used away from buildings. The distance should be at least 35–40 meters. If these conditions are impracticable, then a clay solution is used to strengthen the walls of the wells. The bases of the wells are strengthened by mounting a branch pipe with a length of at least two meters. After preparing the well, it is protected from the possibility of ingress of foreign objects, water or snow. It is impossible to leave the well without concreting for a long time. This process must be carried out within 24 hours, and in soft soils subject to sediment, downtime should not exceed 8 hours.
If the filling time is overdue, it is necessary to re-survey the wells.
Tongue deviation

Let us now consider what deviations of the sheet pile exist and how to eliminate them.
- Roughness is the deviation of the tongue from the vertical level in the plane of the alignment. Forward angling usually occurs when one or more dowels are driven to full depth. It increases with the hammering of each subsequent tongue. To eliminate the deviation of the fan, it is necessary to shift the driving mechanism from the center of gravity of the submerged sheet pile in the opposite direction of the deviation by 10–20% of the width of the sheet pile. With small deviations, fanning can be eliminated by pulling the tongue and groove during its deepening in the opposite direction of the deviation direction. If its indicator exceeds the tolerances, then it is eliminated by using wedge-shaped dowels. The wedge shape of the tongue (the ratio of the difference between the width of the lower and upper parts to its length) should be up to 0.5%.
- Out-of-alignment is a deviation from the vertical level in the plane perpendicular to the alignment. It usually occurs when there is insufficient tracking of the vertical level of the tongue placement. This can happen even at the initial stage of laying, when its length above the zero level is large enough. The reasons for the dragging of the tongue from its vertical position may be different. This is the insufficient rigidity of the guide device, the pressure of the cable from the crane to the upper end of the tongue in the horizontal direction, or in the elementary presence of any obstacles in the ground. If this deviation does not exceed the design norm, then it can be straightened when the subsequent sheet piles are immersed by pulling the cable in the direction opposite to the deviation. If it exceeds the tolerance, then it should be removed and the dive should be made again, observing all levels
Deviation of sheet pile by immersion level
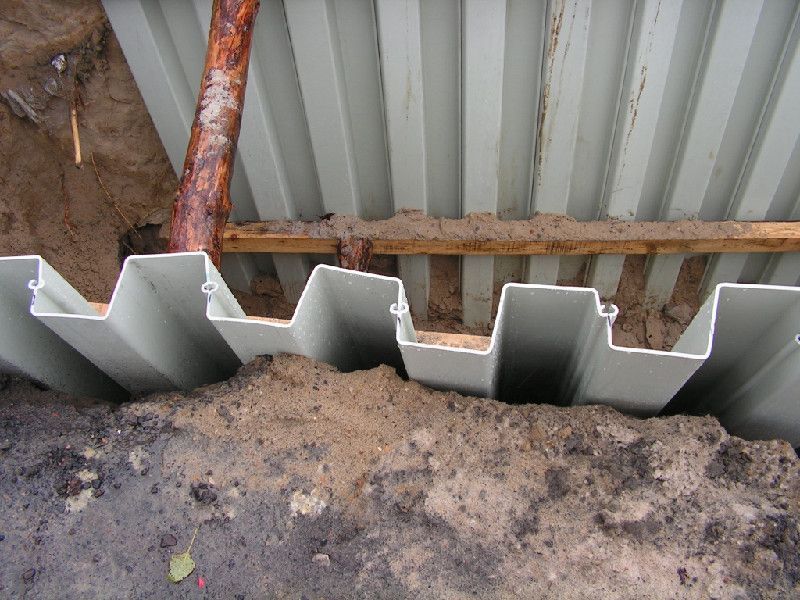
The drift of the sheet pile below the design mark due to the immersion of the adjacent sheet pile occurs when the adjacent sheet pile deepens due to the high resistance in the lock. To prevent such a deviation, it is necessary to connect the previously immersed dowels to the design mark by welding or connecting bolts. Plunging the sheet pile to insufficient depth due to obstacles in the ground or strong friction in the locks. The way to eliminate such a deviation is to raise several submerged sheet piles by 0.5–0.8 m and then submerge them back to the required depth. If the reason is due to the presence of a foreign object, then the deepening of the problem groove should be stopped and proceed to the immersion of subsequent structures. After their successful immersion, we return to the problem sheet pile and immerse two adjacent sheet piles along its guides.
If the deviations of the tongue and groove cannot be eliminated by all of the above methods, it is necessary to resolve this issue together with the design organizations.
Quality control of pile installation
The quality of the installation of the pile supporting structure should be monitored throughout the entire process of work. It is affected by:
- The quality of the material used in the installation of the structure;
- Strict compliance with all approved rules for driving piles;
- Correct placement of pile rods according to the project;
- High-quality work when deepening piles;
- Control of ensuring high strength of the pile foundation.
Of all these areas, the last is non-standard. To perform this control, two methods are used: statistical and dynamic. For printed - only statistical.
Statistical way
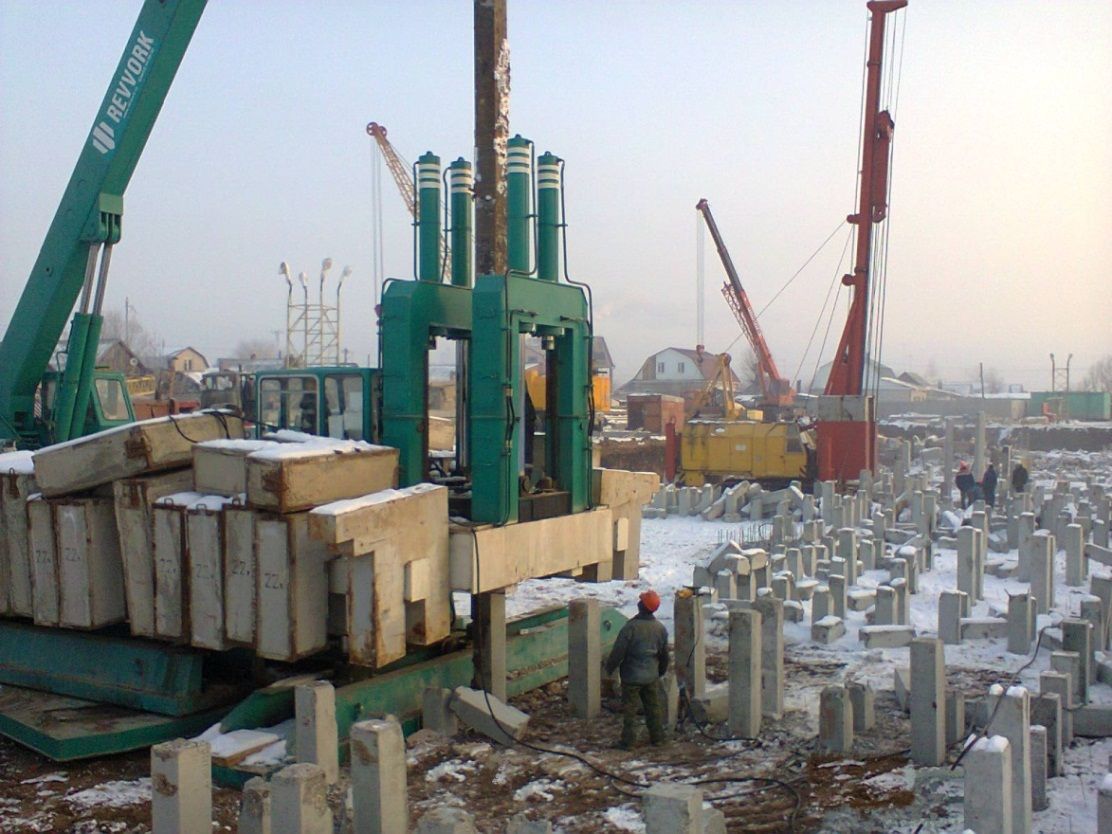
The statistical method for controlling the bearing capacity is used after the installation of the pile structure has been completed, before further work on the construction of the future building begins. To do this, it is necessary to load the structure with a certain load or to provide pressure on it using a hydraulic press until a slight movement appears.
Based on the exerted effort, a conclusion is made about the bearing capacity of the pile. This method is quite reliable, but it requires a lot of effort and wasting time (from 4 to 12 days). Therefore, it is mainly used to control the quality of bored piles.
Dynamic way
The dynamic method is a conditional assessment of the bearing capacity of pile rods by the failure rate. To determine it, use different ways... For example, the use of a refusal meter - a device with a scale with pointers moving along it. This device is placed directly on the ground or attached to a pile. During the deepening of the pile, one of the rods moves. Its position indicates the value of the residual failure. During a slight backward movement of the pile, the second pointer moves up and indicates the elastic failure value.
When performing quality control of the pile installation, you should constantly monitor that the deflection of the piles does not exceed the design tolerances.
Construction control
Scope of operations and controls
Preparatory work | Verify: | General work log, act of acceptance of previously performed work, passports (certificates) | |
- availability of acts for previously performed work; | Visual | ||
- correct installation and reliability of fastening the formwork, supporting scaffolding, fasteners and scaffolding; | Technical inspection | ||
- readiness of all mechanisms and devices that ensure production concrete works; | Visual | ||
- cleanliness of the pile heads, the previously laid concrete layer and the inner surface of the formwork; | Also | ||
- the presence of grease on the inner surface of the formwork; | Also | ||
- the state of fittings and embedded parts, their compliance with the design; | Technical inspection, measuring | ||
- a leader of the design elevation of the top of the concreting on the inner surface of the formwork. | Measuring |
Concrete laying, concrete hardening, stripping | Control: | General work log | |
- the quality of the concrete mix; | Laboratory | ||
- the state of the formwork; | Technical inspection | ||
- the height of the dumping of the concrete mixture, the thickness of the layers to be laid, the step of rearranging the deep vibrators, the depth of their immersion, the duration of vibration, the correctness of the working seams; | Measuring, 2 times per shift | ||
- temperature and humidity conditions of concrete hardening; | Measuring, in places of certain PPR | ||
- the actual strength of the concrete and the timing of stripping. | Measuring at least once for the entire volume of stripping |
Acceptance of completed works | Verify: | Acceptance certificate of work performed, executive geodetic scheme | |
- the actual strength of the concrete; | Laboratory | ||
- the quality of the grillage surface, the geometric dimensions of the grillage, compliance with the design position of the entire structure; | Visual, measuring, every structural element | ||
- the quality of the materials used in the construction. | Visual |
Control and measuring tool: plumb bob, tape measure, metal ruler, level, theodolite, two-meter rail, tacheometer. |
Operational control is carried out: foreman (foreman), construction laboratory engineer, geodesist - in the process of performing work. Acceptance control is carried out: quality service workers, foreman (foreman), surveyor, representatives of the customer's technical supervision. |
Note: the operational control of the surveyor during the concreting process is possible only for the purpose of monitoring deformations, the formwork adjustment at this moment is unacceptable, because affects the change in the continuity of the concrete mixture and the formation of voids in it. |
Technical requirements and limit deviations
SNiP 3.02.01-87 " Earthen structures, bases and foundations. ", Table 18 (excerpts from the table) or SP 45.13330.2012" Earthworks, foundations and foundations. ", Table 12.1 (excerpts from the table),
SNiP 3.03.01-87 "Bearing and enclosing structures", table. 11 or SP 70.13330.2012 "Bearing and enclosing structures", table. 5.12
5. Size of the cross-section of the grillage | +6 mm; -3 mm | Also |
(from the joint venture) at the size< 200 мм | +6 mm | |
(from joint venture) at size \u003d 400 mm | +11 mm; -3 mm | |
(from the joint venture) with a size\u003e 2000 mm | +25 mm; -9 mm | |
(from SP) intermediate sizes are interpolated |
SP 70.13330.2012 "Bearing and enclosing structures", Table X.1 - Classes concrete surfaces
A3 | 2 | 4,5 | 7 | 9,5 |
A4 | 3 | 7,5 | 10,5 | 14 |
A6 | 5 | 10 | 12 | 15 |
Requirements for the quality of materials
GOST R 52085-2003 "Formwork. General specifications." (excerpts)
6.2.5 Round timber should be used for timber bearing and supporting elements conifers I - II grade according to GOST 9463 "Round timber of coniferous species. Technical conditions", table. 2 (excerpts from the table),
coniferous sawn timber of I - II grade according to GOST 8486 "Softwood sawn timber. Technical conditions".
6.2.6 Faced (laminated) birch plywood shall be used for formwork decks of the 1st and 2nd classes; for class 2, combined veneered plywood can also be used; for the 3rd class - softwood sawn timber in accordance with GOST 8486 "Softwood sawn timber. Specifications" and hardwood according to GOST 2695 "Hardwood sawn timber. Technical conditions" not lower than grade II, chipboards according to GOST 10632 "Chipboards. Specifications ", fibreboards according to GOST 4598" Fiber boards. Specifications ", bakelized plywood according to GOST 11539" Bakelized plywood. Specifications ", FSF plywood according to GOST 3916.1" General purpose plywood with outer layers of hardwood veneer. Specifications ", GOST 3916.2" General purpose plywood with outer layers of coniferous veneer. Specifications "and other materials.
Note - the grades of timber and sawn timber are determined depending on the number and size of wood defects (knots, rot, etc.) according to the above-mentioned GOSTs.
GOST 23478-79 "Formwork for the construction of monolithic concrete and reinforced concrete structures. Classification and general technical requirements"(GOST is not valid in the Russian Federation)
4.14 Deck boards should have a width of not more than 150 mm, the moisture content of the wood used for the deck should be no more than 18%, for supporting elements - no more than 22%.
4.20 The formwork elements must fit snugly together during assembly. Slots in butt joints should not be more than 2 mm.
GOST 10922-2012 "Reinforcement and embedded products, their welded, knitted and mechanical joints for reinforced concrete structures. General specifications", p. 5.3, table. 1 (excerpts from the table)
5.6 On the elements of reinforcement products and embedded parts, there should be no peeling rust and scale, as well as traces of oil, bitumen and other contaminants.
GOST 23279-85 "Welded reinforcing meshes for reinforced concrete structures and products. Specifications"
3.15 Maximum deviations from the straightness of the mesh rods should not exceed 6 mm per 1 m of the mesh length.
GOST 7473-2010 "Concrete mixtures. Specifications."
8.2 Prior to the start of delivery of concrete mix of a given quality, the consumer has the right to demand from the manufacturer (supplier) information on the quality of the materials used and the nominal composition of the concrete mix, as well as the results of preliminary tests of the concrete mix of this nominal composition and concrete for all indicators specified in the supply contract. This information is presented in the cards for the selection of the concrete composition.
8.4 When supplying ready-mixed concrete of a given quality, the manufacturer (supplier) must provide the consumer in a printed and certified form with the following accompanying documentation:
- for each batch of concrete mix - a document on the quality of the concrete mix and a test report for determining the standardized indicators of concrete quality;
- for each load of concrete mix - consignment note;
- additionally (if specified in the supply contract), the manufacturer must provide the consumer with information in accordance with 8.2.
8.5 When supplying ready-mixed concrete of a given composition, the manufacturer must provide the consumer in a printed and certified form with the following accompanying documentation:
- for each load of concrete mix - a waybill and a document on the quality of the concrete mix;
- for each batch of concrete mix - copies of passports for the materials used;
- additionally (if specified in the supply contract), the manufacturer must provide the consumer with protocols for determining the quality indicators of the concrete mix and concrete.
Work instructions
SNiP 3.03.01-87 "Bearing and enclosing structures" pp. 2.8 - 2.13, 2.100, 2.109, 2.110 or SP 70.13330.2012 "Bearing and Fencing Structures" p. 5.3.1 - 5.3.15, 5.17.1, 5.17.4-5.17.8
Before concreting, the base must be cleaned of debris, dirt, oils, snow, ice, cement film, after which the cleaned surfaces must be rinsed with water and dried with a stream of air. Reinforcement, correct installation and fastening of the formwork must be accepted according to the act. Reinforcement of the grillage should be carried out according to the project. Installation and acceptance of the formwork, stripping must be carried out according to PPR. Concrete mixes should be placed in the structure in layers of the same thickness. When compacting the concrete mixture, it is not allowed to rest the vibrators on reinforcement, embedded products, formwork fastening elements. The depth of immersion of the deep vibrator into the concrete mixture should ensure its deepening into the previously laid layer by 5 - 10 cm, the permutation step should not exceed one and a half radius of its action. The height of the free throwing of the concrete mixture into the formwork should not exceed 3 m. Laying the next layer of the concrete mixture is allowed before the concrete of the previous layer begins to set. The upper level of the laid concrete mix should be 50 - 70 mm below the top of the formwork panels. The thickness of the layers of concrete to be laid should not exceed 1.25 of the length of the working part of the vibrator. The surface of the working joints, which are made during the laying of the concrete mixture at intervals, must be perpendicular to the axis of the grillage within the middle third of the span. The resumption of concreting is allowed to be carried out when the concrete reaches a strength of at least 1.5 MPa. Measures for the care of concrete, control over their implementation and the timing of demoulding should be established by the PM. The minimum concrete strength when removing the grillage must be at least 70% of the design.
to homeThis fact testifies to a violation of the requirements of SNiP 3.03.01-87 LOADING AND GUARDING STRUCTURES, table 11, according to which the maximum deviations of the location of the anchor bolts in the plan within the contour are 5 mm.
SNiP 3.03.01-87 LOADING AND GUARDING STRUCTURES RECEPTION OF CONCRETE AND REINFORCED CONCRETE STRUCTURES OR PARTS OF STRUCTURES
2.113. Requirements for finished concrete and reinforced concrete structures or parts of structures are given in table. eleven.
Table 11
Parameter | Limit deviations | Control (method, volume, type of registration) |
1. Deviation of lines of planes of intersection from the vertical or design slope for the entire height of structures for: | ||
foundations | Measuring, |
|
walls and columns supporting monolithic coverings and ceilings | each structural element, work log |
|
walls and columns supporting prefabricated beam structures | ||
walls of buildings and structures erected in sliding formwork, in the absence of intermediate floors | 1/500 of the height of the structure, but not more | Measuring, all walls and lines of their intersection, work log |
walls of buildings and structures erected in sliding formwork, in the presence of intermediate floors | 1/1000 of the building height, but not more than 50 mm | |
2. Deviation of horizontal planes for the entire length of the verified area | Measuring, at least 5 measurements for every 50 100 m, work log |
|
3. Local irregularities of the concrete surface when checking with a two-meter rail, except for supporting surfaces | ||
4. Length or span of elements | Measuring, each element, work log |
|
5. Size of the cross-section of elements | ||
6. Marks of surfaces and embedded products that serve as supports for steel or precast reinforced concrete columns and other prefabricated elements | Measuring, each support element, executive circuit |
|
7. The slope of the supporting surfaces of foundations when supporting steel columns without grout | The same, every foundation, executive scheme |
|
8. Location of anchor bolts: | ||
in plan within the contour of the support | The same everyone |
|
foundation bolt, |
||
in height | executive scheme |
|
9. The difference in elevation at the junction of two adjacent surfaces | The same, each joint, executive scheme |
Expert opinion - according to the expert opinion, the elimination of these violations of the requirements of regulatory and technical documents is not possible without dismantling monolithic structures, since when installing support elements on an anchor, the arrangement of columns in compliance with the geometric parameters in accordance with the project is impossible. In the case of this arrangement of columns, there will be a redistribution of loads on the foundations.
Table 10
Parameter |
Parameter value |
|
1. Accuracy of formwork manufacturing: |
||
inventory |
According to working drawings and technical conditions - not lower than H14; h14; ± ---------- according to GOST 25346-82 and GOST 25347-82; for forming elements - h14 |
Technical inspection, registration |
pneumatic |
According to technical conditions |
|
2. Defectiveness level |
No more than 1.5% at normal control level |
Measuring according to GOST 18242-72 |
3. Accuracy of setting the inventory formwork: |
± _____ in accordance with GOST 25346-82 and GOST 25347-82 |
|
including: |
||
unique and special structures |
Defined by the project |
|
low-turnover and (or) non-inventory during the construction of structures, the surface of which is not subject to accuracy requirements |
By agreement with the customer may be lower |
|
for structures ready for painting without putty |
Differences in surfaces, including butt ones, no more than 2 mm |
|
for designs ready for wallpapering |
The same, no more than 1 mm |
|
4. Installation accuracy and surface quality permanent formwork- facing |
Determined by the quality of the cladding surface |
Measuring, all elements, work log |
5. Accuracy of the installation of fixed formwork, which serves as external reinforcement |
Defined by the project |
|
6. Formwork turnover |
GOST 23478-79 |
|
7. Deflection of the assembled formwork: |
Registration, work log |
|
vertical surfaces |
1/400 span |
Controlled when factory |
floors |
1/500 span |
tests and at the construction site |
8. Minimum strength of concrete of unloaded monolithic structures during surface stripping: |
Measuring according to GOST 10180-78, GOST 18105-86, work log |
|
vertical from the condition of maintaining the shape |
||
horizontal and inclined in flight: |
||
70% of the design |
||
80% of the design |
||
9. Minimum strength of concrete during stripping of loaded structures, including from overlying concrete (concrete mix) |
Determined by the PM and agreed with the design organization |
ACCEPTANCE OF CONCRETE AND REINFORCED CONCRETE STRUCTURES
OR PARTS OF STRUCTURES
2.111. When accepting finished concrete and reinforced concrete structures or parts of structures, the following should be checked:
compliance of structures with working drawings;
quality of concrete in terms of strength, and, if necessary, frost resistance, water resistance and other indicators specified in the project;
the quality of materials used in construction, semi-finished products and products.
2.112. Acceptance of finished concrete and reinforced concrete structures or parts of structures should be drawn up in the prescribed manner by an act of survey hidden works or an act of acceptance of critical structures.
2.113. Requirements for finished concrete and reinforced concrete structures or parts of structures are given in table. eleven.
Table 11
Parameter |
Limit deviations |
Control (method, volume, type of registration) |
1. Deviation of lines of planes of intersection from the vertical or design slope for the entire height of structures for: |
||
foundations |
Measuring, |
|
walls and columns supporting monolithic coverings and ceilings |
each structural element, work log |
|
walls and columns supporting prefabricated beam structures |
||
walls of buildings and structures erected in sliding formwork, in the absence of intermediate floors |
1/500 of the height of the structure, but not more |
Measuring, all walls and lines of their intersection, work log |
walls of buildings and structures erected in sliding formwork, in the presence of intermediate floors |
1/1000 of the building height, but not more than 50 mm |
|
2. Deviation of horizontal planes for the entire length of the verified area |
Measuring, at least 5 measurements for every 50 100 m, work log |
|
3. Local irregularities of the concrete surface when checking with a two-meter rail, except for supporting surfaces |
||
4. Length or span of elements |
||
5. Size of the cross-section of elements |
||
6. Marks of surfaces and embedded products that serve as supports for steel or precast reinforced concrete columns and other prefabricated elements |
Measuring, each supporting element, actuator circuit |
|
7. The slope of the supporting surfaces of foundations when supporting steel columns without grout |
The same, every foundation, executive scheme |
|
8. Location of anchor bolts: |
||
in plan within the contour of the support |
The same everyone |
|
foundation bolt, |
||
in height |
executive scheme |
|
9. The difference in elevation at the junction of two adjacent surfaces |
The same, each joint, executive scheme |
3. ASSEMBLING OF PREMIUM CONCRETE
AND CONCRETE STRUCTURES
GENERAL INSTRUCTIONS
3.1. Preliminary storage of structures in on-site warehouses is allowed only with appropriate justification. The on-site warehouse should be located in the area of \u200b\u200bthe assembly crane.
3.2. Installation of structures of each overlying floor (tier) of a multi-storey building should be carried out after the design fixing of all mounting elements and the concrete (mortar) reaching the monolithic joints of the supporting structures of the strength specified in the PPR.
3.3. In cases where the strength and stability of structures during the assembly process is ensured by welding the mounting joints, it is allowed, with the appropriate indication in the project, to mount structures of several floors (tiers) of buildings without monolithing the joints. At the same time, the project must provide the necessary instructions on the procedure for installing structures, welding joints and embedding joints.
3.4. In cases where permanent connections do not ensure the stability of structures during their assembly, it is necessary to use temporary erection connections. The design and number of ties, as well as the order of their installation and removal, should be specified in the PPR.
3.5. Grades of solutions used in the installation of structures for the device of the bed must be indicated in the project. The fluidity of the solution should be 5-7 cm at the immersion depth of the standard cone, except for cases specifically stipulated in the project.
3.6. The use of a solution, the setting process of which has already begun, as well as the restoration of its plasticity by adding water is not allowed.
3.7. Maximum deviations from the alignment of landmarks when installing prefabricated elements, as well as deviations of completed installation structures from the design position should not exceed the values \u200b\u200bgiven in table. 12.
Table 12
Parameter |
Limit deviations, mm |
Control (method, volume, type of registration) |
1. Deviation from the alignment of the installation guidelines of the foundation blocks and foundation nozzles with the risks of centering axes |
||
2. Deviation of the marks of the supporting surface of the bottom of the foundation glasses from the design ones: |
||
before the device of the leveling layer along the bottom of the glass |
||
after the device of the leveling layer along the bottom of the glass |
||
3. Deviation from alignment of landmarks (lines of geometric axes, edges) in the lower section of the installed elements with reference landmarks (risks of geometric axes or edges of underlying elements, risks of alignment axes): |
||
columns, panels and large blocks load-bearing walls, volumetric blocks |
||
curtain wall panels |
Measuring, each element, work log |
|
girders, purlins, beams, crane beams, trusses, trusses and trusses |
||
4. Deviation of the axes of the columns of one-story buildings in the upper section from the vertical with the length of the columns, m: |
Measuring, each element, geodetic executive scheme |
|
| 8 | 16 |
||
| 16 | 25 |
||
5. Deviation from alignment of landmarks (lines of geometric axes) in the upper section of the columns of multi-storey buildings with risks of alignment axes with the length of the columns, m: |
||
| 8 | 16 |
||
| 16 | 25 |
||
6. The difference in top marks |
||
columns or their support sites (brackets, consoles) of one-story buildings and structures with the length of the columns, m: |
||
| 8 | 16 |
||
| 16 | 25 |
||
7. The difference in the marks of the top of the columns of each tier of a multi-storey building and structure, as well as the top wall panels frame buildings within the verified area with: |
||
contact installation |
||
installation of beacons |
||
8. Deviation from alignment of landmarks (lines of geometric axes, faces) in the upper section of installed elements (girders, girders, beams, trusses, roof trusses and beams) on a support with reference landmarks (risks of geometric axes or faces of downstream elements, risks of alignment axes ) at the height of the element on the support, m: |
Measuring, each element, work log |
|
st. 1 to 1.6 |
||
| 1,6 | 2,5 |
||
| 2,5 | 4 |
||
9. Deviation from symmetry (half of the difference in the depth of support of the ends of the element) when installing girders, girders, beams, crane beams, trusses, trusses (beams), roof slabs and floors in the direction of the span to be covered with the length of the element, m: |
||
| 8 | 16 |
||
| 16 | 25 |
||
10. The distance between the axes of the upper chords of trusses and beams in the middle of the span |
||
11. Deviation from the vertical of the top of the planes: |
||
load-bearing wall panels and volumetric blocks |
Measuring, each element, geodetic executive scheme |
|
large blocks of load-bearing walls |
||
partitions, curtain wall panels |
Measuring, each element, work log |
|
12. The difference in the marks of the front surfaces of two adjacent unstressed floor panels (slabs) in the seam with the length of the slabs, m: |
||
| 8 | 16 |
||
13. The difference between the elevations of the upper flanges of crane beams and rails: |
Measuring, on each support, geodesic |
|
on two adjacent columns along a row with a distance between columns l, m: |
executive scheme |
|
on columns |
||
in span |
||
14. Deviation in height of the threshold of the doorway of the volumetric element of the elevator shaft relative to the landing site |
Measuring, each element, geodetic executive scheme |
|
15. Deviation from the perpendicularity of the inner surface of the walls of the elevator shaft relative to the horizontal plane (pit floor) |
Measuring, each element, geodetic executive scheme |
The designation adopted in table. 12: n is the ordinal number of the tier of columns or the number of panels installed in height.
Note. The depth of support of horizontal elements on bearing structures must be at least as specified in the project.