Warmth is one of the prerequisites for comfort and home coziness. To insulate the floor in wooden house was as efficient as possible, certain technologies must be observed. You can do the work yourself or contact the services of professionals
Cold floor reasons
There are several reasons for a cold floor:
- slit in the floor;
- poor tightness of the space under the floor;
- poor thermal insulation of the foundation.
Regardless of the cause, the consequence is the formation of moisture accumulations inside the floor material. The floor covering is deformed: paintwork material peels off, laminate, chipboard practically crumble. Carpet, resistant to deformation, linoleum just blacken. Wet spots covered with black mold appear on the walls, destroying the wood - it begins to rot.
How to insulate the floor in a wooden house
Do-it-yourself floor insulation measures are best carried out in a complex: foundation, basement, floor itself.
Foundation
Insulation of the foundation in a wooden house
External insulation allows you to avoid a lot of troubles associated with a shift in the dew point - high humidity inside the basement, the formation of condensation on the surfaces of its walls.
You can insulate with expanded clay, or with insulation - foam, mineral wool. The most expensive, but the most reliable option is brick and stone cladding.
First, a trench is dug around the perimeter of the house: the depth is about 80 cm, the width is half a meter. The surface of the foundation structure is thoroughly cleaned of dirt, and the necessary restoration measures are taken. Then it is treated with moisture-proof, antiseptic liquids.
Expanded clay
Insulation of the foundation in a wooden house with expanded clay - a detailed diagram
The bottom of the trench is compacted. On sand pillow (about 10 cm) a waterproofing sheet is laid - roofing material, film materials.
Important! When deciding to save money using an inexpensive plastic wrap, it is better to give preference to a two-layer canvas.
Expanded clay (about 60 cm) is poured on top, which is also covered with a waterproof material.
Styrofoam, mineral wool
Insulation is attached to the outer surface of the foundation adhesives, screws, dowels. The type of fastener is selected depending on the selected type of insulation, base material.
For fixing the finish - plaster, siding, a reinforcement system (mesh) or lathing made of a bar, galvanized profile is attached to the above-ground part of the foundation.
A layer of sand is poured onto the compacted bottom of the trench - about 15 - 20 cm, then a layer of gravel - about 50 cm.
Brick or stone
The compacted bottom of the trench is covered with a sand and gravel bed - 10 cm of sand, 15 cm of gravel. The sand layer is leveled, compacted - spilled with water.
Then the reinforcement grid is laid.
Important! When deciding to connect the elements of reinforcement by welding, you should purchase a rod bearing the letter "C" in the marking.
Flooded concrete mortar... It is desirable that the surface of reinforced concrete rises above the ground by at least 20 cm.
After the concrete hardens, the formwork is removed, the entire structure is covered around the perimeter with a double layer of roofing material - the fold outward.
The masonry can be 1 - 1.5 bricks. The distance between the old basement and the new one is filled with sand, expanded clay, sawdust or slag during masonry work every 3 to 5 rows.
Regardless of the option chosen on final stage along the perimeter of the building, concrete is poured or tiles are laid.
We insulate the basement
When insulating a basement, it should be borne in mind that perfect tightness is also not useful to the building structure. Therefore, ventilation must be provided at the same time.
Advice! An inexpensive household fan inserted into the air vent will improve its operating conditions.
Regardless of what the basement surfaces will be insulated with - foam, mineral wool, they must be thoroughly cleaned of dirt, treated with water-repellent, antiseptic agents - mastics, liquids.
For fastening fibrous materials, you will need a crate, a vapor barrier sheet. If foam insulation is planned, then its sheets can be attached with ordinary "fungi".
We insulate the wooden floor in the room
If the insulation of the foundation and basement is difficult for any reason, for example, late autumn, you can start work in living roomsoh. Usually, floor insulation in a wooden house is carried out with light materials:
- expanded clay;
- foam;
- sawdust;
- mineral wool.
We insulate the floor in a wooden house with our own hands
Remove all layers of the old flooring to the base. The base itself is carefully tidied up. All cracks are closed with putty, polyurethane foam, wooden inserts.
The surface is leveled, treated with antiseptics. Then the waterproofing material is laid - approaching the wall up to 20 cm.
About every half a meter, a timber - logs are mounted. The space between the timber is filled with the selected insulation.
Important! If you plan to do it yourself with foam, mineral wool, then the distance between the lags should correspond to the size of the insulation plates.
When backfilling with expanded clay, sawdust, slag, you need to pay attention to their condition - bulk materials should be dry, without debris, signs of mold, rot.
Wood is a "living" material, so the insulation is covered from above with a vapor barrier membrane.
Then a board, chipboard, OSB, moisture-resistant plywood is laid on top.
How to choose insulation
Each material has its own pros and cons. The only insulation that is not recommended for do-it-yourself floor insulation is fiberglass. Working with him involves the use of a full range of personal protective equipment - gloves, mask.
- Polyfoam - easy to install, moisture resistant, so you can save on vapor barrier. Minus - warm material rodents like it too.
- Basalt fiber (mineral wool) is environmentally friendly, almost non-combustible. No cases of detection of mouse nests in "stone" wool were recorded. Minus - a vapor barrier layer is required.
- Sawdust - "old-fashioned" insulation. Eco-friendly, hygroscopic, but flammable, loved by insects and rodents. They dry out over time, a bedding is required.
- Slag. Used extensively in soviet era... Does not burn, is not damaged by rodents, has bactericidal properties.
- Expanded clay. Light hygroscopic material, no serious drawbacks.
A common disadvantage of all bulk materials is shrinkage. Therefore, when using them in vertical insulation systems, it is necessary to provide for the possibility of adding - after 20 years.
Sometimes owners of private houses prefer to start floor insulation with internal work, trying to save money. To be convinced of the incorrectness of this approach, it is enough to look back in the recent past.
In old village houses on wooden piles with a plinth - two layers of planks and backfill with sawdust, the floor was one layer! No "rough" options! The upper, planed surface served as the floor in the room, and the lower, unprocessed surface, served as the “underground” ceiling. We walked barefoot on such a floor in winter! published
27.06.2016 0 commentsAll efforts to insulate capital walls come to naught if neglected physical phenomenonpresent in every heated room - by the presence of convection (ascending) air flow. It is perceived as wind and reduces the subjective assessment of comfort. The insulation of the house ceiling cannot stop it, since this would contradict the laws of Nature, but it significantly reduces the speed of the convection flow, and the house becomes noticeably warmer.
In contact with
Classmates
Process physics
Do-it-yourself insulating floors is a feasible task for any home craftsman. But for it to bring tangible results, it is worth understanding the physical processes that you are trying to resist. It is also important because they consist of interconnected parts. For example, if you insulate only the attic floor, but do not do it with the floor, then the convection flow will only intensify - it will become warmer under the ceiling, but at the level of the lower floor the temperature will remain the same.
Therefore, the goals of insulation interfloor overlap, laid out on wooden beams, differ depending on its location. This also dictates the need to use different materials for insulation and technology of their laying.
- Overlap of the first floor (floor) - the temperature on its surface as a result of the work should increase by 1-2 degrees, and the insulation also plays the role of a sealant, preventing cold air from sucking from the unheated underground.
- Interfloor ceiling - reflects radiant energy, plays the role of sound insulation.
- Attic floor - also reflects radiant energy, but soundproofing properties fade into the background if the next room above it is non-residential.
It should also be borne in mind that the convection flow captures mechanical particles (dust) and substances emitted by the insulation, which can be poisonous.
Types of heaters
Thermal insulation of interfloor overlap on wooden beams is carried out taking into account thermal insulation, mechanical and chemical properties insulation.
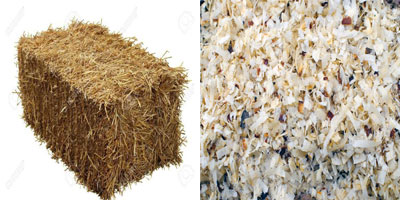
Insulation technology
Wooden interfloor floors are the most common option in individual housing construction. Their design is the same in both wood and aerated concrete house... It is a plane with stiffening ribs, between which the material used for insulation is laid. The floor plan of the house is shown in the figure below ( fig. 6).
When arranging attic and basement floors, the beams are usually left unshielded on one side, which makes adjustments to the technology of the work performed - for floor insulation with bulk and slab materials (expanded clay, mineral wool), an additional raised floor is required between the beams. But you are free to choose the type of material yourself, based on knowledge of their properties.
Floor insulation
For these works, it is best to use polyethylene foam. All work is carried out from the underground. A piece is cut from the roll, equal to the length of the gap between the beams. It is most convenient to fix it with a construction stapler, using staples with a height equal to two thicknesses of the material. It is impractical to use foil-clad material - there is no source of radiant energy in the subfield.
Insulation of interfloor ceilings
Insulation between floors should play the role of sound insulation, so the use of foam for this purpose is undesirable. The best way - mineral wool or expanded clay .
Expanded clay backfill ( fig. 7) may be too heavy. So that she does not tear off the ceiling material in the lower room, slats with a section of 2 by 2 cm are nailed onto the beams. Boards are laid out on them, which will serve as the basis for it. Waterproofing is not required, but geotextile (non-woven material) must be laid on top of expanded clay to prevent dust from entering the room.
Mineral wool ( fig. 8) requires waterproofing both from above and from below (the air coming from the lower floor is saturated with moisture). As an original waterproofing solution that allows you to combine business with pleasure, between the beams, directly on the ceiling boards of the lower floor, foamed polyethylene foam is laid (with the foil down). Mineral wool can be placed directly on top of it if it is a roll material. The slab is denser and heavier. Therefore, it is necessary to act in the same way as in the case of expanded clay - to nail the cranial bars and lay a board crate on it. Then between the foam foam layer and the overlap, there will be a space required for the foil to reflect the radiant energy. Without this condition, it will not work.
Cover the top with mineral wool with foil. It plays the role of waterproofing, and also prevents mechanical particles (fiberglass) and volatile substances from the impregnation from entering the room. The film can be either ordinary or membrane, allowing steam to pass in one direction. It is laid with the side impervious to water upwards, towards the floor fig. 9).
Insulation of the attic floor
Thermal insulation of the attic interfloor overlap on wooden beams crowns all the work. The amount of fuel consumed for heating largely depends on its quality - more than half of all heat goes through these gates.
If the attic is not heated and the floor is non-residential, then sawdust can also be used for thermal insulation ( fig. 10) - a large open area guarantees their complete drying. But it is better to use this material as an additional one, and foam will be the main one ( fig. 11).
A layer of foil-clad polyethylene is laid first. The polystyrene is light, so the cranial bars can not be nailed to the beams and the additional crate can not be arranged. Foam plates are laid on top of them, the joints - including with the walls - are filled with polyurethane foam, as a result of which a continuous heat-insulating coating is formed without seams. If cheap packaging foam is used (balls are visible on the breakage), then a layer of sawdust is poured over it, which not only increases the thermal insulation properties, but also protects the expanded polystyrene from the damaging effects of sunlight. Extruded construction - bubbles-polyhedrons are visible on its cut - more resistant, but it will not hurt to sprinkle it with sawdust.
In the attic on top of the insulation, plank ladders are necessarily arranged so that you can walk without destroying the structure and without trampling the heat-insulating layer.
The proposed technology for insulating floors has been tested in practice and gives good results.
In contact with
A house built with your own hands is the pride of every owner. In such a house, everything is done for a comfortable and comfortable life... To keep it warm and comfortable in any weather, you should carefully consider all stages of construction, especially laying the floor. It should be warm in a frosty winter and cool in a hot summer in a wooden house.
Even the most professional and high-quality work on laying the floor leaves small gaps between the boards, which inevitably leads to heat loss, and also disrupts the air circulation under the joists, which is necessary in wooden structure... Up to 30% of the heat is emitted through such slots, which will significantly lower the room temperature and increase the energy consumption for heating.
There are several options for eliminating such defects. You can use additional coverage, thereby quickly and inexpensively solving this problem. Simply laying linoleum or carpeting will not solve the problem. The disadvantages of this step are fragility and relatively low efficiency. A more cardinal and decisive approach is to independently engage in floor insulation using modern thermal insulation materials... To choose a method of insulation, one should take into account the design features of the house, climatic conditions and some temperature parameters.
Insulation of the floor between wooden joists
Uncomplicated and enough effective method, which is quite possible to carry out on their own without the help of specialists. Well suited for both private and multi-family residential buildings.
Selection of material and calculation of its required thickness
Before you buy a material for thermal insulation, carefully study the existing range. Of great importance here will be what it is made of, standard sizes, properties, brand-manufacturer. Keep in mind that the material in the mats will be more dense and resilient than the rolls. Consider the thermal conductivity of the material, its specific gravity, shape stability and vapor permeability. Many manufacturers place this information on their product packaging.
We'll have to apply several formulas. Calculation of the required thickness of thermal insulation \u003d RxA. Values \u200b\u200bfor the coefficient R (total thermal resistance building structure), can be found in the tables to the SNiP appendix "Thermal protection of buildings". Building codes are a set of basic regulatory requirements and regulations. There you can see all the values \u200b\u200bof interest. For example, the value of the thermal conductivity coefficient is A. The collection of all parameters should be carried out taking into account the requirements of SNiP. It is necessary to calculate the parameters of the permissible floor load. In the tables, you will also find values \u200b\u200bfor calculating the so-called temporary loads (furniture, equipment, people and animals). The total height of the entire structure is calculated. Humidity and temperature inside the house are taken into account. You can also use an online calculator for the calculation.
The main stages of floor insulation work
- Installation of a structure with wooden joists on a leveled floor surface
- Installation of waterproofing and rough flooring from boards or shields
- Laying insulation between logs (filling joints with polyurethane foam or sealant)
- Laying material that provides reliable vapor barrier
- Manufacturing of wood flooring, on which the final finishing coat can then be mounted.
The layer of insulation is “sewn up” between the layers of waterproofing and vapor barrier.
The vapor barrier will protect the thermal insulation from the formation of condensation and steam from the inside of the room. The material for the vapor barrier is a film that is additionally fixed with a special metal tape. There are the following types of film vapor barrier: polyethylene and polypropylene.
When used for wooden floors, the film needs an air gap.
Polyethylene film vapor barrier
- Perforated film (can be used as a waterproofing agent)
- Non-perforated film (for vapor barrier in wooden houses, not tear resistant)
- With an aluminum layer (for rooms with high humidity)
- Reinforced (a reinforced layer is placed between two layers of polyethylene)
Polypropylene vapor barrier
- Non-reinforced film (cheap but not practical material)
- Reinforced film (viscose and cellulose - additional reinforced reinforced layer). During installation, it is laid down with a reinforced layer.
The parobayer is installed on the logs using any available fasteners.
Features of floor insulation without lag
In the absence of a lag, an additional screed is poured onto the floor surface. It will level the surface and remove all possible irregularities.
- We are laying waterproofing. Choosing affordable and economical products. We focus on reliability and ease of use. Traditional roofing felt and roofing felt, bitumen-containing roll materials are suitable.
- Fill in a layer of medium fraction expanded clay. Thermal insulation can be carried out using expanded perlite or vermiculite. A thin layer of such materials will also create good sound insulation. Vermeculite can also have a leaf form of release. Agloporite is not a very economical option. Environmentally friendly material is sawdust. They are hygroscopic, superior to expanded clay in terms of thermal insulation quality, are non-flammable and prevent decay. Processed with a special composition with an antiseptic, even at high humidity, such a filler will remain dry. Industrial slag is the cheapest thermal insulation material. There are certain requirements for the content of ash and coal in waste, for their subsequent use as a heat insulator.
- Top - additional layer roll waterproofing. Using the slats, we set the height of the insulation layer.
In a small room, it will be enough to arrange the slats only around the perimeter of the room.
Ways to insulate the floor in a wooden house with a basement
Quite a laborious process, it is most convenient to disassemble in stages.
- Crate mount
Bars of lathing 5x5 mm., Attached to the timber of the base of the floor. - Laying the sublayer boards
Small gaps are allowed. The sub-boards should not completely cover the ceiling joists. - Waterproofing laying
- Insulation sheets
- Vapor barrier
- Finish layer of final finish
This installation is suitable for houses with a basement or an underground floor, where there are no subzero temperatures.
Another scheme is the most popular:
- Draft layer
- Loose insulation or sand
- Cardboard
- Air gap (about 3 cm.)
- Finishing
Wooden logs can be fixed on posts (brick, concrete), installed directly on the foundation of the house, or embedded in the wooden basement of the house. Also directly onto the supporting beams.
We insulate a wooden floor in a house without a basement
The feature of the foundation will be important here. The method of installing the lag and the subsequent installation of the floor will depend on it. You can insulate the soil itself, or you can put the insulation in the interlag space.
In houses with a small base, where the height above the ground is low, you can lay the logs directly on the reinforced ground. The advantage of such a floor is that it will not put additional stress on the base of the house. Reinforcement is carried out using a concrete screed, on which, subsequently, a lag structure is installed. The screed is best poured in several layers. Insulation, vapor barrier is laid on the waterproofing, in the space between the logs, and you can start installing the plank floor. Roll mineral wool or expanded clay can be used as a heat insulator.
In the version with a large basement distance, the joists are laid in such a way that there is an opportunity for air circulation. This creates a ventilated space that prevents dampness in the house.
Variety of modern insulation
Fiber insulation
Fiberglass and mineral wool are excellent heat insulators, good sound insulators. Laying the fiber between the laths is very tight. The space between the slats should be made smaller than the width of the roll of material. The disadvantages of the material include low vapor permeability and low mechanical strength. Also, glass wool fibers are subject to shrinkage, and it is unsafe to work with it. Mineral wool is safe, does not shrink, but outperforms fiberglass. Mineral wool is laid with the marking upwards, that is, the denser side. In this case, vapor barrier is not required.
Organic insulation
Linen or jute fiber, very similar in properties to mineral wool. The fibers are easy to work with and safe. They are afraid of moisture getting to the surface, as the decay process may begin.
Polyurethane foam
Can be used as a finishing touch. It is applied by spraying. High enough price, adequate quality indicators... Such a coating will have low thermal conductivity, low water absorption, and environmental friendliness. Stability in its structure and shape, durability. Quality material must be dry and free from harmful volatile impurities.
With foam
Polyfoam is a dense material that reflects infrared rays well. Environmentally friendly and inexpensive. The only drawback is the instability to environmental influences. In enclosed spaces, the foam does not wear out and does not lose its qualities.
Bulk insulation
Easy to install. On the bulk insulation, you can make a flooring finish. Not very economical in terms of cost.
Foam concrete and aerated concrete, granular concrete
Remains after construction can be used as insulation. These types are highly resistant to heat retention. Granuloben is affordable and has high qualities of a heat insulator. Its composition is sand, cement and pieces of foam.
The latest insulation
The range of heat-insulating materials is expanding more and more.
Traditional materials give way to the latest advances. Physico- specifications become more and more perfect. The names of species, brands and types are enormous.
Penofol
Foiled reflective foam layer and low thickness, gives results that are many times superior to conventional materials. Layed in one layer, it does an excellent job not only with the heat preservation function, but also with waterproofing. It can serve as a vapor barrier. Long service life, ideal for use in a wooden house.
The novelty Penofol-2000 has protection on both sides in the form of aluminum foil. The efficiency of the material is much higher than that of its predecessors.
Izolon
The use of materials of a new generation with a uniform cellular structure will give the entire structure even greater strength and elasticity. Foamed material with a cellular structure. A thin layer of such material is an unsurpassed heat insulator. Economical in price, elementary in its use and operation. Combines with any other materials, great for use in wooden houses. Eco-friendly.
For insulation with a thin layer, you can use extruded polystyrene foam, which also has a foamed cellular structure, it will good choice... Plates made of expanded polystyrene - penoplex, will also be a good heat insulator. The material is laid on the leveled base of the floor, attached to it with plastic anchors. After installing such a heater, you should immediately proceed with the installation of the main floor covering.
Materials and methods for finishing the floor
For the final, final finish of the floor, there is a large selection of different floor coverings... , laminate, parquet board and solid wood boards. In cases where it is necessary to emphasize the beauty of a wooden floor, it is advisable to use varnish. Also pay attention to the oiling and waxing method. Such processing will protect the wood from the appearance of fungus, mold, insects and will give an excellent appearance. When choosing a finishing material, you should pay attention to such material characteristics as:
- Wear resistance
- Good acoustic properties
- Ease and practicality in cleaning
- Compliance with the style and interior of the house
From the right choice the materials and method of insulation, as well as the quality of the work carried out, depends on the warmth and comfort of your home.
Usually these articles are also viewed.
Warming of interfloor ceilings, like this is a process that is necessary to improve their thermal insulation and sound insulation properties. This is especially true for floors that are arranged on wooden beams.
Such structures are often found both in relatively old houses and in new buildings. Their peculiarity is in a very simple installation scheme, but at the output we get only an overlap of boards and beams. It is not able to qualitatively divide the space inside the house.
That is why they devote so much time to warming the interfloor overlap on wooden beams.
1 Features and purpose
Overlapping on wooden beams is most often installed in wooden houses. However, this is not a rule that cannot be deviated from. Such overlaps are common in other buildings of this type.
They do not use them only in monolithic buildings, frame houses and other buildings that were erected using serious technology.
And all because floors on wooden beams can be installed using a very simple procedure. Basically, all you need to do is rent a light duty crane (almost any model of a truck crane with a boom will do) and a few assistants.
The whole work consists in the installation of wooden beams with a certain pitch and in a certain direction. The beams are easy to assemble, they can also be processed without much difficulty. And to create a covering on them, it is enough to simply lay boards of the required size over the beams.
Compared to the construction of a private house from reinforced concrete blocks, the difference is obvious. The work does not require the use of powerful equipment, a large number of equipment, etc.
It is not surprising that timber-type floors have become so popular in the field of private construction, especially when we are talking about light summer buildings.
The problem is that the overlap on the beams does not have sufficient density. It's simple basic structure (the beams themselves act as the load-bearing element here), onto which a boardwalk was stuffed on one or both sides. As you yourself understand, this structure performs only a protective function.
You will have to do the insulation and sound insulation yourself. And without fail.
It is necessary to insulate the cavity between the beams. As a rule, they are hammered with boards from above and below. As a last resort, the flooring is only on top. But of great importance it doesn't attach.
In any case, such an overlap will not retain heat, or damp noise from people passing through it. If you ever heard the second floor wooden house neighbors creak, then you should know that they are probably walking along the usual beams of the interfloor type.
Insulation is carried out using special materials. You can use different technologies. For interfloor floors, the thickness of the insulation does not play such a big role.
In most cases, this is due to the fact that, as a rule, about the same temperature is kept on different floors of the house. But there are all sorts of cases. And every builder will tell you that insulation will definitely not hurt.
High-quality thermal insulation of structures always has a positive effect on the comfort inside the house. Especially those samples of structures that do not differ in special thermal insulation properties.
1.1 Types of insulation for floors on wooden beams
Insulation for beams in the thermal insulation of floors in a private house has a huge impact. So, properly selected material will help you perform high-quality insulation in the house, and save a significant amount of money. Serious mistakes will also affect both the quality of the result and the cost of money.
Now on the market there are a huge number of different ones with the help of which insulation of floors in a private house is performed.
Most often used:
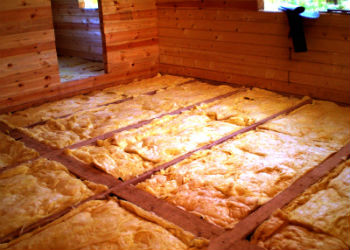
There is no need to talk a lot about mineral wool. After all, this is one of the most popular models of insulation for this moment... Mineral wool does not burn in a fire (and this is a very important indicator, because we are dealing with wooden beams) provides excellent protection against heat loss and sound insulation.
Moreover, in terms of sound insulation, it can be considered the most successful material. No other insulation can dampen noise so well.
But cotton wool also has several disadvantages. First, it swells quickly upon contact with water. For the insulation of interfloor floors, this parameter does not always matter, since in our houses, as a rule, it is dry and comfortable. But if you are going to insulate the attic, then you will have to think about it.
The second point is that insulation with cotton wool can cost you a pretty penny. This process will almost certainly be the most expensive. In terms of cost, only work with penoizol can compete with it, but there it is necessary to take into account the need to attract specialists with specialties to work. equipment.
Polyfoam is also used in our area, and quite often. In terms of thermal conductivity, it is not inferior to mineral wool, but it dampens noise by an order of magnitude worse.
There are differences in the disadvantages of this insulation. On the one hand, it does not react at all to moisture, does not absorb water and can be operated normally, even if you have planned the insulation of the bathroom. On the other hand, the foam is vulnerable to fire and high temperatures.
If something goes wrong in a wooden house, then an overlap with foam insulation can significantly complicate the task of fire extinguishing. Or even cause a fire. Such situations are extremely rare, but they do happen, and they must be noted in advance.
Extruded polystyrene foam is the same foam that has just passed the extrusion process. After remelting under pressure and with high outlet temperatures, a denser material is obtained. It is much stronger, withstands serious loads and exceeds all the above-mentioned models in terms of thermal insulation.
The problem of expanded polystyrene, like some others of this type, is in its price and inability to dampen noise.
Penoizol is a spray insulation made of artificial foam that is mixed with carbon dioxide. The output is a foamy material that is easy to apply and adhere to the surface. After spraying, penoizol swells in the same way as with polyurethane foam.
The result is a very dense material with excellent thermal insulation properties and good structure.
Unlike other heaters, the floor box from the beams can be filled with penoizol completely, without worrying about the inconsistency of the shapes and preliminary preparation.
The foam will simply clog all the cracks and areas, thereby forming a high-quality filling of the voids.
Expanded clay, wood chips, etc. are often used as a backfill heat insulator. In a modern private house, such methods are rarely used. This insulation is quite heavy, free-flowing, it may even have a specific smell (although it can be easily removed).
Although if we talk about the private construction of summer cottages or other similar buildings, then the use of backfill insulation can be justified. After all, their entire installation does not consist in installing waterproofing, and then filling in insulation, and it is extremely cheap.
2 Technology of floor insulation
Now let's turn directly to the technology of floor insulation. In fact, there is nothing difficult here. Moreover, the presence of beams and bases already simplifies the work.
Indeed, in most cases, you will not have to mount an additional frame or something like that. It will be quite simple to fill the cavity between the beams with insulation and layers of insulation, and then fill it with boards.
Stages of work when insulating the interfloor overlap from the floor:
- We prepare the floor, if necessary, we open the boardwalk.
- We prepare insulation and all the necessary materials.
- We lay a layer of vapor barrier. You can work with Izospan or any other suitable vapor barrier film.
- We install insulation.
- We lay a layer of waterproofing, if necessary.
- We hammer the cavity with boards.
- We lay the topcoat.
If you need to insulate from the side of the ceiling, then here the technology is almost identical. Only waterproofing you most likely will not need at all. And if necessary, then it will be mounted first under the cover.
Then a layer of insulation will go, which is attached with dowels to the bases of the beams, and then a vapor barrier film.
There is no great need for a vapor barrier film to work with insulation based on expanded polystyrene. Here it is already necessary to assess the overall situation.
2.1 Installation of insulation in the interfloor overlap (video)
The widespread introduction of energy-saving technologies also affected private construction. At the dacha or in a country house, heat can go through walls, windows, doors, floor, roof. With constant use of the attic or attic, it is imperative to insulate the interfloor overlap.
As a rule, interfloor ceilings made of wood are warm in themselves, since wood serves as a good thermal insulator, however, any insulation depends on both the structure and the thickness of the material, which is why sometimes additional insulation work is necessary.
Even during the construction of the building, all floors are necessarily insulated. This will help to further reduce the cost of heating during the operation of the building, which will please with comfortable living conditions. Beams are also properly insulated - for this, the sequence of work is observed and the appropriate material is selected.
Choosing a material
For insulation of interfloor floors on wooden beams, it is advisable to use extruded polystyrene foam, polystyrene foam, foamed polyethylene foam, mineral wool and bulk materials.
Extruded polystyrene foam
This type of material, also called styrex, penoplex, techno-nicol and technoplex, is used for different types thermal insulation and perfectly insulates wooden floors. It is considered the best thermal insulation material that you can install yourself. Its advantage is that the high density of the panels allows plastering or puttying directly on them. It is environmentally friendly.
It is made in the form of plates, to which a cement-bonded layer is additionally glued. The material retains its properties even in the event of periodic freezing and thawing.
The material is appreciated for:
- light weight;
- zero water absorption;
- low thermal conductivity;
- high mechanical strength.
Another effective material used for insulating floors in a wooden house is polystyrene foam. In structure, appearance and functions, it is similar to extruded polystyrene foam, although it has a lower density. Available in sheets with a thickness of twenty millimeters. The foam can be easily cut with a knife.
This material is distinguished by:
- low cost;
- low thermal conductivity;
- ease of installation work;
- antimicrobial properties;
- resistance to temperature fluctuations;
- waterproofness.
It does not burn, so it is often used in the construction of private houses with stove heating. The choice of slab thickness depends on the design features of the building and the climatic zone.
Foil polyethylene foam
Foamed polyethylene foam is a gas-filled polyethylene, in which one side is covered with aluminum foil. The material is produced in rolls. It has a small thickness, but this does not prevent it from effectively insulating wooden interfloor floors, largely due to the properties of foil. When hitting such a heater, heat fluxes do not lose their energy, but, being reflected, return back to the room.
Mineral wool
Under the general concept of mineral wool, there are several types of materials at once - glass wool, slag wool and stone wool, obtained from glass, blast furnace slag and basalt. Insulation is produced in rolls, and its use in a wooden house for insulating interfloor floors is convenient and practical. You can choose the foil option, which will create an additional effect of thermal insulation.
Vata is different:
- environmental friendliness;
- hygiene;
- low thermal conductivity;
- high level of fire safety;
- good noise absorption;
- resistant to bacteria, fungi and insects.
When working with cotton wool, you must take into account its sensitivity to moisture. The insulation is laid on a vapor barrier material. If you do not follow the technology, it will reduce the heat-insulating properties of mineral wool.
Important! When installing mineral wool, carcinogenic dust appears, so it is imperative to cover the body with clothes as much as possible and use gloves, glasses and a respirator.
Bulk material
Among the bulk insulation, the most common is expanded clay. They receive it in special ovens, acting high temperature on natural shale clay. The clay, due to continuous rotation, foams and takes on a hard, hardened surface.
Thanks to this, expanded clay receives the following properties:
- light weight;
- high sound insulation;
- fire safety;
- high thermal insulation;
- environmental safety;
- resistance to decomposition and decay.
When using expanded clay between floors, some features must be taken into account. Since the material contains a large amount of crumbs and dust, it is poured onto the substrate. The thickness of the layer is about ten to twenty centimeters. To prevent expanded clay from getting wet and not drying for a long time, a waterproofing layer should be created.
Expanded clay is sold in the form of sand, crushed stone and gravel, but only gravel is used between the beams.
Instead of expanded clay, you can use sawdust. They are chosen because they are natural, lightweight, affordable and free of toxic impurities. However, the material is highly flammable, so it is not often used.
Works on insulation of floors
For arranging multi-storey floors in a house, the most popular material is wood. Beams made of wood are affordable, allow less heat to pass than concrete, and are easy to install. The work on the thermal insulation of the floor is carried out in a certain sequence.
First, do everything preparatory work... During preparation, the elements are carefully inspected and checked for a bark beetle, fungus and other problems. If there are gaps or black marks, then the affected area is treated with a special agent. In older houses, beams may need to be reinforced before the wood floor is insulated.
Then perform waterproofing works... It is better to use a super diffusion membrane rather than a waterproofing membrane. Such a membrane will retain water, but let steam through. Waterproofing material cover the entire protected surface. Particular attention is paid to beams that wrap waterproofing film... In order for the wood to dry naturally, it is necessary to leave ten millimeters free from each edge. It is recommended to prime the beams with a primer or any other suitable mortar.
After that, the selected insulation is fixed. At the end of the installation of the insulation, the ceiling is finished.
Insulation with foam
When using foam plastic for warming interfloor floors, work is performed in the following sequence:
- the insulation is cut to size, reducing it by one centimeter to fix it. You can also cut it exactly to size, and then fix the sheet with special glue foam, glue or umbrella dowels;
- with the help of wooden pegs, which are hammered between the foam and the beam, the insulation is fixed;
- the places where floors and beams are connected and joined are blown out with polyurethane foam;
- when the polyurethane foam dries up, the excess is cut off;
- after that, if the ceiling is putty, a polymer film is attached.
Thermal insulation with mineral wool
When using mineral wool for insulating a wooden interfloor floor, the work is performed in the following sequence:
- the distance between the beams is measured;
- insulation is cut in accordance with the dimensions;
- cotton wool is placed in the space between the beams. In cases where the height of the beam is greater than the height of the insulation, the cotton wool is laid in two layers;
- with the help of a wire, the insulation is fixed to the ceiling;
- then a layer of membrane is laid.
For the final finishing of the resulting ceiling, it is recommended to use suspended ceilings, wooden lining or drywall.
Floor insulation
It is much easier to carry out the process of warming wooden beams on the floor. In this case, it is advisable to use polystyrene foam, polystyrene foam, mineral wool, bulk materials as insulation material.
The sequence of work will be as follows:
- the floor is leveled;
- a vapor barrier film is spread overlapping (if a rigid or loose insulation is used, then the film is not needed);
- insulation is laid;
- the hydro-barrier is laid;
- after that, a rough floor is laid from OSB, plywood, natural boards or a concrete screed is made.
Insulation of various types of floors
The sequence of work is influenced by the type of material of the ceiling, the type of insulation and the place where the insulation works.
If these are concrete floors, then it is better to perform their thermal insulation using rigid materials, fixing them with special dowels or glue. If used soft materials, then a galvanized profile is mounted or wooden slats are stuffed.
Thermal insulation of the ceiling is performed from the attic and from the living quarters. If the work is carried out from the side of the attic, then it is possible to use any heat-insulating materials, even bulk ones. In the case of insulation from the side of living rooms, cotton wool or slabs are used.
When insulating the attic floor, any thermal insulation materials are used. If the attic space is planned to be exploited, then a rough floor must be made. The condition of the gables and rafters should be checked, and the roof should be insulated.
General characteristics of thermal insulation materials
Eco-materials for thermal insulation of wooden interfloor floors are constantly being improved and the latest scientific achievements are involved in their development. When choosing a material, you should focus on its technical characteristics. It is necessary that it meet the following parameters:
- light weight;
- low thermal conductivity;
- toxic safety;
- moisture-repellent qualities;
- vapor permeability and air permeability;
- sufficient fire resistance and fire resistance;
- moderate density;
- sorption moisture;
- compressive strength and crease;
- resistance to damage by putrefactive bacteria and fungus;
- resistance to overheating;
- frost resistance.
The heat saving efficiency of the material is up to 35 percent. With ineffective interfloor insulation, payment for heating can turn into high costs. With high-quality insulation, the temperature drop will be less felt, the conditions for the appearance of condensation will not arise and the room will receive additional protection from fungus and mold.
In aggregate, most of the indicators correspond to expanded polystyrene, penoizol, glass wool, mineral wool, polyurethane foam. Each material has its own advantages and differs in some parameters. Styrofoam and its various derivatives are good for thermal insulation, but if they tan, they will begin to release toxic substances. Extruded polystyrene foam and natural bulk materials are also great, but will become unusable if mice appear in the attic. With a weak foundation, especially on floating ground, it is better not to use expanded clay, since it makes the overall structure heavier.
Parameters of high-quality insulation of interfloor floors
With high-quality thermal insulation, the temperature range at different times of the year will differ significantly from external fluctuations, and correspond to the optimal microclimate inside the house.
Minimum humidity in enclosed spaces and minimum amount of condensation indicate compliance with thermal insulation technologies. But even in this case, the room still needs to be ventilated.
The thermal insulation of the ceilings along the beams protects the room in the event of very low temperatures in winter, and also protects against the choking summer heat. Thanks to this, you can save on air conditioning.
When correct waterproofing and vapor barrier, the operating time of roofing structures increases, corrosion affects metal parts less, and fungus and mold do not appear on wooden beams.
Thanks to the correct arrangement of attic windows and ventilation openings in the attic, humidity is reduced and strong drafts do not occur. In addition, by providing the attic with high-quality thermal insulation from the outside, a minimum amount of ice and icicles will form on the roof.
In modern construction of country and private houses, it is imperative to insulate the structure of the roof, attic or attic, since up to a quarter of the heat goes through the roof during the heating season. By performing high-quality insulation on the beams, you can significantly save heat during the operation of the house in winter. During installation attic space and the roofs must be insulated with wooden beams. To do this, they use various insulation materials, each with its own pros and cons, which is chosen, focusing on the price and technical characteristics of the room.