After installing the battens and securing waterproofing material the profiled sheet is mounted on the roof plane. The fixing process is very important, since the strength of the roof and its durability depend on it. Poor fastening leads to sheet displacement, corrosion and material deformation. How to properly fix the profiled sheet, and what screws should you use?
Basic principles of technology and requirements for self-tapping screws
The technology of fastening the profiled sheet consists of several stages:
- selection of roof fasteners;
- distribution of material along the roof slopes;
- fixing the profiled sheet with self-tapping screws;
- fastening of additional parts of the roof.
For the profiled sheet, you will need special screws. Conventional self-tapping screws with a round head and a sharp end are not suitable for this purpose, since they deform the surface of the sheet, which leads to the destruction of the polymer shell and corrosion. In addition, the head of an ordinary self-tapping screw is tightly pressed against the sheet, this prevents its natural deformation when heated from the sun. As a result, the coating surface can warp and come off the base. If the screw is not twisted, water will enter the hole. You can avoid this by treating each breakdown site with silicone, but over time, such fasteners will still loosen and allow moisture to pass through.
All these nuances were taken into account when creating a special type of self-tapping screw, called "roofing".
A sheet of corrugated board is a fairly light material. It is made of zinc plated steel and coated with a protective polymer. It can be attached to a lightweight crate, but it should be borne in mind that this material tends to sail.
The roofing screw has a hexagon head and a drill-shaped point. The peculiarity of the hex head is that the force for tightening it is several times less than that of a conventional one. The drill-shaped tip does not bite the surface and easily penetrates the sheet. These conditions allow you to accurately and with minimal damage to fasten the corrugated board.
Another feature of the special self-tapping screw in the device for securing thin metal. For this purpose, the design of the screw is reinforced with a protrusion and equipped with a washer with a rubber gasket - a seal. This shape allows you to maintain the shape of the screw when screwing it in and carefully close the attachment point. Rubber, silicone or neoprene gaskets absorb the deforming effect of solar heat on the corrugated board. Therefore, even with strong heating, natural deformation will not warp the metal.
Types of roofing screws
Roofing screws are made of several types of metal:
- stainless steel;
- carbon steel;
- zinc coated carbon steel;
- acid resistant steel.
The screw heads can be enameled to match the color of the roof material or not painted.
The length and width of the self-tapping screws may also vary, but the heads of all fit a dozen turnkey heads. The thickness varies from 4.5 to 6.3 millimeters, the length is from 19 to 152 millimeters. For fastening the ridge elements, screws with a length of 80 millimeters are used.
Such variations are dictated by the variety of wavelength and thickness of the corrugated board. When choosing a self-tapping screw, it is necessary to provide that its length is no more than half the thickness of the sheet.
Important! Self-tapping screws made of galvanized steel are considered to be of the highest quality. They cost a little more than the others.
Preparing for installation
A roof made of corrugated board can have a small slope, this is one of the positive aspects of this coating. Since the material is thin and light, it can be mounted on a sparse crate in steps of five to ten centimeters.
For styling roofing material you will need:
- drill with attachment or screwdriver;
- electric shears or hacksaw;
- self-tapping screws for the roof.
For your information: the laying of corrugated board on a roof with two slopes begins from the end on the right, on a hipped structure - from both sides at the top of the slope.
The selection of sheets for installation should take into account their location, length and width of the roof surface. This way you can minimize losses when trimming the material.
Important! All cut edges of the corrugated board must be treated with an anti-corrosion compound.
Basic requirements for installation conditions:
- taking into account the climatic features of the region (reinforced fastening of the material in places with strong winds);
- work in wet weather is not allowed;
- it is important to observe safety precautions when working on high-rise buildings (use safety material, fences and soft comfortable shoes)
The main mistakes when installing the profile:
Calculation of the consumption of fastening material
Before starting work on the roof, you need to calculate the consumption of roofing material and screws. There is a simple rule dictated by practice: square meter the profiled sheet is fastened with at least nine self-tapping screws. This consumption is considered standard.
Taking into account the fact that the corrugated board is laid with an overlap, the number of fasteners is reduced. In addition, when purchasing self-tapping screws, you need to take into account the accidental losses that always occur during construction works... The easiest way is to multiply the square of the roof by nine and get the required amount of fasteners. Self-tapping screws are usually sold in packages labeled with the number of parts.
For your information: in three and a half kilograms of the smallest roofing screws 2.5 centimeters long, there are 1000 pieces.
Self-tapping screws are packed in standard packages from 100 to 6000 pieces. Large fasteners are packed in boxes of a thousand pieces.
Fastener placement principles
You should be aware that an excess of attachment points can lead to deformation of the sheet, and their lack - to tearing off the material in a strong wind.
To rationally use fasteners, you need to know several basic principles of work:
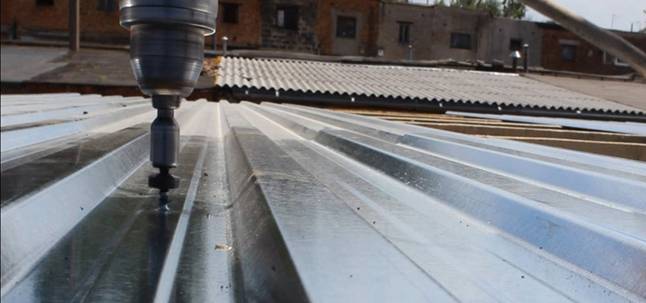
- consumption of fasteners per square meter of sheet 6-9 pieces;
- self-tapping screws can be screwed into the upper wave only when the sheets are joined.
For your information: for the lathing of light corrugated board, a rail of 40 by 40 or 60 by 40 millimeters is used.
A roof made of corrugated board must withstand a significant wind load, therefore it is important to firmly fix the material on the roof.
The procedure for laying the profiled sheet
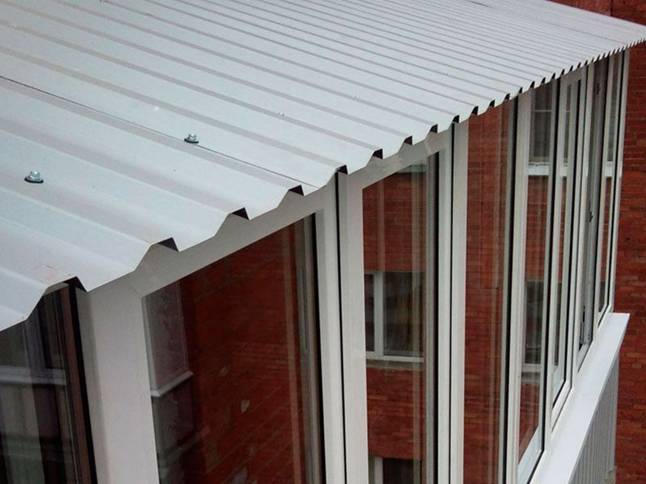
Important! After laying the profiled sheet, you need to periodically check the fasteners for loosening and untwisting. To prevent deformation of the roof sheeting, the self-tapping screws must sometimes be tightened. In the event of rust spots, the fasteners are replaced with zinc, having previously treated the surface with an anti-corrosion compound.
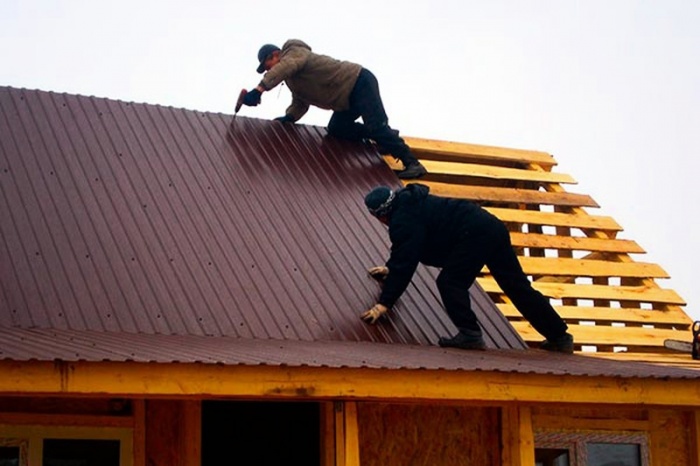
After all the work on the roof is finished, you need to remove all unnecessary from its surface.
It is important to remember that not only the strength of the structure, but also its durability depends on high-quality roofing screws. You should not save on fasteners, and then it will securely and permanently fix the corrugated board, preventing the appearance of rust and deformation
Self-tapping screw - one of the types of fasteners, presented in the form of a metal rod with a triangular external thread and a head.
When carrying out fastening in the connecting holes of objects, this fastening representative independently forms an internal thread.
The main distinguishing feature of self-tapping fasteners from their closest similar types of fasteners, screws and screws, is that the thread is cut completely over the entire surface rod.
The self-tapping screw kit includes a special gasket... It does not allow moisture to pass under the screw head, blocks the formation of corrosion and eliminates the need, when working with self-tapping screws, to select gaskets for them from ordinary washers.
Quite often, manufacturers cover self-tapping screws, designed for work on fastening profile sheets, various colors of polymer paint.
This makes it possible to choose "your" self-tapping screw for each color shade of the sheet. Such a decision gives a kind of aesthetics and performs protective functions for fasteners, prolonging its operation.
By application, self-tapping screws are divided into main types:
1.for working with a profiled sheet on a wooden frame
2.for fixing the profiled sheet to the metal frame
3. for fastening ridge and all kinds of additional roofing elements.
Self-tapping fasteners for profiled sheets in their design have a special tip, reminiscent of a drill and a hexagonal head... This allows the self-tapping screw to be fixed in a screwdriver or drill chuck, greatly facilitating the workflow.
For fastening the profiled sheet, use self-tapping screws of various sizes. But before starting work, the estimated load is determined, which makes it possible to select the parameters of the fasteners.
- 4.8-6.3 mm - screw diameter;
- 19-25 mm - the length of the screw.
For fastening galvanized steel sheets with a powerful polymer coating thicker screws are allowed. This is due to the fact that the weight of the bonded sheet is significantly increased.
The length of the screw is calculated based on the thickness parts to be connected. In this case, you need to add up the thickness values \u200b\u200bof the parts and add 3-5 mm. The drill length is not taken into account. This way you can achieve a reliable connection.
How can we determine the approximate consumption of screws? Suppose must be done roofing ... The usual consumption is 5-8 self-tapping screws per 1 sq. M.
But if you want to make high-quality fasteners – remember:
- on a straight roof section for one sheet 6-8 screws required;
- fastening perform with a step of 300-500 mm;
- at the ends of the sheets, the number of screws increase for reliability operation during strong winds.
For the device of the fence, the profile sheet is attached to the logs with 5-6 screws. If you want to get an improved stability option - add a little more to the consumption of screws... We advise you to mount it through all the waves of the profiled sheet - you will not regret it.
Installing on a wall surface - apply self-tapping screws through one wave bend, bottom edge. Rivet the vertical joints.
The weight value of self-tapping screws is calculated based on their diameter and thread. A set of a thousand pieces for fastening profiled sheets will be 18.5 kg (for self-tapping screws 5.5x105 mm) and 41.7 kg (for self-tapping screws 6.3x280 mm). These sizes of hardware are taken as the most used in working with this material.
And also watch a video on how to choose the right screws:
Decking is a widespread type of roofing, which is popular for the most part because of its technical characteristics, aesthetic appearance, affordable cost, etc.
For high-quality fastening of the corrugated board, you will need special fastening materials - self-tapping screws, which are worth talking about.
About the technical characteristics of the fastening material
As a material from which self-tapping screws for installation are made metal roofs, as well as for wall fastening of corrugated board, carbon steel of the C1022 brand is used.
In accordance with GOST, the surface of the fastening material under consideration can have a zinc coating in the range of 12.5-15 microns.
Zinc coating is used in self-tapping screws to provide anti-corrosion properties.
Paying attention to the fact that fixing the corrugated board by means of self-tapping screws implies the effect of loads, all batches of this fastening material are thoroughly tested for rupture, while 102 kg / cm is considered to be a normal indicator (most manufacturers of self-tapping screws prefer to attach a higher value, reaching 170 kg / cm. ).
The design of a self-tapping screw is often the same: a self-tapping screw is a screw-drill with a semicircular, hexagonal, or countersunk head.
Self-tapping screws for a fence made of corrugated board differ from roofing ones in a smaller thread pitch.
In turn, the head of the screw is painted in a color identical to the color of the corrugated sheet being installed.
Also, the screw head can have a polymer coating.
In fact, the drill is the lower part of the self-tapping screw.
This avoids additional drilling during assembly work.
The self-tapping screw can be screwed in manually, or you can use an electric tool for this purpose - a drill with the required nozzle and a soft start, or a screwdriver (in the case of a power tool, the installation of metal sheets is significantly accelerated).
In addition, the self-tapping screw for mounting the corrugated board is equipped with a washer made of neoprene rubber.
In this case, rubber plays the role of a hermetic material that protects the joints from moisture.
The washer is pressed against the working surfaces of the corrugated sheets with a standard press washer or EPDM supplied in the set.
It should be noted that the EPDM washer has a number of positive qualities, the main of which is elasticity.
When choosing self-tapping screws, you should pay attention to the following:
- zinc coating;
- tip type;
- polymer coating;
- the presence of a washer;
- the required length of the goods;
- the presence of a neoprene layer under the washer.
How to make the correct calculation of fasteners
The correct calculation in this case is necessary in order to protect yourself from the short service life of the corrugated board.
Also, the correct calculation will serve to the advantage if there is a desire to save money on fasteners.
Calculation features
For example, let's take a professional sheet, the width of which is 1000 millimeters, and the length is 12 200 millimeters.
Note that the exact size of the roofing sheet is very important!
The profiled sheet is fixed to the extreme supports with each wave, and also through one wave - to the intermediate ones.
The sheets are attached to each other using self-tapping screws with a distance of 1 meter from the support in increments of 250, 500, 1000 millimeters.
The calculation of the lower self-tapping screws is performed, as a result of which the result is 6-9 units per 1 m 2.
Dimensional accuracy during calculation is essential.
Corrugated board fastening technique
The durability of the roofing is closely related to the correct execution of the sheathing.
Thus, it will be necessary to perform the correct calculation of the pitch of the crate.
The step of the battens should include the angle of inclination of the roof, the type of corrugated board used.
It is imperative to use a vapor barrier film.
Fixation of sheets of material should begin with quality preparation.
Roofing screws for corrugated board, as a rule, have a section thickness of 4.8-6.3 millimeters.
The length range ranges from 19-250 millimeters.
The speed of work, as well as its quality side, depend on whether the head of the self-tapping screw has a hexagonal shape.
If the screw is hex, then the speed and quality of work on fastening corrugated sheets is significantly accelerated due to the possibility of using an electric tool in the form of a drill or screwdriver.
A lot also depends on the correct selection of the length of the self-tapping screw.
The threaded part of the self-tapping screw must exceed the width of the surfaces that are connected by 3 millimeters.
Sometimes combined rivets can be used to connect the roofing sheets.
The neoprene washer supplied with a self-tapping screw plays a protective role, since it makes it impossible for moisture to enter the under-roof space.
At the stage of calculating self-tapping screws, the moment is taken into account, according to which 6-8 screws will be needed per sheet of corrugated board (in the case of installing an ordinary roofing corrugated board).
Closer to the end of the sheet, the number of self-tapping screws increases for better wind protection.
The fastening step should not be less than 500 millimeters.
The procedure for fastening profiled sheets is worthy of consideration.
Materials and tools:
- bulgarian;
- screwdriver;
- roulette;
- lacing;
- level;
- nails and hammer;
- stapler and staples.
Sequence of work:
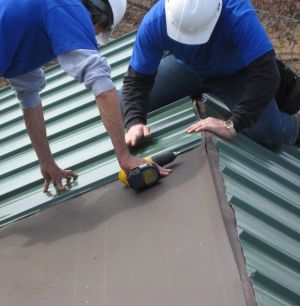
How much are self-tapping screws
The minimum cost of self-tapping screws with a galvanized head is within 1.8 rubles per unit of goods, while the maximum price for the product in question reaches 3 rubles.
A self-tapping screw with a polyester-coated head will cost 3-3.5 rubles.
Self-tapping screws with polymer coloring and a protective coating of imported production have a retail value of about 8.5 rubles per piece.
When performing calculations, installing profile sheets, you should carefully and attentively treat everything related to the construction of a roof.
Otherwise, there is a risk of getting a short-lived result of work, and, consequently, unnecessary financial costs.
Watch the video about the choice of self-tapping screws.
Description and specifications
When building various communications using profiled sheets, it is important to choose the correct installation method.
Self-tapping screws for corrugated board are the main fastening element, and also play an important role in the construction of various communications.
The most reliable and high-quality fastening is provided by special self-tapping screws for corrugated board.
Fasteners are load-bearing, therefore, the main part of the tested loads falls on them.
The self-tapping screw got its name for the ability to independently cut a thread in any material, where it is screwed in without first drilling holes. This is achieved due to the high strength acquired by thermal hardening during the manufacturing process. In the manufacture of self-tapping screws, alloy steel with galvanized zinc coating of white or yellow color is used. The color of the coating does not matter, except for decorative. The thickness of the coating, according to GOST, should be in the range from 12.5 to 15 microns, on high-quality self-tapping screws, the galvanized layer is 20-25 microns. Black self-tapping screws are obtained by oxidation or phosphating of metal, while a protective coating of phosphate or iron oxide with a thickness of 2-15 microns is formed on their surface. Such a film is less resistant to weathering.
Self-tapping screws are structurally different in the shape of the head, splines, pitch and type of thread, shape of the tip. Both wood and metal tips can be sharp or drill-shaped. The head of the self-tapping screw can be countersunk, biscuit, hemispherical, flat, hexagonal. Hemispherical and hex sockets are often made with a press washer, and the latter with an EPDM (ethylene propylene rubber) washer, where the conical washer with a rubber gasket is part of the head itself. Single washers, steel bent or aluminum tapered, with neoprene or EPDM gasket, are used in conjunction with a self-tapping screw with a press washer. The heads of roofing screws along with washers are often coated with liquid or powder paint of different colors.
Self-tapping screws for wood have a larger thread pitch than for metal, but the tip in the form of a drill is usually smaller than the diameter of the threaded rod. Self-tapping screws for metal have a drill equal to the diameter of the rod, and high quality steel and special sharpening do not disturb the metal structure when screwing in, reducing the risk of corrosion.
How to choose the right type and size of screws
Self-tapping screws, depending on the type of metal and size, are used differently, so it is necessary to clearly distinguish between them, as this will simplify the work associated with the installation or fastening of metal structures.
The price of a self-tapping screw with a galvanized head is from 1.8 to 3 rubles per piece, with a polyester coating - from 3.2 rubles. and higher. Imported premium hardware with a colored polymer coating cost from 8.5 rubles.
The number of screws for attaching the profiled sheet depends, first of all, on what exactly it is used for. It can be laid on the roof, used as a material for facade decoration, mounted on a fence, or even mounted on a frame in the manufacture of a garage, shed and other buildings. In each of the above cases, the consumption of self-tapping screws for corrugated board will be different.
In addition, special operating conditions - for example, strong winds or large snow cover - also affect the consumption of self-tapping screws towards an increase in their number. So, if you are installing a profiled sheet fence near the sea, where stormy winds often occur, then you may need to attach the sheets to the bottom of each wave to achieve greater reliability.
How many self-tapping screws are there on a sheet of corrugated board when attaching it to the roof?
Installation of corrugated board begins from the side of the eaves. First, the first left sheet of the bottom row is laid, then the second with an overlap in one wave. After aligning the sheets along the edge of the eaves, the profile is attached to the bottom beam of the sheathing in each wave. In the place of the overlap, the sheets are connected together with rivets.
After installing the first two bottom sheets with an overlap of 200 mm, the left sheet of the second row is installed. In the place of the overlap, the lower and upper sheets of the corrugated board are attached to the crate in each wave. In the interval, each sheet of corrugated board is fastened in a checkerboard pattern after 1-2 waves. For reliable fastening, the distance between the roofing screws should not be more than 500 mm.
Based on the above-described technology for fastening the profiled sheet, they determine how many self-tapping screws on the profiled flooring are needed for reliable laying of the roofing.
To do this, you need to perform a simple calculation of self-tapping screws for corrugated board. If we lay a sheet with a length of 8.0 m and a width of 1.1 m with a step of fastening to the lathing of 500 mm, then we need 10 self-tapping screws for fastening the profile in the upper and lower parts, as well as 8 more pieces for fastening the middle part of the corrugated board. The total consumption of self-tapping screws for the profiled sheet will be 18 pcs. This number must be multiplied by the number of sheets on the roof and we will get the number of self-tapping screws needed to directly fix the corrugated board.
The number of screws per profiled sheet may differ depending on the length and width of the sheet. In addition, with large slopes, it is recommended to reduce the fastening step, which also increases the consumption of self-tapping screws per 1m2 of profiled sheet. When fixing corrugated board, the greatest attention should be paid to the joints of the roofing, it is there that the probability of leakage is highest.
At the ends pitched roof, in places of pediment overhangs, a profiled sheet of roofing must be fixed to each batten of the sheathing. This also increases the number of self-tapping screws per 1m2 of profiled sheet.
Thus, such a concept as the rate of consumption of self-tapping screws on a profiled sheet can hardly be considered completely correct when it comes to installing a roof. Rather, we can talk about some average figure that allows you to make an approximate calculation of self-tapping screws for a profiled sheet when ordering materials for installing roofing. In this case, it is necessary to order 5-10% more than calculated, since there is always a possibility of marriage, unforeseen expenses, loss and breakage of self-tapping screws.
Calculation of self-tapping screws for fastening corrugated board to a fence
The number of screws for attaching the profiled sheet to the fence depends, first of all, on the number of lags. As a rule, one sheet is fixed with 3 self-tapping screws per log. That is, if with two lags you need 6 pieces, with three - 9.
As in all other cases, the sheets must be fixed with self-tapping screws in the overlap areas, and with one more - approximately in the middle. If the fence is made in the area of \u200b\u200bhigh wind loads, then the number of self-tapping screws for fastening the profiled sheet increases sharply - up to screwing them into each wave.
However, in most cases, to calculate the approximate number of self-tapping screws, it is enough to use a simple formula: 3 · L · n, where L is the number of lags, and n is the number of corrugated sheets.
Consumption of self-tapping screws for profiled sheet on facades and buildings
When installing corrugated board on the facade of a building, it is usually attached to a special frame through a wave, while, as in all previous cases, fastenings in the overlap areas are required. The distance between the screws along the length of the sheet is, depending on the operating conditions of the building, from 0.5 to 1 meter.
Thus, a sheet, 2 meters long, must be fastened with three rows of self-tapping screws, which are staggered across the wave. In some cases, when it comes to a region with a high wind load, it is possible to mount in each wave.
The consumption of self-tapping screws when finishing the facade with a profiled sheet and cladding technology:
1. Insulation;
2. Guides;
3. Decking;
4. Self-tapping screw.
In the case of the manufacture of various buildings from corrugated board, the sheets are already attached to each wave, while the distance between the rows of screws is about a meter.
How many screws are there per sheet of corrugated board - calculation by weight and per 1 m2 of coverage
It is considered that the approximate need for roofing screws per 1 m2 of roofing is 8-9 pcs. Based on this, it is easy to calculate how many self-tapping screws per profiled sheet will need to be ordered for the installation of the entire roof covering.
To do this, subtract the size of the transverse overlap, equal to 150-200 mm, from the length of the corrugated sheet. The resulting figure is multiplied by the useful (working) width of the sheet. As a result, we get the useful area of \u200b\u200bthe corrugated sheet. After that, multiply the result by 9 and get the approximate number of required roofing screws per 1 m2.
The total number of self-tapping screws is determined based on how many self-tapping screws per 1m2 of profiled sheet we need and the total roof area. The given approximate calculation also takes into account the self-tapping screws required for fastening various abutment elements, wind and cornice strips, aprons around ventilation and chimneys and snow holders.
When purchasing self-tapping screws, it is not at all necessary to count out all the quantity you need one by one. For each size of the screw, its weight is precisely known. So, for example, one thousand pieces of roofing screws Ø4.8 mm and 25 mm long weigh 3.5 kg, and a thousand screws Ø6.3 mm and 152 mm long - 45 kg. Therefore, manufacturing plants pack small roofing screws in packages of 100, 200, 250, 500, 1000, 2000 and 6000 pieces, and the maximum number of large screws in a package is 1000 pieces.