Circumstances forced me with my own hands. In the hot summer of 2010, many summer residents faced the problem of water supply.
The wells supplying uninterrupted water have dried up.
Most owners of summer cottages and suburban areas use iron concrete rings with an inner diameter of 1000 mm and a height of 900 mm.
It seems that deepening the well is not a problem, but ...
It will not be possible to besiege the rings of the well squeezed by the soil, it is unrealistic to dig in the well from all sides ...
The first thing that comes to mind is that it's easier to dig out a new one, but the price of rings of 2000 rubles instantly jumped to 2300-2400 rubles, not available, the queue is scheduled for 2-3 months in advance. And I want to drink and water the garden. If you move your convolutions a little and get off the sofa next to the TV, then this problem can be solved in a few days, for some you can save a significant part of the family budget, and for some you can stir up a profitable business. It goes without saying that the outer diameter of the rings for deepening the existing well should be less than 1000 mm. I took an outer diameter of 840 mm, an inner diameter of 700 mm and a height of the rings 600 mm. Concrete for such a ring will require 100 liters, i.e., about 180 kg, for the preparation of which 50 kg of cement (180-190 rubles), sand 130 kg (45-50 rubles), a bucket of water and approximately 10 kg of wire are needed (let it be 100 rubles, but I will find a wire rod of 4-6 mm or steal it somewhere). The cost is not more than 340 rubles. for 0.6 linear meters of the future well. And how much would a standard ring costing 2400 rubles cost if its height was not 900 mm, but 600 mm? 2400 RUB : 900 mm x 600 mm \u003d 1600 rubles. We save 1260 rubles. on each ring. I climb off the sofa and go to the garage (aka a workshop and a warehouse of illiquid assets).
To make it immediately clear, I show the finished dIY well ring mold.
This is what I had to do. Actually make formwork for rings with your own hands not difficult. How to make a shape for rings I came up quickly.
If you know how to use metal scissors, a grinder and a little electric welding - the flag is in your hands and let the shabashniks break off.
I cut two rings with an inner diameter of 840 mm and an outer diameter of 900-950 mm with scissors for metal from sheet steel 1.8 mm thick. Outside diameter unprincipled - these will be stiffening ribs for the outer part of the formwork. The scissors cut normally if the handles are lengthened. I roll a sheet of metal 600 mm wide into a "tube", top and bottom - rings, boil it, cut the resulting contraption into two halves with a grinder, reinforce the cut points with angle steel with holes for bolts for assembly and disassembly.
It is more difficult with the vnutryanka ... you need to come up with something so that it is not clamped with concrete after pouring, and you can freely remove it. Therefore, before pouring, its diameter must be equal to the design one, i.e. 700 mm, and after pouring - decrease by 15-25 mm.
I solved this problem by destroying two old car jackby making a device for compressing the expansion into four sides.
Easier to show than to explain:
I assemble the inner "barrel" from two round parts with a diameter of 700 mm (such as the bottom and the lid), and the side of the barrel, again from sheet steel 600 mm wide. I again roll the sheet into a tube so that it does not roll out - I pull it with a cable with a winch, boil the bottom and the lid. In the lid and bottom of the finished keg, I cut out square holes (I can't cut the round ones with a grinder), install the perversion that came out of the jacks inside, cut it into 4 parts, strengthening the cut with a corner.
Checking if the compression-decompression mechanism is working:
Works fine.
I’ll digress a bit: if you make sleeves from thin metal, for example, from galvanized steel with a thickness of 0.55- 0.8 mm, a width of 600 mm and a diameter of 700 and 840 mm, then with their help it will be possible not to wait for the concrete poured into a homemade one to seize, and immediately after vibrating the concrete mix, remove the formwork. Thus, it will be possible to cast not one ring per day, but as many pairs of sleeves you prepare. Even the thin metal of the sleeves will not allow the concrete mixture to spread out after removing the formwork.
Note the bolts in this photo. They, among other things, play the role of release limiters.
Now you know how to make ring formwork. Next, we knit the reinforcement cage. It can be of any design, the main thing is that the distance between the rods is no more than 200 mm in height and 300 in circumference. Diameter - 770 mm. Do not forget to release the hinges.
I got this:
We attract free labor in the person of relatives to mix concrete in an old bathtub. I couldn't catch my relatives, but there is a concrete mixer.
Pour the ready-made mixture into the homemade ring formwork, vibrate with a piece of reinforcement and go to drink beer on the sofa under the TV until the next day. During the night, the concrete will set, and you can remove the homemade mold.
The outer part can be easily removed. The inner part should be removed carefully so as not to damage the walls of the ring. It is better to do this together or to build a lifting mechanism like a crane.
It is better to let the rings stand for two weeks under natural conditions of strength development, then they can be loaded, transported, turned over, if they did not save on cement, of course ...
When constructing engineering communications during the installation of water supply systems, sewerage systems, drainage of a personal plot, it is necessary to build wells for various purposes. At the same time, ready-made reinforced concrete rings for wells are purchased at large factories or from individual entrepreneurs engaged in the manufacture of similar products. In some cases, it is more profitable to buy a form for self-production of data concrete structures and cast rings in the required quantity on site. There are various options for blanks that differ in size and configuration, using which, you can get reinforced concrete products of different diameters and heights.
This video shows the work of a self-made installation, with the help of which concrete rings for wells are produced. It should be noted that it takes only 15 minutes for two workers to produce one piece.
Preparation of concrete with maximum strength
For the manufacture of reinforced concrete rings for a well, matured cement of the M400 brand and higher is required. Matured cement is considered, from the date of production of which more than a month has passed. In addition to cement, you also need water and sand, as well as gravel. It is important to observe the ratio of all ingredients to obtain maximum concrete density. To do this, for each part of the cement is taken:
- sand (2-2.5 parts);
- water (0.5-0.7 parts);
- gravel (3-4 parts).
The preparation of concrete begins with mixing sand and cement. Then water is added to the mixture of materials and the mixing process continues. Next, the turn comes to gravel, which must be moistened with water before adding. In a mold set on a flat floor or steel pallet, first place reinforcement mesh, on which the lugs necessary to move the finished ring are fixed. After that, they start pouring the form with concrete. The thickness of the reinforced product ranges from 0.6 to 11 mm. Depending on the dimensions, the volume of the produced ring changes, which affects the amount of the mixed solution.
Important! If you make rings for a well with your own hands without using reinforcement, then increase the wall thickness to 15 cm.The service life of such rings is very long. To prevent the displacement of the cylindrical walls, a spacer made of wooden wedges is installed between them.
It is recommended to make concrete rings on an open construction site under a shed to prevent precipitation from entering the hardening mortar.
List of required equipment
Work on the manufacture of concrete rings is carried out on a spacious construction site. The list of mandatory equipment and necessary fixtures can include:
- concrete mixer (shovels and a metal sheet on which concrete mortar is manually mixed);
- blanks for rings (special shapes);
- vibrator;
- lifting devices, since the weight of one reinforced concrete ring for a well can reach 500 kg and more;
- reinforced frame (you can purchase ready-made or weave it yourself from wire).
How to make a shape for a well ring yourself?
When self-manufacturing a cylindrical shape, two metal barrels are selected, the diameters of which will make it possible to make a ring of the specified dimensions. Instead of barrels, air ducts or pipes of the corresponding diameter can be put into operation. If there are no ready-made cylindrical shapes of the required diameter, then they are made from separate steel sheets, connected to each other by simple window or door awnings. These connecting elements are attached to the metal mold by welding or rivets.
Important! You can perform formwork not only from metal or plastic cylindrical "glasses". It is easier to work with light plastic molds with small mechanization of manual labor.
Name | Price with VAT) |
Ring shape KS-7-9 | 21,000 RUB |
Ring shape KS-10-9 | 23,000 RUB |
Ring shape KS-15-9 | 35,000 RUB |
Ring shape KS-20-9 | 47,000 RUB |
Ring cap shape 1m | 8,000 RUB |
Ring cap shape 1.5m | 11,000 RUB |
Ring cap shape 2 m | 14,000 RUB |
Benefits of collapsible well ring molds
1. Forms are easily disassembled and moved around the site by 1-2 people, they do not take up much space during storage.
2. Parts of the mold are connected using wedge locks, which reduces the time of assembly and disassembly several times, just one bolted joint.
3. The formwork has hollow formers for the production of rings with technological holes 50 mm in diameter.
4. The mold for the production of reinforced concrete rings is made of metal with a thickness of 2 mm, which ensures its strength without additional reinforcements.
![]() |
The parts of the formwork are connected by locks, which greatly reduce the time of assembly and disassembly |
![]() |
Void formers for the production of rings with technological holes 50 mm in diameter |
![]() |
Form with a diameter of 1 m in transport / storage |
![]() |
Mold with a diameter of 1.5 m in transport / storage |
![]() |
The centering of the formwork for the rings is carried out using spacer inserts, which are removed after filling the formwork with concrete |
![]() |
Internals form |
![]() |
Ring cap shape with a diameter of 1 m |
![]() |
Ring cap shape with a diameter of 1.5 m |
![]() |
Finished ring after stripping |
![]() |
Filling caps facilitate mold filling |
Starting a business for the production of precast concrete rings, and choosing our well ring molds, you can recoup your investment after 1-1.5 months of work, because the average profit from one ring is 1000 rubles. A day on one formwork, you can make 5-10 concrete rings if you are using hard concrete or 2-3 rings if you are using movable concrete from a concrete mixer or mixer.
Produced by us collapsible forms for reinforced concrete rings, in the course of long-term operation, we and our customers have confirmed their operational reliability and have proven themselves excellently with better side throughout the entire service life. Durability and excellent consumer properties are due to the special design of the form with ring reinforcements and the optimal metal thickness of 2 mm, while molds for the production of concrete rings are not inferior in strength and durability to formworks made of thicker metal, and have ideal geometry. The strength and lightness of collapsible forms increase their mobility, make it possible to use them in an open area not equipped with lifting mechanisms, which is especially necessary in rural areas and other areas not provided with a three-phase power grid. Over the entire time, more than a hundred molds for well rings various sizes and caps for them. All our clients are convinced of the short production times and high quality of the formwork, many of them have become our permanent partners and, when expanding their production, again turn to us for molds for the production of reinforced concrete rings.
The formworks are designed for the production of reinforced concrete rings by vibratory casting and have an undeniable competitive advantage over their analogues. Components molds for concrete rings, manufactured by us, are connected to each other using special wedge locks and disassembled in a matter of seconds with just one hammer. Unlike bolted molds, which take up to half an hour to disassemble during assembly, and the bolts must be replaced every week. the edges of the bolts are erased, the threads are clogged with concrete, and the bolts become completely unusable.
Our well ring molds are made of 2 mm metal and have a frame made of shaped pipes sizes 40x40 or 30x30 and corners 40x40. The molds consist of two cylinders, which represent the outer and inner shaping surfaces of the reinforced concrete ring. Both the outer and inner parts of the mold for reinforced concrete rings are collapsible. The external formwork consists of two (three) parts, and the internal formwork of three. Thus, the form for the ring is mobile, moves around the workshop or site without lifting mechanisms by two or three people.
A concrete ring is formed directly on the floor of the workshop (site) if it is sufficiently flat, or you can use metal or wooden pallet... The ends of cable coils are very good for this, they can be purchased at firms selling cable products for mere pennies - 100 - 200 rubles. To prevent adhesion of the finished product, a plastic film is placed under the mold, and the walls of the collapsible mold for concrete rings are lubricated with a special emulsol lubricant, and in its absence, working off.
After preparation, the solution begins to fit into the formwork in layers, each layer is 20-25 cm high. After that, the concrete is compacted with a bayonet, a metal or wooden rod. This is necessary so that the mortar fills the formwork more densely, displaces the surrounding air and fills in possible voids. When the concrete level in the mold exceeds the average level, the spacers can be removed because parts forms for reinforced concrete rings will no longer move relative to each other. After complete filling of the form with concrete, the upper edge is smoothed with a trowel, this surface should be as even as possible. A deep vibrator can also be used to compact the concrete in the formwork, which will significantly save time.
Form for the production of well rings can be disassembled after the solution has set. Rings can be produced at any positive ambient temperature. Freshly formed rings must be covered with tarpaulin or foil from exposure to precipitation and direct sunlight. Also, to improve the conditions of concrete hardening, fresh well rings are recommended to be watered with water 1-2 times a day.
Is it possible to make durable reinforced concrete rings yourself or is it easier to buy ready-made ones from the manufacturer? A master class on making durable concrete for rings will answer this question.
Any task requires the right approach to its solution. If there is a need to build a well, a septic tank, a cesspool in the house on the site, you cannot do without reinforced concrete rings. Before starting work, you need to carefully study this topic.
First, let's analyze the cost. On average, a finished ring costs from 1,500 rubles. up to 4500 rubles, depending on the grade of concrete, weight and dimensions.
To make one ring with a diameter of 1.5 m, you need 0.3 cubic meters of concrete. The price for a cube of cement is from 2500 rubles. up to 4500 rubles, depending on the brand. The cost of the ring is 750 rubles on average. The savings are evident.
Secondly, let's analyze the labor costs. When buying ready-made concrete products, all efforts will be directed to finding a bona fide manufacturer from whom you can purchase a quality product. You also need to arrange delivery finished products to the site.
If a decision is made to make reinforced concrete rings with his own hands, then there is a need to search and purchase high-quality material, tools and the manufacture of special forms for pouring concrete products. According to the efforts made, the option of buying ready-made rings comes out on top.
Materials and equipment
To make a ring with your own hands, you will need the following:
- Sand, crushed stone, cement of high quality M200-M500 (for the manufacture of concrete mixture).
- Concrete mixer.
- The wheelbarrow is garden.
- Large containers.
- Form for pouring concrete mixture.
Making a mold for pouring concrete products
Technological conditions for the manufacture of the mold include the following points:
- The formwork should be of a flat ring-like shape, including two collapsible rings installed in each other.
- The material for the manufacture of formwork is metal or wood.
Most the best way for making molds - use old metal barrels as a material. Ready-made cylinders of the required size can be cut out of them.
The inner cylinder should be ten centimeters higher than the outer one.
Manufacturing technology of molds for casting rings 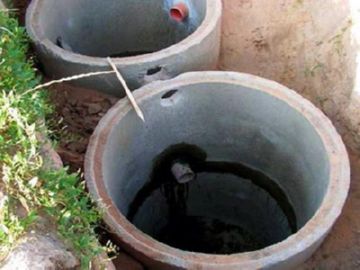
- Draw two longitudinal lines on the outside of the large cylinder. This divides the cylinder into two equal parts vertically.
- Place two door sheds along the lines, aligning them exactly with the marked line.
- Draw similar lines to the inside of the cylinder.
- Cut the cylinder along the inner lines with a grinder, being careful not to move the canopies.
- Disassemble the hinged joints of the awnings on one side. To do this, cut off the retaining caps at the spindle.
- Reattach the cylinder blades with the clips.
- Finish the inner cylinder: mark two vertical lines at a distance of 1/3 of a circle.
- Install canopies along the marked lines.
- Cut the cylinder on the outside with a grinder.
- Disassemble the structure along one of the lines, reassemble.
- Check connections: the inner cylinder should open easily inward and the outer cylinder outward.
Stages of precast concrete production
To make a reinforced concrete ring, you need the following:
- Prepare a strong concrete mixture, taking into account the proportions: 1 part of cement, 1.2 parts of sand, 2.7 parts of crushed stone. From 10 liters of cement, 31 liters of ready-made high-strength concrete mixture is obtained. The amount of water is 50% of the weight of the cement.
- Place the concrete pouring mold on a flat, clean surface.
- Pour the concrete mixture into the mold in small portions, constantly ramming with a metal rod.
- Smooth the end face of the future concrete products.
- Leave the product to harden for four days.
It is important to carefully remove the formwork. Open the inner cylinder first, then the outer one.
Useful tips for making a reinforced concrete ring 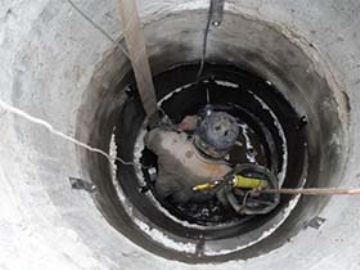
- The filling must be carried out in layers of 20 cm.
- The ambient temperature should be no higher than 22 ° C and not lower than 8 ° C.
- The higher the ambient temperature when pouring the concrete, the stronger the concrete will be.
- To increase the plasticity and water resistance of a reinforced concrete product, potash glass can be added to the concrete mixture.
- To increase the fluidity of the concrete mixture, a liquid detergent is added to the composition - 2% of the volume of the mixture.
- For the strength of concrete products, PVA glue is added to the concrete mixture.
Installation of concrete rings in a well
First of all, you need to decide on the place of the future well and dig a hole. The depth of the pit should be 1 meter. This is an important parameter for normalizing.
Ring setting technology
- Set the first ring to a depth of 1 meter.
- Continue sampling of soil from under the ring until the concrete elements settle naturally by one meter.
- Install the second ring on top and continue sampling of soil from under the lower reinforced concrete until the rings shrink by another meter.
- Continue placing the rings on top of each other in the same way until an aquifer appears.
- Lay the joints between the rings with waterproofing and cement.
- Dig a hole in the soil aquifer. For more comfortable operation, you can use a mud pump.
- Fill the bottom of the well with rubble with a layer of 15 cm.
- Fasten reinforced concrete rings with metal staples. Paint the staples.
- The rise of the rings above the soil level should be at least one meter.
- Outside the rings, you can install waterproofing: remove the top layer of soil around the perimeter of the well, fill the depression with sand and cover waterproofing material... Cover with gravel on top.
Thus, strong reinforced concrete rings can be made by hand.
The process, although laborious, is quite economical. Having mastered it, you can easily do it.
Concrete rings are a highly demanded product used for the construction of hydraulic engineering and sewerage facilities. Moreover, the demand exists not only from large construction companies, but also from private traders, individual developers who want to provide themselves with a comfortable life.
For the manufacture of these products, special molds are used for the production of well rings, produced by the industry in accordance with the standards that regulate their sizes (GOST 8020-90).
Factory forms
For the construction of various types of wells, wall rings of KS of various standard sizes are used. They are made by pouring concrete into special molds, which are double cylindrical metal formwork.
Their outer and inner diameters correspond to the values \u200b\u200bregulated by the State Standard, as well as the difference between them, equal to the thickness of the finished ring.
The formwork metal has a thickness of 3 to 8 mm. Vibrators are installed on it in an amount from one to four, depending on the size of the ring, intended for compacting the concrete mixture.
For reference. The process of producing rings using these shapes is extremely simple.
They are installed on a metal pallet, reinforcement with a diameter of 6-10 mm is laid inside, concrete is poured and vibration is turned on. As the solution settles due to tamping, it is added. After the product has acquired a certain strength, the shape is removed.
When standard sizes the forms may still differ slightly from each other, which must be taken into account when purchasing them.
The main difference is the possibility of making rings with different end shapes:
- Rings with flat ends are installed on top of each other, followed by sealing of the joints and tightening with metal brackets;
- Rings with locks have a ridge on the top and a groove on the bottom. They provide a tighter and more reliable connection, preventing the rings from displacement relative to each other in the horizontal plane.
The sale price of such products is always higher.
To form such a lock, the formwork is supplied with hollow formers - metal strips welded in a circle. They are located on the outside of the inner ring of the formwork and on the inside of the outer ring.
In addition, the shape for well rings can be designed for making rings with metal transport loops, which are rigidly connected to the reinforcement frame. And it can provide the formation in the walls of the ring through holes-lugs for attaching the lines.
When planning to take shape, pay attention to these points, as well as to the thickness of the metal from which they are made. The larger it is, the stronger and more durable the product, and the more accurate the geometric.
Homemade forms
Having your own mold for casting rings is beneficial in all respects. Of course, it can be purchased, but the high cost of such products (from 40 to 80 thousand rubles) will not justify the independent production of rings for personal needs.
Another thing is if you are going to establish their production for sale or acquire a form together with neighbors in a garden cooperative. Then this venture makes sense.
But if you only need to make 3-4 rings to build a water well, or cesspool, it is better to make the formwork for them with your own hands.
What will it give you:
- Saving money on the purchase of finished products;
- No costs for the delivery of rings to the site - they can be done directly at the construction site of the well;
- Confidence in the quality of the raw materials used;
- The opportunity to make money by renting out the formwork to neighbors or by making well rings for them yourself.
How to make formwork
The best shape for the production of well rings is obtained from metal barrels or large diameter pipe pieces, plastic cylinders. These products have the correct geometric shape, which is difficult to obtain from sheet metal without special equipment - bending machine.
Note! The difference between the diameters of the two barrels used must be at least 7-8 cm for the manufacture of reinforced rings and at least 15 cm for the manufacture of products without a reinforcing frame.
You have to make four parts of approximately the same shape as shown in the drawing:
The sequence of work is as follows:
- The bottom of both barrels is cut off, the inner barrel is made several centimeters higher than the outer one;
- Marking is made on a large barrel, dividing it by two vertical longitudinal lines into two equal parts. The markings should be both on the outside and on the inside;
- A steel angle is attached on both sides by welding or rivets along the marked lines. It can be solid, for the entire height of the cylinder, or three pairs of segments are welded to it exactly opposite each other (above, below and in the middle);
- Then holes are drilled in the corners for their subsequent fastening with bolts. You need to drill both corners at once at one time so that the holes match exactly;
- After that, the barrel is carefully cut from the inside along the marking line with a grinder with a thin circle so as not to damage the corners welded on the outside. The outer formwork cylinder is ready.
The inner cylinder is made in the same way, with the only difference that the corners are attached not to the outer, but to its inner wall.
Note! The smaller barrel is marked differently - so that one part is twice the size of the other. This is necessary so that when removing the formwork, it easily folds inward. Therefore, the distance between the marking lines should not be half of the circle, but its third.
For ease of use, handles can be welded to the formwork elements - outside on a large cylinder and inside on a small one.
To make the rings convenient to move during the construction of the well, drill through holes with a diameter of 4-5 cm in the walls of the formwork, into which wooden plugs will be inserted during the pouring of the mortar. After they are removed from the finished ring, eyelets for sling are formed.
Additionally, you can make metal spacers from reinforcement, put on the upper ends of the formwork to prevent the displacement of the rings during the pouring of the mortar.
How to make a concrete ring using a DIY mold
For the manufacture of rings, standard materials are required: cement, sand, crushed stone or gravel, water. They will turn out to be much stronger if they are reinforced with metal wire or rods.
So:
- It is advisable to use cement of a high grade (not lower than M400) and matured (produced at least a month ago);
- The mass fraction of sand should be 2-2.5 parts per one part of cement;
- The proportion of gravel is 3-4 parts;
- The proportion of water is 0.5-0.7 parts.
It is this ratio of components that ensures the maximum concrete density.
To prepare the solution, cement and sand are first mixed, poured with water, mixed, after which gravel pre-soaked in water is poured.
Council. It is desirable to be engaged in the manufacture of any concrete products at a temperature not lower than +8 degrees. The production site must be placed under a canopy or in a place protected from sunlight, since too rapid evaporation of moisture leads to a decrease in the strength of the concrete.
Further instructions are as follows:
- Place the mold on a flat hard surface or in a metal pallet, placing the outer and inner formwork so that the distance between them is the same along the entire circumference. Bolt the halves of each cylinder through the holes in the corners;
- Place a reinforcement cage welded from metal rods between the walls of the mold. You can also use a wire with a thickness of 2-6 mm, laying it in turns as it is poured into the form of concrete mixture;
- In the absence of metal spacers, make wooden wedges, the length of which is equal to the distance between the walls, and install them slightly above the average level between the cylinders in three to four places;
- Begin to evenly lay the solution into the mold, every 15-20 cm, making it compact in a circle with a thick wooden or metal rod (for example, a shovel handle). This procedure will replace the vibration used in the factory made rings;
- When the concrete level reaches the spacers, they must be removed and the filling of the mold continues to the edge of the outer ring;
- The last step is to carefully level the mortar over the top. The smoother the end part of the well rings, the easier it will be to join and seal them during the construction of the well.
Remove the formwork when the product gains sufficient strength. Depending on the ambient temperature and air humidity, this can happen every other day or after 3-4 days.
To remove, unscrew the mounting bolts, then first fold the smaller cylinder inward, then open the larger one.
After stripping, it must not be moved for several days. All this time, it is recommended to wet it with water to ensure the best concrete strength. It will be ready for use in 10-14 days from the date of manufacture.
Conclusion
By watching the video in this article, you can better understand how to make durable and high-quality concrete rings, from which you can build a water or sewer well. Of course, this, taking into account the independent execution of the formwork, will take quite a lot of time, but you will significantly gain in price and will be able to subsequently use the mold for casting new products for your friends and acquaintances.