Today, of the existing technologies for the construction of buildings and structures, the most promising is monolithic construction - is the construction of structural elements from a concrete-containing mixture using special forms (formwork) directly at the construction site.
An absolutely rigid frame is created with different kinds enclosing structures. In our country long years preference was given to prefabricated construction. Although it can be noted that in the 30s - the time of development of constructivism - there was experience in monolithic construction. Then there was the time of the "brick", panel house building was very actively promoted, and only in the last 10 years can we say that monolithic construction has taken its rightful place.
Monolithic construction in Kiev and Odessa - has always been complicated by the natural features of our country, as well as other "outdoor" work. But, monolithic concrete construction is gaining more and more popularity among compatriots. Moreover, this applies to both the construction of apartment complexes and monolithic construction of private houses... How do developers manage to cope with difficult weather conditions and, despite the whims of nature, remove monolithic construction in Kiev and Odessa to an ever higher quality level?
Monolithic construction in winter requires additional heating of sites not only to create comfortable conditions for workers, but also for high-quality solidification of the concrete mass. Winter monolithic construction is also convenient because with the onset of the warm season, the customer can personally take an active part in finishing works and decorating an already finished home.
In order not to reduce the strength of reinforced concrete structures, crystallization of the concrete mixture after pouring should be avoided. Heat guns of various power successfully cope with this task, which allows obtaining high-class reinforced concrete structures even in severe frost. Monolithic individual construction - also inevitably faces the obstacles created by the domestic climate. But, here - the scale of work is completely different, which means it is easier to cope with such troubles. Moreover, the monolithic construction of private houses in suburban settlements is mainly carried out after the closure of the "summer cottage". So there is less chance of quarreling with neighbors because of construction noise or a road broken by heavy equipment.
AT last years in Kiev and Odessa, along with prefabricated housing construction, where the production of basic load-bearing structures buildings is carried out at DSK and reinforced concrete factories, the method of monolithic housing construction, which allows you to make structures (walls, floors, columns, flights of stairs, etc.) directly on the construction site during the construction of the building. For this, various types of formwork are used.
Abroad (USA, England, France, Turkey, etc.) the volume of cast-in-place concrete buildings is 60-80% of the total construction volume. In Ukraine, according to various estimates, monolithic housing construction is still 10-15%.
The technical and economic analysis shows that in some cases, monolithic reinforced concrete is more efficient in terms of metal consumption, total labor intensity and reduced costs.
Building monolithic buildings compared to prefabricated houses allows you to reduce the one-time costs of creating a production base by 30-40% (reinforced concrete, reinforced concrete and DSK factories), reduce steel consumption by 10-20% (technological and assembly fittings in prefabricated structures), energy costs - by 30% (molding, steaming prefabricated products).
About 80% of the volume of monolithic concrete is used in industrial construction, mainly for the construction of structures underground parts buildings and structures and in the foundations for technological equipment. It is also used in the construction of heavy columns, various tanks, retaining walls, chimneys, cooling towers, energy facilities, complex arched and vaulted roofs.
In residential and civil construction, buildings are erected from monolithic concrete, characterized by complex, expressive plans and combinations of volumes of increased number of storeys. Monolithic concrete and reinforced concrete are widely used (also used in road, airfield, underground, overground, mine, hydraulic and water construction, three construction of bridges, port facilities and in many other areas.
The advantages of monolithic structures in comparison with prefabs, they are especially obvious for areas with an underdeveloped base for prefabricated housing construction (lower capital unit costs and the creation of a construction site), areas with high seismicity and difficult soil-geological conditions.
The main directions for improving the construction of monolithic buildings are:
- Minimization and technical equipment of manual processes;
- Application of industrial technological formwork;
- Introduction of specialized high-performance machines, mechanisms and equipment (concrete mixing and concrete pumping units);
- Extensive chemicalization of concreting technology and the use of effective building materials;
- Intensification of monolithic processes and an increase in the capacity of concrete works;
- Development effective ways winter concreting;
- Training of highly qualified personnel-monoliths.
The complex technological process of construction of monolithic buildings includes formwork, reinforcement and concrete work. The main processes of monolithic works include: installation and dismantling of formwork, installation, binding or welding of reinforcement and laying of concrete mixture.
The specifics of the construction of monolithic buildings
It is customary to distinguish by constructive types: monolithic and prefabricated monolithic buildings.
Buildings are called monolithic in which the main supporting structures (internal walls, columns and ceilings) are made of monolithic concrete. Fencing structures, flights of stairs, partitions, etc. can be prefabricated. The share of solidity should be 70% or more of the total volume of the building's structural elements.
Precast-monolithic buildings are called, in which some of the structures are made in a monolith, and the other in a prefabricated version. The share of solidity should be from 30 to 70% of the total volume of structural elements.
The organization of the technological process of erection of buildings from monolithic concrete creates great opportunities for creative searches and, due to the flexibility of shaping, allows to achieve the greatest correspondence of the architecture of buildings to their functional purpose.
Constructive solutions for monolithic buildings
Monolithic concrete buildings can be designed as a cross-wall structural system with load-bearing or non-load-bearing outside walls, transverse-wall, when only transverse walls are bearing vertical elements, or longitudinal-wall with bearing longitudinal walls (Fig. 1.1.).
Figure: 1.1. Frameless wall structural systems of residential buildings: a, b - cross-wall (with parallel and radial bearing walls); в - longitudinal-wall; d, e - cross-wall.
![]() |
![]() |
||||
![]() |
![]() |
![]() |
Using monolithic concrete almost any architectural idea can be realized. Monolithic concrete is the most "convenient" material for creating unique structures, large public buildings with complex functions and, accordingly, a complex, multifaceted structure. The flexibility of monolithic concrete in residential construction is primarily manifested in the possibility of free choice of planning solutions for buildings.
Residential buildings can be built without significantly complicating the construction technology different types: ordinary apartment, hotel type, dormitory buildings of boarding houses, etc. It is easy to achieve a change in the height of the floor in the monolith, which is very important for placement on the first floors non-residential premises and offices. In such premises, the span size and height can be taken in accordance with the functional requirements of the built-in enterprises.
Depending on the size of the span of the floor slabs, wall structural systems are divided into short-span (up to 4.8 m), medium-span (up to 7.2 m) and long-span (over 7.2 m). In the practice of housing construction, small-span and medium-span structural systems are used.
In buildings with transverse load-bearing walls, horizontal loads acting perpendicular to the load-bearing walls are perceived by separate stiffening diaphragms located in the longitudinal direction of the building, a flat frame due to a rigid connection of transverse walls and floor slabs, radial transverse walls with a complex building plan in plan.
In buildings with longitudinal load-bearing walls, horizontal loads acting perpendicular to these walls are perceived by separate transverse staircase walls, end walls and intersection walls.
In buildings with cross-bearing walls, horizontal loads, depending on the direction of their action, are perceived by longitudinal or transverse walls, and therefore this structural system allows the construction of the most durable, rigid and stable buildings. In terms of height and in terms of the building, the structural system can be regular and irregular. Regular systems include buildings with the same floor-by-floor arrangement of walls and openings, and irregular - buildings with vertical and horizontal structures different sizes and type (for example, on the first floors - columns, and on the overlying floors - walls; the building has an expansion or narrowing of the dimensions of the walls in height, their different heights, etc.). The choice of the structural system of the building in terms of ensuring strength and rigidity is carried out on based on static calculations and depends on the number of storeys, geological and soil conditions of construction.
The constructive and technological type of the building is associated with the method of its construction. There are two main and most common constructive and technological types of frameless buildings erected in removable (movable) formwork.
Buildings of the first structural and technological type
In buildings of this type, at the first stage, internal and external load-bearing walls are erected floor by floor, at the second stage, ceilings are arranged. The inner walls of such buildings are always monolithic single-layer, the outer walls are monolithic and prefabricated monolithic. For the construction of walls in this case, large-panel or block formwork is used (Fig. 1.2.).
Figure: 1.2. Erection of a building of the first structural and technological type in block and large-panel formwork.
Construction of a building of the first structural and technological type
in block and large-panel formwork (Fig. 1.2.):
- Large-panel formwork;
- Block formwork;
- Monolithic wall;
- Prefabricated floor slabs;
- Horizontal technological seam.
The ceilings used in buildings of the first structural and technological type, as a rule, are prefabricated from solid or hollow-core slabs. It is possible to use prefabricated monolithic and monolithic floors.
Buildings of the second structural and technological type
In buildings of the second type, at the first stage, load-bearing walls and floors made of in-situ concrete are erected simultaneously or sequentially. The outer walls are erected at the second stage.
With the simultaneous erection of walls and ceilings, volumetric-adjustable (tunnel) formwork is used (Fig. 1.3.)
Figure: 1.3. Erection of a building of the second constructive and technological type in volumetric-adjustable (tunnel) formwork.
Erection of a building of the second structural and technological type in a volumetric-adjustable (tunnel) formwork (Fig. 1.3.):
- L-shaped element of volumetric-adjustable formwork (half-tunnel);
- Traverse for lifting the formwork;
- Basement formwork installed on cross-shaped inserts;
- Cross-shaped insert;
- End slab formwork;
- End wall formwork;
- Projector;
- Formwork fixing bolts;
- Large-panel formwork of walls for the device of the end of the house;
- Work platforms;
- Work platforms;
- Telescopic stand;
- Infrared emitter;
- Fencing;
- Tarpaulin for covering the tunnel during concrete heating;
- Jack.
Internal walls are designed as single-layer monolithic, predominantly of heavy concrete. The compressive strength class of concrete is assigned on the basis of ensuring the strength of the walls is at least B15. The thickness of the walls is taken according to the results of the calculation for force effects and must meet the requirements of sound insulation. The minimum thickness of inter-apartment walls is 160mm.
Figure: 1.4. Reinforcement schemes for monolithic walls in buildings being erected.
Figure: 1.4. Reinforcement schemes for monolithic walls in buildings erected:
a) Under normal geotechnical conditions;
b) In seismic areas.
- Space frames installed at intersections of walls;
- Frames installed at the edges of openings;
- Armoblock from flat frames;
- Spatial framework of lintels.
Figure: 1.5. Diagrams of vertical butt joints of monolithic walls.
Figure: 1.5. Diagrams of vertical butt joints of monolithic walls:
a) Keyless;
b) With dowels evenly distributed along the height;
c) With discretely spaced through keys:
- Monolithic walls, concreted in the first place;
- Secondary concrete walls;
- Woven mesh razor, fixed to the frame;
- Horizontal reinforcement ties.
External walls can be made of single-layer monolithic aerated concrete with a density of up to 900 kg / m 3 with the obligatory installation of an external protective layer. The most widely used external walls of a three-layer prefabricated structure, which meet the requirements of SNiP 23-02-2003 (Thermal protection of buildings).
Examples of building envelopes
Figure: 1.6. Three-layer building envelope.
Overlappings are used monolithic, precast-monolithic and prefabricated.
Figure: 1.7. Three-layer building envelope.
Consisting of monolithic reinforced concrete (-0.18 m thick), heat-insulating material (polystyrene concrete blocks -0.3 m thick) and plaster (0.02 m thick).
- Polystyrene blocks;
- Monolithic reinforced concrete;
- Shotcrete (plaster).
Monolithic floors are calculated and designed as slabs supported along a contour or on three sides with a fourth free side for a unified load for residential premises.
Precast-monolithic floors represent a two-layer structure in the thickness of the slab: the lower layer is a precast slab (shell) 40-60 mm thick, used as fixed formwork; top layer - monolithic concrete 120-140 mm thick. The calculation of a precast-monolithic floor for a unified load for residential premises is carried out as for a solid monolithic slab. The prefabricated slab is made using steel formwork in polygon conditions from heavy concrete of class B15. the monolithic layer is made of heavy or lightweight concrete of class B12.5 or higher.
Prefabricated floor slabs are used: solid floor slabs and hollow-core decking.
Elevator shafts are made monolithic.
The stairs are made of unified prefabricated reinforced concrete flights and platforms, as well as in a monolithic design using a special formwork.
The popularity of monolithic construction
The popularity of monolithic construction in Kiev and Odessa quite understandable. Monolith - one of the most durable materials that allow the building to operate for over 200 years. This means that monolithic house - a reliable investment. Considering that real estate prices in Kiev and Odessa are constantly growing, and inflation still continues to "eat up" a significant part of our income, investing in individual monolithic construction - the most reasonable choice for a person who wants to save and increase the money earned.
But, of course, it is not only economic benefit that motivates people who decide building a house made of monolithic concrete... Building on your own land should bring joy to the future "landowner". Modern technologies allow giving monolithic walls, windows and ceilings, practically any shape... Accordingly, with this method of construction, you can not restrain your imagination and give yourself a dream home.
It is difficult to imagine the architecture of the 20th century without concrete and reinforced concrete. This material is able to bring to life the diversity of architects' creative fantasies. To implement original architectural ideas, you must have engineering and design experience.
This feature of modern architecture was noted by Alexander Vasilyevich Kuznetsov, the creator of the original reinforced concrete structures. He wrote: “An architect-artist with a scientific education. The architect will not be the spokesman for the era if he does not take advantage of the progress of modern technology in its entirety. Architecture is the harmony of science and art ”.
Currently, monolithic reinforced concrete in the structures of residential buildings of mass construction is increasingly replacing the prefabricated method of housing construction.
The main reason for the preference for the construction of buildings from monolithic concrete using the methods of modern construction technologies is the actual unlimited freedom to choose the configuration of the building plan and its volumetric-spatial solution.
Such houses noticeably stand out from the surrounding buildings with original plastic and non-standard solutions of facade planes, enriched with the structure of balconies and loggias (Fig. 3.10).
Often they combine various building systems, erecting not only purely monolithic houses, but also monolithic-panel, monolithic-brick.
The method of building buildings in precast-monolithic structures is widespread: - with monolithic load-bearing internal walls, ceilings and prefabricated three-layer curtain panels of external walls.
Typical series of 14-17-storey buildings have been developed with a pitch of load-bearing internal reinforced concrete monolithic walls 3.6 - 7.2 m.
Constructive solutions for monolithic buildings
Monolithic buildings are made in various versions of structural systems, depending on the solutions of the main supporting structures:
wall system with a small pitch of the bearing internal walls (option 1);
wall system with wide bearing spacing interior walls (option 2):
frame bezel-less system;
constructive girder-free system with bearing pylons;
structural transom system with supporting pylons;
frame system with box-type flat overlap.
Wall system with a small (wide) spacing of load-bearing walls (options 1 and 2).
With these structural schemes, the load-bearing structures are transverse solid walls made of monolithic concrete, located with a small (3.0 -3.6 m) or wide step (up to 9.0 m) (Fig. 3.11).
The location of the walls with a small pitch complicates the freedom of planning, especially in cases of apartment redevelopment.
The load-bearing internal walls are concrete plates operating in eccentric compression. They are reinforced with two nets interconnected with special reinforcing pins. A variant of reinforcement with vertical frames is possible, to which they are attached reinforcement mesh (Fig. 3.12).
Monolithic 24-storey house with an individual layout
2-19 floors
Combination rectangular shapes with semicircles and sharp corners
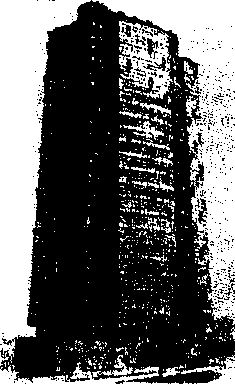
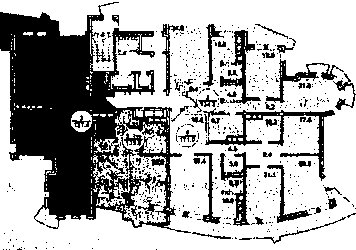
Figure: 3.10. Monolithic residential buildings
(Option 1)
Wall plan
Internal wall nodes 1-4
A wall system with a wide spacing of load-bearing walls is shown (Option 2) in Fig. 3.12
Wall plan
Option to reinforce the opening in the inner wall
The numbering of nodes 1-4 is shown in Fig. 3.11
Symbols of reinforcement products:
SV - reinforcing mesh of the inner wall
KG - bent frame
КР - design jumper frame
OS - individual rods
Figure: 3.12. Internal wall reinforcement nodes
Along the edges of walls and openings, vertical frames or bent rods are installed, welded to vertical grids. Bent rods are also placed at the intersections of the walls. During the process of erecting walls, the continuity of the reinforcement is observed.
Heat-insulating liners are laid in the outer walls of the attached loggias.
Monolithic slabs in a structural wall system work as continuous beam systems or as slabs clamped on three or four sides (Fig. 3.13). Reinforcement of floor slabs is performed with reinforcing (welded or knitted) meshes. The grids are laid in the lower section of the slab, and in the places where they rest on vertical walls - in the upper section. In places where the plates rest on the outer walls, heat-insulating packages are laid. Thermal insulation of the floor slab is observed when arranging loggias and balconies. In the structures of monolithic buildings, it is allowed to arrange floors from prefabricated panels (Fig. 3.14).
Frame structural system of the monolith represents freedom in the planning of residential premises, as well as the possibility of arranging non-residential areas (shops, cafes, restaurants) in the lower floors of buildings (Figure 3.15).
As well as in the wall system, the principle of continuous reinforcement is observed when erecting load-bearing structures. Columns are reinforced with vertical bars with closed clamps or vertical frames. Monolithic ceilings are reinforced between the columns with meshes and under the columns, designed for punching forces. Variants frame system serve as structural systems with flat pylons (flat columns) (fig. 3.16 and 3.17). They can be solved both with the device of crossbars in the floor plane, and without them. Just like frame systems, they have freedom of planning decisions, but they also have some disadvantages compared to the frame system:
columns replaced with flat ones sections of wallsmore advanced than
with a section of columns;
with the transom system, beams appear in the interior of the premises.
It should be noted that from the point of view of a constructive solution, the transom system has advantages over a non-girder system due to the simplification of the reinforcement of the floors, which does not require reinforcement of its above-column part.
The dimensions of the pylons range from 200-250x1200-1500 mm. The reinforcement of the pylons is assigned by calculation.
Frame system with flat overlap box type (Figure 3.18) is used with a large column spacing - 7.2x7.2 m or 9.0x9.0 m.
A flat floor slab with a height of 400 mm is a system of cross beams (ribs) with inserts of heat-insulating materials (expanded polystyrene, mineral wool, etc.) laid between them. The upper (60 mm thick) and lower (50 mm thick) planes of the slab are interconnected by ribs. The upper and lower plane of the slab is reinforced with structural meshes, and the edges are reinforced with welded or knitted frames. The main beams with a width of about 400 mm are placed along the axes of the columns and reinforced with working reinforcement. Secondary (additional) beams, going with a step of 600 mm, have a width of 120-150 mm, their reinforcement is constructive.
The frame system with a flat box floor has a high load-bearing capacity, good sound insulation properties and is quite easy to manufacture.
Wall system with a small pitch of load-bearing walls Option I Wall system with wide spacing of load-bearing walls Option II | ||||
h L L L L L L |
6 5 "5 5 5 5 o
Figure: 3.13. Floor plans of a monolithic building of a wall structural system
SECTIONS FOR REMOVAL OF LOGGIES, BALCONIES
Reinforcement of walls is conventionally not shown
Symbols of reinforcement products
LPG) mesh bottom overlap
SVP mesh upper overlap
FVG) background mesh top floor
Checkpoint - spatial overlapping frame
SGP - bent overlap bar
Option of a monolithic wall and overlapping loggia
Figure: 3.14. Floor details (monolithic reinforced concrete)
Typical floor plan Floor reinforcement option in the places where columns pass "TW |
■ "TS.) | |||
and upper r |
"Monolithic |
Column reinforcement is conventionally not shown
Diameter and spacing of reinforcement according to calculation
SG bent rods - clamps
OS - individual rods
Figure: 3.15. Frame beadless system
Typical floor plan
Figure: 3.16. Structural girder-free system with supporting pylons
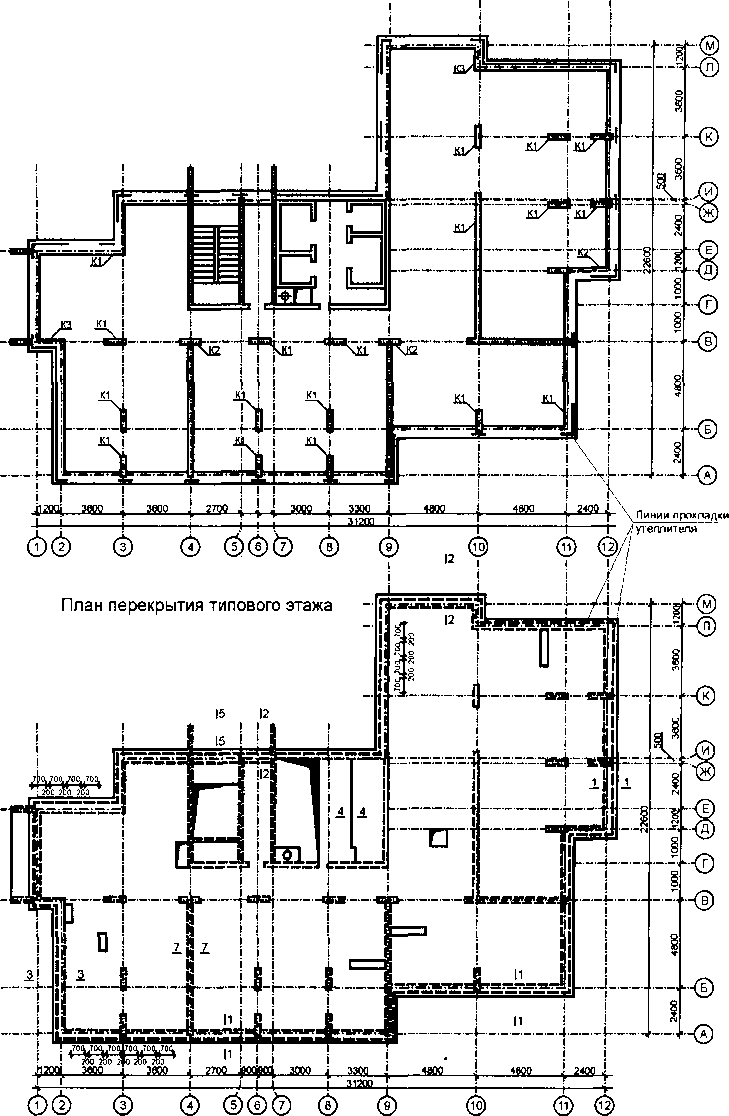
Typical floor plan
Floor plan of a typical floor
Pylon reinforcement scheme P1
Figure: 3.17. Monolith structural system with supporting pylons
Floor plan Fragment of a box section floor plan I I I rilliZII □ \u003d □ 1 L ““ “JS . 395^400 |
tfslLsoJhsQlWtfcl 595JJ4SoJJ45oiJ4SoJ. | |||
150 150 150 150 150 150 1 50 2080 J 3470 |
150 150 1650 \ . | |||
1.Specifics of the construction of monolithic buildings
It is customary to distinguish by structural types: monolithic and precast-monolithic buildings. Buildings are called monolithic in which the main load-bearing structures (internal walls, columns and floors) are made of monolithic concrete. Prefabricated can be enclosing structures, flights of stairs, partitions, etc. The share of solidity should be 70% or more of the total volume of the building's structural elements. Precast-monolithic buildings are called buildings in which part of the structures is made in a monolith, and the other in a prefabricated version. The share of solidity should be from 30 to 70% of the total volume of structural elements.
The organization of the technological process of erection of buildings from monolithic concrete creates great opportunities for creative searches and, due to the flexibility of shaping, allows to achieve the greatest correspondence of the architecture of buildings to their functional purpose.
1.1 Constructive solutions of monolithic buildings
Monolithic concrete buildings can be designed as a cross-wall structural system with load-bearing or non-load-bearing external walls, cross-wall, when only transverse walls are the load-bearing vertical elements, or longitudinal-wall with load-bearing longitudinal walls (Fig. 1.1.)Figure: I.1. Frameless wall structural systems of residential buildings:
a, b - cross-wall (with parallel and radial load-bearing walls); в - longitudinal-wall; d, d - cross-wall
Using monolithic concrete, almost any architectural idea can be realized. Monolithic concrete is the most "convenient" material for creating unique structures, large public buildings with complex functions and, accordingly, a complex, multifaceted structure. The flexibility of monolithic concrete in residential construction is primarily manifested in the possibility of free choice of planning solutions for buildings.
Without significant complication of the construction technology, residential buildings of various types can be built: ordinary apartment buildings, hotel types, dormitories of boarding houses, etc. It is easy to change the floor height in the monolith, which is very important for placement in the first floors of non-residential premises and offices. In such rooms, the size of the spans and the height can be taken in accordance with the functional requirements of the built-in enterprises.
Depending on the size of the span of the floor slabs, wall structural systems are subdivided into low-span (up to 4.8 m), medium-span (up to 7.2 m) and long-span (over 7.2 m). In the practice of housing construction, small-span and medium-span structural systems are used.
In buildings with transverse load-bearing walls, horizontal loads acting perpendicular to the load-bearing walls are perceived by separate stiffening diaphragms located in the longitudinal direction of the building, a flat frame due to the rigid connection of transverse walls and floor slabs, radial transverse walls with a complex building plan in plan.
In buildings with longitudinal load-bearing walls, horizontal loads acting perpendicular to these walls are perceived by separate transverse staircase walls, end walls and intersection walls.
In buildings with cross-bearing walls, horizontal loads, depending on their direction of action, are perceived by longitudinal or transverse walls, and therefore this structural system allows the construction of the most durable, rigid and stable buildings. In terms of height and in terms of the building, the structural system can be regular and irregular. Regular systems include buildings with the same floor-by-floor arrangement of walls and openings, and irregular systems include buildings with vertical and horizontal structures of different sizes and types (for example, on the first floors - columns, and on the overlying floors - walls; the building has an expansion or narrowing the size of the walls in height, their different heights, etc.) The choice of the structural system of the building in terms of ensuring strength and rigidity is carried out on the basis of static calculations and depends on the number of storeys, geological and soil conditions of construction.
The constructive and technological type of the building is associated with the method of its construction. There are two main and most common constructive and technological types of frameless buildings erected in removable (movable) formwork.
Buildings of the first structural and technological type. In buildings of this type, at the first stage, internal and external load-bearing walls are erected by floor, at the second stage, overlappings are arranged. The inner walls of such buildings are always monolithic one-layer, the outer walls are monolithic and prefabricated monolithic. For the construction of walls in this case, a large-panel or block formwork is used. (Fig. 1.2.)
Figure: 1.2. Erection of a building of the first structural and technological type in block and large-panel formwork: -
1- large-panel formwork;
2- block formwork;
3 - monolithic wall;
4 - prefabricated floor slabs;
5 - horizontal technological seam
The ceilings used in buildings of the first structural and technological type, as a rule, are prefabricated from solid or hollow-core slabs. It is possible to use prefabricated monolithic and monolithic floors.
Buildings of the second constructive and technological type. In buildings of the second type, at the first stage, load-bearing walls and floors made of in-situ concrete are erected simultaneously or sequentially. The outer walls are erected in the second stage.
With the simultaneous erection of walls and ceilings, volumetric-adjustable (tunnel) formwork is used (Fig. 1.3.)
Figure: 1.3. Construction of the second constructive building
but-technological type in volume-adjustable (tunnel) formwork: 1 - L-shaped variable volumetric element formwork (half-tunnel); 2 - traverse for lifting the formwork; 3 -basement formwork to be installed on cruciform inserts; 4 - cross-shaped insert; 5 - end floor formwork; 6 - endwall formwork; 7 - openingeducator; 8 - fasteners formwork bolts; nine -large-panel formworkwall for torus devicetsa at home; 10-11 - workerssites; 12 - telescopeak rack; thirteen -infrared emitter; 14- fencing; 15 - tarpaulin for covering the tunnel during concrete heating; 16 - house foldInternal walls are designed as single-layer monolithic, predominantly of heavy concrete. The compressive strength class of concrete is assigned on the basis of ensuring the strength of the walls is at least B15. The thickness of the walls is taken according to the results of the calculation for force effects and must meet the requirements of sound insulation. The minimum thickness of inter-apartment walls is 160mm.
Fig. 1. 4. Schemes of reinforcement of monolithic walls in buildings erected:
A) - in normal engineering and geological conditions; b) - in seismic regions. I - space frames installed at the intersection of walls; 2 - frames installed at the edges of the openings; 3 - armored block made of flat frames; 4 - spatial framework of lintels
Figure: 1.5. Diagrams of vertical butt joints of monolithic walls:
a - keyless; b - with dowels evenly distributed along the height; c - with discretely located through keys: 1 - monolithic walls, concreted in the first place; 2 - walls to be concreted in the second stage; 3 - cutter made of woven mesh, fixed on the frame; 4 - horizontal reinforcement ties
Exterior walls can be made of single-layer monolithic aerated concrete with a density of up to 900 kg / m3 with the obligatory installation of an outer protective layer. The most widely used external walls of a three-layer prefabricated structure, which meet the requirements of SNiP 23-02-2003 (Thermal protection of buildings).
Examples of building envelopes :
Figure 1.6. Three-layer building envelope. 1). Consisting of aerated concrete (-0.4 m thick), heat-insulating material (expanded polystyrene with a thickness of -0.1 m) and facing brickwork (thickness -0.125m) 2). Three-layer building envelope. Consisting of internal brickwork (-0.25 m thick), heat-insulating material (mineral wool plate -0.1 m thick) and facing brickwork (-0.125 m thick).
Overlappings are used monolithic, precast-monolithic and prefabricated.
Monolithic floors are calculated and designed as slabs supported along the contour or on three sides with a fourth free side for a unified load for residential premises.
Precast-monolithic floors represent a two-layer structure in the thickness of the slab: the lower layer is a prefabricated slab (shell) with a thickness of 40-60 mm, used as a permanent formwork; the top layer is monolithic concrete 120-140mm thick. The calculation of a precast-monolithic floor for a unified load for residential premises is carried out as for a solid monolithic slab. The prefabricated slab is made using steel formwork in polygon conditions from heavy concrete of class B15. the monolithic layer is made of heavy or lightweight concrete of class B12.5 or higher.
Prefabricated floor slabs are used: solid floor slabs and hollow-core decking.
Elevator shafts are made monolithic.
The stairs are made of unified prefabricated reinforced concrete flights and platforms, as well as in a monolithic design using a special formwork.
Figure: 1.7. Three-layer enclosing structure. Consisting of monolithic reinforced concrete (0.18m thick), thermal insulation material (polystyrene concrete blocks 0.3m thick) and plaster (0.02m thick)
1-polystyrene blocks,
2-monolithic reinforced concrete,
3-shotcrete (plaster).
If in the announcement of the sale of an apartment we see the phrase monolith-brick, then it means a building that was not built, but cast from concrete. Brick in such a house is used mainly as a facing material, and also sometimes for the construction of interior walls.
According to experts, the principle of monolithic construction in Russia has been used since the beginning of the last century, but it is being improved all the time, and modern monolithic buildings bear little resemblance to houses with a century of history. The main difference between modern buildings is in the formwork, which is used to "fill" monolithic walls; as concrete and monolith filling. At the dawn of monolithic construction, formwork was usually disposable. It was knocked together from unplanned boards, concrete mortar was poured into the formwork, and then the boards were torn off from the frozen monolithic wall.
Later, the process was slightly improved: they began to put together plank shields, which were enough for several times. In the middle of the last century, they also approached concrete fillers in a very indiscriminate way. So, in the mining regions, monolithic buildings were built, the walls of which are a mixture of concrete and overburden rock, which (as it has now become known) has a slightly increased radioactive background. During the period of "Khrushchev" and "Brezhnev" panel construction, monolithic houses were built less often, but now they are again winning a solid segment of the market from brick and panel buildings. Now on the market in a wide range of different types of formwork, including multifunctional structures.
Construction of walls and floors
Experts note that plastic formwork should be attributed to the most multifunctional building systems, since the same structural elements formwork is suitable for filling walls, columns, floors, beams and other supporting supports and structures of a building. Figuratively speaking, reusable plastic formwork is a "Lego constructor", from which you can quickly assemble and securely fasten any shape. The individual formwork modules can be connected in different shapes so that narrow cavities remain inside the "constructor". Fittings are installed in them and concrete mortar is poured. And when the concrete dries up, the formwork is removed from the finished monolithic walls, after which the formwork is installed for the construction of the next wall or floor.
In order for the structure to comply with building codes, the "jellied" walls and ceilings must be securely joined together. For this purpose, during the construction of the wall, long reinforcement rods are taken out of the boundaries of the formwork: the reinforcement is obtained longer than the section of the wall prepared for pouring. As a result, long metal rods protrude from the finished monolith. Their bases are carefully "wrapped" with special tabs, for example, made of PVC, so that when the next section is poured with concrete, a cavity remains around the rods. In the future, this will make it possible to connect vertical reinforcement with horizontal - one that will be laid "with a margin" in monolithic floor slabs... In a similar way, formwork is assembled, intended for pouring floors.
It turns out a shallow "trough" of a large area, as a rule, "covering" a section from one load-bearing wall to another. Of course, the formwork is designed in such a way that horizontal monolithic slabs lay flat on the main walls of the building, taking into account the load, which engineers, of course, scrupulously calculate at the design stage. A frame made of reinforcement is laid in the formwork. At the intersection of the horizontally laid reinforcement with the vertical one, the rods are firmly connected to each other, after which the joints are poured with concrete. Experts believe that in monolithic construction, it is impractical to weld fittings, since chemical composition welded metal reacts poorly with liquid concrete mortar... Therefore, reinforcement rods are often tied together with strong wire, although other ways of connecting vertical and horizontal reinforcement are possible.
Of course, in future walls, before pouring concrete into the formwork, it is necessary to reconsider the openings for windows and doors. For this purpose, as a rule, rectangles are hammered out of boards, which correspond in size to the design shape of doors and windows. The boards must be tightly fitted "under the formwork" so that the concrete does not "seep" under pressure into the window and door openings. However, some formwork models are equipped with special reusable inserts for these purposes, which are installed in the places provided for by the project, and then, when the concrete has hardened, removed.
Also, the technology of monolithic housing construction, as a rule, provides for vertical openings intended for joining external walls with internal monolithic partitions. Many construction systems are conceived in such a way that the formwork is first installed on the lower floor, and then, as the concrete is poured and the monolith hardens, the formwork system is lifted and installed on the floor above. Similarly, they act in the case when the building has, for example, the shape of an elongated rectangle. The formwork is first moved in stages along the wall, and then vertically.
When the formwork is installed, the reinforcement is laid, a mixer drives up to the construction site. With the help of hoses, the concrete pump pumps the mortar to a sufficient height, which, according to experts, can reach 40 meters. The cavity inside the formwork is filled with concrete mortar - from top to bottom. In this case, it is necessary to ensure that there are no lumps in the solution. The surface of the formwork is pre-treated with a special lubricant so that it can be easily removed after the concrete has hardened. Experts warn that the concrete solution "does not like" when snow gets into it - this affects the quality of the concrete. But frosty weather does not interfere with the creation of reliable monolithic structures. For this purpose, for example, not only reinforcement is laid in the formwork, but also heating cable... When the concrete is poured into the formwork, the cable is turned on for a while. Due to the optimal temperature, the water in the concrete solution does not freeze, and the hardening process takes place in the optimal mode. The cable is then disconnected. It solidifies inside the concrete, and becomes part monolithic construction.
The composition of the concrete solution is mixed in accordance with the project. Sometimes additives are provided, for example, expanded clay, which reduce the strength of the monolith, but improve the thermal insulation properties. Experts emphasize that engineering calculation of monolithic walls is necessary, even when a one-story house is being built. The load-bearing capacity and thermal insulation properties of the walls must be balanced and accurately calculated. Sometimes the main non-bearing load is placed on the columns and ceilings, and the walls are “diluted” with heat-insulating fillers.
According to experts, monolithic walls and ceilings, which are assigned the role of load-bearing structures, are usually reinforced with reinforcement. Inside a building, walls are often made of lighter materials, such as panel or block materials. And the outer walls in the "monolithic" house are also panel. Often, the columns and floors of buildings are made monolithic, that is, the supporting main frame, and panels are "hooked up" to it as external and internal walls. Also on the monolithic supporting structure can be hung metal carcass and thermo-structural sandwich panels are put on. Then, a suspended facade is mounted on the building (for example), and a monolithic-panel house is obtained.
At the same time, buildings are widespread and in good demand, about which in the ads they briefly write "monolith-brick". It is understood that such a building is cast from concrete with the help of formwork, which, solidifying, has become a monolith. Then the monolithic building is faced with brick, which not only adds external charm, but also protects from the cold in winter and from the heat in summer. Other external fencing of a monolithic building is also possible. For example, with the use of a hinged facade system and "filling" of heat-insulating material.
Disadvantages of monolithic housing construction
According to experts, the main problem construction of monolithic buildings is that the entire technological cycle takes place outdoors in the open air. And since most of the year in our area is winter and autumn-spring, respectively, the quality of the structures being erected may suffer due to frost and precipitation. According to technological requirements, concrete should be laid at a temperature of no more than five degrees. At lower elevations, the solution of water, cement and fillers solidifies "incorrectly", as a result, the quality of concrete and the reliability of the structure deteriorate. If the concrete hardens in a severe frost, then the water will freeze, the wall will increase in size, the monolith will not only lose its strength properties, but can damage the formwork.
They try to solve this problem in various ways. As mentioned above, a heating cable is laid inside. According to experts, cable heating not only increases the cost of the project, but also leads to some drying out of water in the solution. As a result, deviations from the technological regulations are possible. Sometimes, even at the stage of concrete preparation, special additives are mixed into the solution, which prevent water from freezing and preserve the strength properties of the monolith, which "happened to be petrified" in frosty weather. Other methods of warming up are also possible. For example, initially heated crushed stone or other filler is kneaded into a concrete solution. Sometimes, right at the construction site, the concreted area is fenced off with "walls" made of cellophane or other inexpensive film, and then heat guns are turned on.
Different types of formwork
Formwork, intended for the construction of monolithic buildings, is produced in various shapes, made of metal or plastic. Any formwork structure consists of a particularly rigid frame and deck. The shape of the deck determines the shape of the monolithic structure. According to experts, plastic formwork has a number of advantages. One of the main advantages of plastic is its light weight. For the installation of plastic formwork, lifting mechanisms are not required (in any case, they can be dispensed with). Moreover, for the installation of plastic formwork, on average, it takes half as many people as for working with a metal analogue. (If we take for comparison the same volume of concrete intended for pouring into the formwork). However, the number of working hands required to install the formwork determines not only the material from which the structures are made, but also the functionality of the individual elements of the system. The market offers a wider selection of different types of formwork. Of course, the usability of designs depends on many factors. These include the method of fastening the formwork, standard sizes, the versatility of individual structural elements and the possibility of using the same formwork system for the construction of walls, floors, foundations and other parts of the building.
According to experts, plastic formwork is good in that it allows you to give material embodiment to the high flight of architectural thought. That is, it is easier to cast intricate concrete curves, vaulted ceilings and other complex shapes using plastic formwork. In particular, interesting is the coffered plastic formwork, which allows you to create extraordinary lines of ceiling arches. It is curious that many of the formwork bends that give originality to dome structures are at the same time stiffeners, that is, elements that reinforce the structure. Metal formwork is no less common. In particular, formwork panels are made from aluminum profiles and steel components. Metal shields are often sheathed with multi-layer moisture-resistant plywood, and the joints with the frame are treated with a sealant. According to experts, it is easier to organize the production of metal formwork than plastic formwork, therefore it is widely represented on the domestic market. Despite the high strength properties of metal formwork and other advantages, on average, it costs less than plastic.
Formwork structures are characterized not only by the quality of the material, but also by the technological features of the use of systems. Formwork can be large-panel and small-panel, they also differ in the way they are removed from the frozen monolith. In particular, formwork can be vertically and horizontally retrievable, tunnel, sliding and others. Also, the formwork is characterized by the "transport mechanism": they can be self-lifting, climbing-climbing, lifting. According to experts, the main criterion for evaluating a formwork system is its manufacturability during installation and dismantling, as well as the versatility and multifunctionality of individual structural elements. In addition, there are disposable formwork made of chipboard, thermal insulation or other materials that solidify with the concrete and remain in the monolithic walls.
One of the main approaches when choosing the technology of monolithic construction and the type of formwork is the architectural forms of the future building, its purpose. For example, according to experts, for the construction of a hospital, dormitory or hotel (that is, buildings in which a corridor system is provided), it is advisable to use tunnel formwork. The main building element is a "half section" consisting of one vertical and one horizontal panel. Three parallel tunnels, with openings for doors and windows, are broken by internal partitions, and get a building with a corridor system.
Fixed formwork
A variety of monolithic buildings are houses, often low-rise, built “on the basis of” fixed formwork, which is constructed from heat-insulating materials. The principle of erecting such structures is generally the same as in the construction of "ordinary" monolithic houses, but there are some peculiarities. The plus is the speed of construction of the facility: after all, the formwork does not need to be removed, and time and material costs are not required for thermal insulation of the building. In addition, foundation costs are reduced as the insulating frame is lightweight. However, "heat-insulating-monolithic" buildings have disadvantages. A "light" building with a relatively weak foundation is not able to withstand heavy loads, which means that we are not talking about the construction of serial apartment buildings. More often, "light monoliths" occupy a niche in low-rise individual construction. In addition, a rigid interior and exterior finishing of the building is required, as otherwise dents will appear on the "heat-insulating" walls. The location of thermal insulation materials on the inside of the walls is undesirable for residential premises (usually thermal insulation is laid on the outside), which means interior decoration you need to "strengthen" in order to protect people from the "harmful factor".
There is one more piquant drawback of such buildings - they are partly "edible". Some types of rigid insulation materials are eaten by rodents, and therefore the house may be partially eaten. And the very encroachments on the walls of the building, suggesting invasions of rodents, will also not please all owners. According to experts, the most widely used formwork is from expanded polystyrene blocks. At the same time, chipboard and cement-chipboard panels have a “place in the sun” as permanent formwork. Also in construction, other types of permanent formwork are used, for example, hollow concrete blocks. According to experts, such formwork is quite suitable for the construction of multi-storey buildings. To give the structure reliability, reinforcement is laid in the hollow concrete blocks. Usually, individual sections of the building are reinforced, which are assigned the load-bearing function. However, reinforcement is also used in low-rise construction for the construction of monolithic buildings, when heat-insulating plates are used as fixed formwork.
According to experts, there are advantages in using permanent formwork from chipboard and cement-chipboard. The main advantage is the ability to provide serial production of "semi-finished products" at the factory. In particular, hollow panels “built” of chipboard slabs are filled with fittings or electrical wiring at the plant, if the project provides for the function of a box for this panel. Thus, the "stuffed" formwork is delivered to the construction site, then the panels are joined together using special locks and poured with concrete. This organization of labor accelerates the pace of building construction. True, it is advisable to insulate monolithic houses with a chipboard or cement-chip frame, since wood-based panels are not thermal insulation materials... But for the interior of the building, the surface of the chipboard (i.e. formwork) is good because it does not need additional processing: the surface of the panel is fully prepared for painting or wallpapering.
The formwork from expanded polystyrene plates is made in the form of panels and in the form of blocks. The latter option, according to experts, is the most common. The block consists of two slabs connected by special ties. When using formwork blocks made of expanded polystyrene, the cavities are “stuffed” with reinforcement right on the construction site. Typically, the vertical pins are overlapped and wired securely. In order to strengthen bearing capacity structures select more "strong" grades of concrete (which is poured into the formwork) and reliable reinforcement. Ventilation boxes and electrical wiring are laid in the cavities of the permanent formwork before it is poured with concrete. Usually, a block formwork system is made in such a way that it includes several standard sizes, as well as corner blocks, end caps and other structural elements. Blocks are relatively small "parts" of the formwork, but panels are usually produced in a floor height and two to three meters long. The panels are partly left hollow for laying communications. They are installed as formwork, and then "stuffed" with reinforcement right on the construction site and poured with concrete.
Galina Pork