Erect reliable roof above the house is an extremely important and large-scale event. However, it would be a mistake to believe that, having laid a high-quality, leak-proof roof, one can “rest on our laurels”, considering the matter completed. A good owner will definitely think about the issues of roof insulation, regardless of whether it is planned to use the attic as a useful room.
Thermal insulation of roof slopes is a specific matter, the features of which are predetermined by the very design of this architectural element of the building. Nevertheless, most of the modern insulation materials are quite suitable for this, and the specifics of the work are more related to the technology of their installation. So, the topic of today's consideration is insulation for the roof: which one to choose, which one is better for conducting self-thermal insulation, which one will be the safest, most practical, durable in operation.
For those homeowners who plan to use the attic space as a full-fledged living room, or even just a warm storage room, the question should not even be raised. None of the roof coatings are able to create an effective thermal barrier that would provide a comfortable temperature level. Moreover, not only protection from winter cold is important. A large area of \u200b\u200bthe roof, exposed to the sun's rays, "catches" a huge amount of heat radiation in the summer, and unbearably hot conditions can be created in the attic. So the word "insulation" should be considered in a broader sense - the term "thermal insulation" is more suitable.
And if the attic is not planned to be used - is it worth then to insulate the roof slopes? Business, of course, is the master's, and many prefer to do without this stage of construction. Nevertheless, such a measure, although it causes certain additional costs, seems reasonable.
- First, it is worth considering the energy efficiency of the building as a whole. It is no secret that the structure of the roof and roof accounts for up to a third of all heat losses at home. In part, this problem is solved by the reinforced thermal insulation of the attic floor. But if we add to this the insulation of the roof slopes, then the maximum energy efficiency mode is achieved, which ultimately leads to the effect of significant savings on energy consumption.
- Secondly, with the proper implementation of insulation and the accompanying hydro and vapor barrier " roofing cake», The structural elements of the rafter system will be significantly less exposed to external influences - temperature, humidity and biological. And this, of course, will significantly increase the durability of this site, and the entire building as a whole.
- Thirdly, almost any thermal insulation material has properties to absorb the propagation of sound vibrations. Thus, the insulation of the roof slopes also gives a good soundproofing effect, which is especially important for “noisy” materials such as corrugated board, slate, roofing iron or metal tiles.
- And finally, fourthly, a good owner should always think "strategically", that is, for the future. Who knows, it is quite possible that in a couple of years there will be a need for additional space, and the previously insulated attic, without traces of freezing and exposure to dampness, will only have to be “refined” and brought to the required degree of comfort. It will be extremely difficult to remodel a “cold” attic space that has repeatedly experienced seasonal fluctuations in temperature and humidity into a comfortable room. And sometimes for this you even have to dismantle the roofing and make changes to rafter system with a crate to fulfill all the necessary conditions for the insulation of the "roofing pie".
Isn't it better to tackle this issue right away?
What are the requirements for a high-quality roof insulation?
In order for the insulation of roof slopes to be effective, durable and safe, thermal insulation materials used for such purposes must meet a number of requirements.
- First of all, of course, the thermal insulation capacity of the material is considered, that is, its resistance to heat transfer. In order for the roof insulation to be effective, it is advisable to use materials whose thermal conductivity does not go beyond the upper limit of 0.050 W / m × C °
- For the roof truss structure, unnecessary, unnecessary weight loads are not at all needed. This means that the material should have a low specific density.
- Insulation should be "indifferent" to temperature extremes in a fairly wide operating range - from extreme winter frosts to strong heating of the roof under the influence of sunlight.
- The quality of the insulation is very important is its low hygroscopicity, that is, the property of minimally absorbing moisture. Overmoistening of the material leads to a sharp loss of thermal insulation qualities, since water is a very heat-absorbing substance. In addition, moisture-laden material becomes significantly heavier.
- Insulation material should not be biodegradable, not serve as a breeding ground for microflora, not become a comfortable place for nests of insects, rodents, birds.
- Ideally, the insulation material should be absolutely non-flammable, or, in any case, be as safe as possible from a fire point of view.
- An important requirement is the environmental safety of the material, so that it does not pose a danger to the health of the residents of the house and does not pollute the environment.
- No one wants to insulate the roof too often, so one of the criteria for choosing a high-quality thermal insulation material is always its durability.
- And, finally, the thermal insulation material should be affordable at its cost and convenient for carrying out insulation work, including on its own, without the involvement of specialists.
Unfortunately, it cannot be said about any material that it fully meets all the listed requirements and is ideal for roof insulation. So you have to choose from the available ones, carefully assessing their advantages and disadvantages.
Compare different roof insulation
Is it convenient to use bulk insulation?
Since we are talking about the insulation of the roof slopes from the inside, we will "take out of the brackets" bulk thermal insulation materials, such as expanded clay, perlite, vermiculite. It is convenient for them to insulate the attic floor, that is, the horizontal plane. They are also used for thermal insulation of wall structures made on the principle of well masonry. There are technologies for their use on pitched roofs with a relatively small slope angle, however, this approach is not particularly widespread due to the rather complex construction of the "roofing pie". In addition, the same expanded clay is significantly inferior to other insulation materials in terms of its thermal insulation characteristics, which means that a thick layer of it will have to be provided, which on a pitched roof is quite problematic.
Vermiculite, in terms of its thermal conductivity, is closer to modern insulation materials, but its cost is very high, and its use in this case is unlikely to be justified.
Immediately, we note that there are supporters of using and assistants natural materials... For example, for a long time, dry foliage, needles, sawdust, etc. have been used to insulate the floors of houses. Again, what is good for horizontal surfaces is not quite suitable for pitched roofs.
As a result, the finished foam is a kind of conglomerate of "glued" balls. The share of air in the structure of the foam is over 90%, which, in principle, predetermines its high thermal insulation qualities.
The production of polystyrene does not require excessive costs, therefore, the material can be attributed to the most affordable of all other heaters.
It would seem - what more could you want? The material provides good thermal insulation, is lightweight, inexpensive, very easy to process, produced in blocks of verified "geometry", that is, it will not be difficult to work with it. However, not everything is as wonderful as it might seem at first glance.
- Let's start with thermal insulation qualities. They are really quite good - the thermal conductivity is usually around 0.038 W / m × C °. But it should be understood correctly that this value will only be valid for ideal operating conditions. The trouble is that although the foam is not considered a particularly hygroscopic material, the input does not penetrate into the balls, it absorbs moisture, and in a sufficiently large amount, there may be gaps between them. It happens that low quality foam is absorbed by moisture, which is almost three times its mass! Naturally, in this situation, the thermal insulation characteristics of the material are sharply reduced.
- The second worrying point is a direct consequence of the first. Moisture that has penetrated into the material during temperature extremes can cause cracks or even coloring of the foam. In addition, the studies carried out have shown that this material can in no way be attributed to the category of particularly durable - the mentioned "water corrosion" of the foam leads to the formation of soft cavities, through "cold bridges" through cracks, and as a result, cases were recorded when such important insulating qualities are already after 5 ÷ 7 years of operation, they decrease several times!
- The third important drawback is the "innate" chemical instability of polystyrene. The fact is that it belongs to the group of equilibrium polymers, that is, under certain conditions, the process of depolymerization can start - decomposition into components. Not only does the foam become loose at the same time, it falls apart into separate balls - this is accompanied by the release of free styrene into the air - a toxic chemical compound extremely dangerous for humans that can cause or activate various diseases.
The process of decomposition is the more active, the higher the temperature and humidity of the material. And in the under-roof space in the summer there will be more than enough of both!
- Perhaps the most important disadvantage of foam is its flammability. No matter how the manufacturers describe the safety of the material, almost all polystyrene foam of this type belongs to the G4 group, the lowest. Moreover, when ignited, the foam melts and is able to become a "liquid flame" spread. And the worst thing is that during thermal oxidation in very large volumes, extremely toxic products are released that can cause almost instantaneous poisoning or chemical burns of the respiratory system. Unfortunately, the statistics of tragedies during fires suggests that people trapped in the polystyrene burning zone have minimal chances of survival.
- And, finally, purely "everyday" considerations. The fact is that the simplicity of foam production has become the reason that it is produced everywhere, often in semi-artisanal conditions. Naturally, in pursuit of a quick profit, the owners of these "factories" often violate the established technology, ignore some mandatory stages (drying, ripening, etc.), and as a result, the output material does not correspond not only to GOST standards, but even more " liberal "TU. As a result - increased fragility, chemical instability, uneven density, persistent unpleasant odor, etc. Moreover, these shortcomings may be subtle at first, but very quickly manifest themselves later, already during operation.
By the way, in many countries, such expanded polystyrene is legally prohibited for use in residential construction. For the above reasons, they completely abandoned it in the production of cars, buses, railway cars, switching to the use of much safer polyurethane foam. And you probably need to be an extremely "risky" owner of the house in order to use it for roof insulation. There are many other, much more effective and safer options.
Extruded polystyrene foam
The production technology of this material is radically different. A melt is prepared from granular raw materials, to which special additives are added, which increase the chemical stability of the polymer and give it greater resistance to fire. Special additives provide foaming of the melt, and in this state it is forced through the molding nozzles of the extrusion line. When solidified, a structure is obtained with completely buried type gas-filled cells isolated from each other, and without any gaps between them, where moisture can penetrate. Thus, the hygroscopicity of the material tends to zero.
The material is obtained with a high gas saturation, a pronounced uniform density throughout its thickness, and the strength properties are much superior to those of foam plastic. The characteristics of resistance to heat transfer also look better. The blocks have clear geometric dimensions, and most types of high-quality extruded polystyrene foam are also equipped with lamellas for seamless connection in one plane.
The introduction of special additives into the composition of extruded polystyrene foam significantly increases the fire safety of the material. Many types are assigned the G1 category, that is, the polymer practically does not ignite even when exposed to an open fire, quickly self-extinguishes and does not spread the flame. Nevertheless, in the event of a fire during the thermal decomposition of such expanded polystyrene, toxic substances will be released to no less extent than foam, and this should be borne in mind.
The advantage of extruded polystyrene foam can also be called the fact that a rather complex technology for its manufacture significantly reduces the risk of running into semi-handicraft products. this market segment has its own "heavyweights", and one of the brands that has earned an unconditional reputation for quality is Penoplex. Plates of universal application "Penopdex-Kofmort" are perfect for roof slopes.
To compare the parameters of foam and extruded polystyrene foam, their main physical and operational characteristics are summarized in the table:
Parameters of thermal insulation materials Polyfoam (for example, PSB-S-50) Plates of extruded polystyrene foam (for example, "Penoplex-Comfort") Illustration Thermal conductivity (W / m оС) 0.039 ÷ 0.050 0.028 ÷ 0.034 Water vapor permeability (mg / m × h × Pa) - 0,017 Water absorption in 24 hours in% of volume 0.6 0.4 Ultimate bending strength MPa (kg / cm²) 0.07 ÷ 0.20 0.4 ÷ 0.7 Compressive strength 10% linear deformation, not less than MPa (kgf / cm²) 0.15 ÷ 0.2 (1.5 ÷ 2) 0.25 ÷ 0.3 (2.5 ÷ 3) Density (kg / m³) 35 ÷ 50 28 ÷ 35 Working temperatures -50 to +75 Fire resistance category G4 (combustible) G1 (non-flammable,
self-extinguishing)Standard panel sizes, mm: - lenght and width 1000 × 1000 600 × 1200 - thickness from 20 to 200 20; 30; 40; 50; 60; 80; 100 Glare of any expanded polystyrene is easily cut, and when insulating the roof, they are adjusted to the distance between the rafters. However, at the same time, due to the lack of proper plasticity and elasticity of the material, it is impossible to do without cracks and gaps, and they will have to be filled with polyurethane foam.
To get rid of cold bridges, they often resort to two-layer insulation, and the second layer turns out to be completely solid - the rigidity of extruded polystyrene foam allows you to do without lathing.
The reverse approach is also practiced - continuous insulation is performed from the outside, thus turning into a kind of continuous crate. Since extruded polystyrene foam has extremely low hygroscopicity and vapor permeability, its continuous layer also becomes an effective hydro and vapor barrier.
Low vapor permeability of the material can lead to a "thermos" effect inside attic space, therefore, in order to prevent a too damp atmosphere, effective ventilation of both the attic itself and the under-roof space must be thought out.
- If you plan to insulate the roof slopes with expanded polystyrene, then the choice should still be made in favor of extruded, despite the fact that this option will be more expensive.
- Do not forget that any expanded polystyrene in the event of a fire can pose a mortal threat to people.
- Due to the chemical characteristics of the material, it is not worthwhile to practice insulation with its help if there is living room - Emission of toxic styrene is not excluded under the influence of elevated temperature from roof slopes heated in the sun.
- If there is an opportunity to use another, safer material, you should use it, since the disadvantages of polystyrene for insulating the roof still exceed its advantages.
Mineral wool
Mineral wool heaters are very popular in thermal insulation work. They all have a common feature - they are a thick layer of densely intertwined thin fibers that are drawn from the melt of tog or other mineral component. This weave creates a layer of immobilized air, which becomes an excellent barrier to heat transfer.
Depending on the fiber material, all mineral wool can be divided into three groups - slag, fiberglass and basalt.
Slag
For the manufacture of heaters of this type, wastes of metallurgical production are used - blast furnace slags are melted in furnaces, and fibers are formed from them, which are then pressed into mats using a binder. The material often turns out to be somewhat heterogeneous, therefore slag mats are usually additionally quilted with cords.
The slag has few advantages, and only the low cost of the material can be called significant. But there are so many shortcomings that it is better to immediately abandon the use of such insulation during the construction of a residential building.
- The initial characteristics of thermal and noise insulation seem to be quite good, but they are quickly lost due to a banal reason - slag wool is extremely hygroscopic, and can literally be saturated with moisture from their air.
- The chemical composition of raw materials is extremely heterogeneous, therefore, slag wool can have a large percentage of residual acidity, which leads to corrosion of metal structural elements in contact with it.
- Slag wool is afraid of even small vibrations - its fibers are extremely brittle, and the material quickly shrinks, decreases in volume, cakes, losing all its insulating qualities.
- The fragility and brittleness of the fibers make this type of mineral wool extremely inconvenient to work - special measures are required to protect the skin, eyes and respiratory tract, and still there is a possibility of irritation of the integument.
In a word, it is better not to consider slag wool at all as a probable insulation for the roof.
Glass wool
In this case, the material for the formation of thin fibers is a melt of refined quartz sand or glass waste (glass breakage). A “carpet” is formed from the fibers using binding additives, which, after pressing, is cut into mats or blocks of the desired size.
As a rule, glass wool stands out against the background of other heaters with a characteristic yellowish tint.
Glass wool has become extremely widespread due to its low price and good performance.
- It is very plastic, that is, it shrinks to smaller volumes during packaging, straightening before installation, which is convenient for transporting material.
- It has a low density and, therefore, weight, and will not weigh down the roof truss structure.
- The elasticity of the blocks and mats makes it easy to install them between the rafters placed at a certain pitch.
- At the same time, the flexibility of blocks or mats allows the use of glass wool for thermal insulation of complex, curved or broken surfaces, which is sometimes encountered in the construction of original roofs.
Nevertheless, a number of disadvantages are inherent in it.
- The hygroscopicity of the material is quite high, and, absorbing moisture, glass wool significantly loses its thermal insulation qualities. When using this insulation, reliable vapor and waterproofing is necessarily provided, conditions are created for the free evaporation of water vapor in order to prevent the formation of condensation.
- Glass is an amorphous material, therefore, the processes of gradual sintering of fibers and an increase in the density of glass wool are inevitable. They are not as pronounced as in the slag, but still they should not be discounted.
- Fiberglass is quite brittle, and it is necessary to work with such insulation using protective equipment. In addition, it is necessary to provide a barrier so that the smallest particles of fibers do not penetrate into living quarters - they can cause allergic reactions or exacerbations of respiratory diseases.
- It will not be possible to completely eliminate the emission of binders, which include formaldehyde resins. With this in mind, you should only purchase reliable material famous brands, whose manufacturers carefully control the quality of their products.
For example, the Ursa company managed to completely or partially get rid of many significant disadvantages inherent in glass wool. The wide range of products is designed for a wide variety of construction areas. But some materials are intended specifically for private housing construction. Insulation blocks and mats "URSA GEO" are especially appreciated. One of the types of insulation even has an eloquent name - “URSA GEO A private house”, And is suitable for almost any area requiring thermal insulation.
They are distinguished by their durability - the manufacturer is not afraid to guarantee a service life of 50 years or more. The material is not subject to shrinkage, chemical or biological degradation, and formaldehyde emissions are kept to such a minimum that there are no obstacles to the use of these insulation boards in living quarters.
The name of this high quality insulation is “URSA GEO Pitched roof", Speaks for itself
Especially for the insulation of the roof slopes between the rafters, a separate type is produced - URSA GEO Pitched roof, in the production of which the URSA Spannfilz technology is used, which literally means "elastic felt". The mats are perfectly compressed, set between the rafter legs, and, when straightened, provide excellent fixation that does not even require additional measures keeping them in place. Naturally, the snug fit also eliminates the "cold bridges".
The table below shows the main indicators of URSA GEO fiberglass insulation, any of which is suitable for insulating a pitched roof
"M-11" "Private
house""Light" "Pitched
roof""Universal
slabs ""Frame" Thermal conductivity coefficient, W / m × ° С λ10 0,040 0,041 0,044 0,035 0,036 0,035 λ25 0,044 0,044 0,047 0,038 0,039 0,038 λА 0,044 0,045 0,049 0,040 0,041 0,040 λВ 0,046 0,047 0,052 0,042 0,044 0,042 Water vapor permeability, mg / m × h × Pa 0,64 0,65 0,7 0,64 0,51 0,54 Fire safety class KM0 KM0 KM0 KM0 KM0 KM0 Flammability group NG NG NG NG NG NG Operating temperature range, ° С 60 ÷ + 270 60 ÷ + 220 60 ÷ + 220 60 ÷ + 220 60 ÷ + 220 60 ÷ + 220 Water absorption in 24 hours, kg / m2, no more 1 1 1,2 1 1 1 Dimensional parameters, mm - length 7000
9000
100008350 7000 3900
30001000
12504500
3900
3000- width 1200 1200 1200 1200 600 1200 - thickness 50
10050 50 150
20050
100100
150
200Video: heaters brand "URSA"
Basalt mineral wool
Basalt wool is rightly considered the highest quality insulation of this kind. It is made from molten rock, and its fibers are particularly resilient and strong. They are not characterized by fragility, which is noted in glass wool, so installation is much easier.
Basalt wool slabs usually have a uniform density, even outwardly resemble natural felt. The special processing of the material makes it almost hydrophobic - water droplets roll down the basalt wool without penetrating deep into the structure. At the same time, the material has excellent vapor permeability, which contributes to maintaining the optimal moisture balance in the insulation, and with the correct organization of vapor and waterproofing, water vapor will have a free exit into the atmosphere.
Plates have a clear geometry, are easy to cut into the desired size if necessary, and it is a pleasure to work with such material. Some types of basalt insulation, in particular, ROCKWOOL LIGHT BATTS slabs, have an interesting structure - one side is made springy, using flexi technology, that is, reliable installation of slabs between the rafters is simplified to the limit.
As already noted, basalt wool practically does not irritate the skin.
Leading manufacturers have tried to minimize the emission of formaldehyde, and many types of basalt wool are approved for use even in children's and medical institutions, that is, they can be safely used to insulate residential attic spaces.
The disadvantages of the material include a higher price - but it's worth it.
Of course, the choice of basalt insulation will be optimal solution... True, all the advantages will be true if a really high-quality material is acquired. Thus, the brands ROCKWOOL, Technonikol, Izovol, Basvul, PAROC, Isobel and some others deserve complete trust.
For example, the table shows the parameters of the universal basalt insulation boards "ROCKWOOL LIGHT BATTS"
Material performance parameters Indicators Thermal conductivity coefficient (W / m × ° С): - calculated at t \u003d 10 ° С 0,036 - calculated at t \u003d 25 ° С 0,037 - operational under conditions "A" 0,039 - operational under conditions "B" 0,041 Flammability group NG Fire safety class KM0 Water vapor permeability (mg / (m × h × Pa), not less 0.03 Partial immersion moisture absorption no more than 1kg / m² Dimensions 1000 × 600 mm thickness 50 or 100 mm Video: Advantages of ROCKWOOL LIGHT BATTS SCANDIC insulation boards
Sprayed insulation for roof slopes
These types of insulation materials include polyurethane foam and ecowool.
Both of these materials deserve close attention, as they show excellent performance characteristics. They basically differ in their composition, but they are united by the fact that special equipment will have to be used to apply a layer of thermal insulation. But on the other hand, they are able to create a uniform, almost seamless coating on the reverse side of the roof slope, filling the smallest gaps and cavities, which minimizes the likelihood of cold bridges formation.
Features of the application of these materials, that is, the mandatory use special equipment and the presence of the accumulated experience of working with it, predetermine the not too yet great popularity of such technologies, especially among the owners who are used to doing everything with their own hands. Therefore, in this article we will not dwell on these issues in detail, especially since they have been given detailed coverage in other publications of our portal.
It will be logical to finish the publication by considering the question of what thickness of insulation is required to create an optimal microclimate in the attic.
Current SNiP, which are immutable laws in construction industry, normalized values \u200b\u200bof heat transfer resistance for building structures of residential buildings have been established, separately for all regions of Russia. In order not to give long tables, below is a schematic map, according to which it is easy to find an approximate value (with a sufficient degree of accuracy) for your place of residence.
Note that the resistance values \u200b\u200bare indicated with three different numbers - for walls, for floors and for roofs. Of course, in this case we are interested in the coatings (red numbers).
Total resistance to heat transfer building structure consists of the parameters of all layers that create a barrier to the spread of cold. But in the case of roof insulation, only the insulation itself, as well as the materials of the inner lining of the attic, can be taken into account. Roofing material, whatever it may be, does not take part in thermal insulation, since it is separated from the insulation layer by a ventilated layer. Thermal resistances of vapor and waterproofing membranes are so small that it makes no sense to take them into account.
So, if the thermal conductivity coefficient of the selected insulation is known, the parameters of the layers of the inner lining, the normalized value of the thermal resistance of the coating structure for a given region, it costs nothing to calculate the required thickness of thermal insulation.
We will not give calculation formulas here, but rather suggest using a special calculator, which already contains the basic parameters necessary for carrying out calculations.
Insulation for the floor is an essential element of the entire structure of the house. In this article, we will look at the main and most popular types of insulation, compare them specifications and styling features.
The thermal insulation of any room will be very mediocre and ineffective if the insulation is not integrated under the floor covering.
With all the variety of thermal insulation materials, let's figure out their pros and cons.
What is floor insulation for?
Thermal conductivity varies depending on the size of the granules and the raw materials used. The most optimal fraction for floor insulation is expanded clay, with a grain of 5-10 mm.
It is very convenient to use when organizing a dry screed. The work scheme is as follows:
- On the base, lags are laid and fixed;
- Expanded clay is poured between the logs;
- The structure is closed from above with two layers of gypsum fiber board or plywood.
This type of screed is very convenient for the efficiency of installation and cleanliness of work... But it has a drawback - it does not tolerate contact with water. That is, it cannot be installed in the kitchen or bathroom.
Convenience of working with expanded clay is especially clearly manifested when leveling large slopes in the room. When backfilling, it will tend to spread over the horizon itself.
Expanded clay is successfully used when creating a floor on the ground. In the floor pie scheme, it occupies an important place just between the rough screed and the rubble layer. Here it not only serves as a thermal insulator, but also cuts off the remnants of the capillary rise of groundwater.
Its use as a filler for screed construction is allowed only on a solid base, provided that grain 0-5 mm is used. But this is not the best way to insulate.
Expanded clay also has negative sides. First, it absorbs moisture well enough. And at the same time then it gives it very badly. And after being saturated with water, the thermal conductivity of expanded clay improves by 34-42%. This means that when using expanded clay as insulation, it is necessary to cover it with a layer of film.
It is caustic. In other words, he collapses upon impact... And crushed expanded clay, much worse shows all its positive qualities.
Summarizing, it can be noted that although expanded clay is a very cheap insulation, in order to give the floor the same comfort as with Penoplex thermal insulation, it is necessary to pour a layer 5 times thicker. And this is not always acceptable.
Calculate the price of your repair! Is free!
Only for residents of Moscow, the Moscow region, St. Petersburg and the Leningrad region:
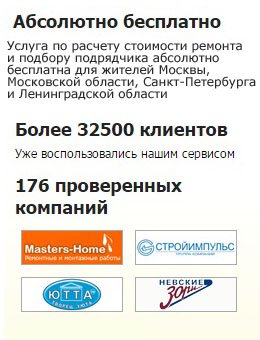
Stone wool
The surface of the insulation is covered with a fiberglass mesh and a layer of glue / plaster. After that, the base layer is primed and covered with a finishing layer of facade plaster.
These manipulations are easy to do with your own hands without unnecessary mechanisms or professional builders.
Advice! In buildings with big amount people per unit volume, or in rooms with high humidity, it is recommended to make a vapor barrier on the inside of the wall in order to avoid the accumulation of moisture in its structure during severe frosts.
Stone wool
Hard, as it has similar properties.
It is characterized by:
- Water vapor permeability - high;
basalt wool is considered as a solid insulation
Since it has similar properties.
It is characterized by:
- Form in the form of a rigid plate, which does not deform under normal operating conditions;
- Possibility of wall mounting without auxiliary structures;
- Possibility of applying plaster;
- Static indicators of thermal conductivity and structure.
Stone wool characteristics:
- Thermal conductivity - 0.039 W / m × ° С;
- Working operational density - 35 kg / m³;
- Stress on supporting structure - 5.85 kg / m²;
- Environmental friendliness - under normal conditions it does not emit harmful compounds; at elevated temperatures, the phenolic binder can release harmful chemicals;
- The recommended layer thickness is 100 mm;
- Water vapor permeability - high;
- Air permeability - high;
- Thermal stability - up to 700 ° С;
- Moisture resistance - low, requires vapor barrier;
- The service life is about 50 years.
The installation of cotton wool resembles the installation of expanded polystyrene. In the case of ventilated facades or siding, instead of plaster, cotton wool is sewn up with panels.
Important! Unlike foam, mineral wool requires a vapor barrier from the outside, otherwise it will get wet and lose its thermal insulation qualities.
It is not as convenient to insulate a loggia with cotton as using expanded polystyrene, since it is lighter and tougher.
Foam glass
Another modern look rigid heat-insulating building material is foam glass. This material is made by foaming liquid molten glass.
The material has good qualities and characteristics:
- Thermal conductivity - 0.04 - 0.08 W / m × ° С;
- Operational working density - 110 - 200 kg / m²;
- Water vapor permeability - 0.005 mg / m × h × Pa;
- Compressive strength - 0.7 - 4 MPa; bending - 0.4 - 0.6 MPa;
- Water absorption - up to 5% of the volume;
- Noise isolation - up to 56 dB;
- Moisture resistance - high;
- Environmental safety - complete;
- Chemical inertness is absolute;
- Air permeability - high;
- Service life is unlimited.
The instructions for installing foam glass also coincide with that of expanded polystyrene. Plates are glued and fixed with dowels, sometimes they do without glue. Further, the surface is plastered and covered with a mesh, on which the finishing layer of the facade coating is applied.
Advice! Drill holes for dowels in rotation mode without impact, since otherwise the hole will be of a larger diameter.
Conclusion
Solid brands of insulation have a number of advantages when insulating walls. Installation of these materials is simple and does not require special knowledge. In the video presented in this article, you will find additional information on this topic.
When arranging the floor, it is mandatory to insulate it. Thermal insulation will protect from the penetration of cold from below, retain heat in the room and distribute it correctly. This will reduce the cost of heating the premises in the cold season. When choosing a floor insulation, it is necessary to take into account many aspects so that it will serve for a long time and be “in place”, performing its functions efficiently.
When choosing floor insulation, consider the operating conditions
Mineral insulation are made from natural materials:
- Mineral wool: fiberglass, rock wool, slag wool. It is a blended fiber from rocks or other materials.
- Foam glass.
- Expanded clay - granulated fired clay.
- Cement-based mixtures with aggregates and additives.
Wood-based materials used for dry screed or empty space filling:
- Moisture resistant plywood.
Cellulose wool is used to insulate wooden floors
- Cellulose wool is blown out or simply filled up and rammed.
Polymer materials are not environmentally friendly:
- Polyurethane foam.
- Reflective polymer insulation.
- Roll insulation.
- Liquid polymer insulation with a foam structure.
- Liquid insulating paint.
When choosing which insulation is better for the floor, be guided by their technical characteristics and future operating conditions. The ideal option would be to use several materials at once at different stages of floor insulation. For example, expanded clay, basalt wool and roll insulation on top of the screed are suitable for a concrete floor.
Important! Polystyrene, polyurethane foam and extruded polystyrene foam emit toxic gas during combustion that can be fatal in two breaths. Therefore, if you decide to use them in construction, then lay them under a concrete screed, where there will be no contact with fire.
How to choose floor insulation
First of all, it is necessary to take into account what kind of floor - wooden on logs, concrete or "warm floor" system. In all three cases, different materials will be needed.
To insulate a wooden floor, mats or sheets of insulation are placed between the logs
For insulation of a wooden floor, a loose, porous material that does not hold its shape, free-flowing is suitable. It can be poured into the space between the logs, or mats, slabs, linens can be laid, depending on the form of insulation. It is very important that in this case the insulation “breathes” and lets steam through. After all, the wooden floor is equipped precisely so that the house "breathes".
For a concrete floor, solid heaters are suitable, which hold their shape well and do not deform under compression and bending loads. This is important, since the concrete screed will be poured from above. In this case, it is not necessary that the insulation "breathes", but it is imperative that it does not absorb moisture.
For the "warm floor" system, insulators will be needed the same as for the concrete screed, with only one caveat: they must have a foil film to reflect the heat coming from the "warm floor" towards the lower floor. You can use materials with aluminum spraying or lamination.
Characteristics of thermal insulation materials
Coefficient of thermal conductivity determines the ability of a material to transmit heat. It is equal to the amount of heat that passes through a material 1 m thick with an area of \u200b\u200b1 m 2 per hour, provided that the temperature difference on both sides of the material is 10 ° C.
Porosity is a very important indicator, it is determined by the ratio of the number of pores to the total volume of the material. Affects all other characteristics of insulation.
Vapor permeability material determines its ability to "breathe".
Water absorption affects the ability to use the material in high humidity conditions. The lower this indicator, the better.
Strength material is important for use in structural elementswhere there are compression loads.
Biostability means whether the material is able to withstand the action of pathogenic flora.
Fire resistance determines the ability of a material to withstand high temperatures for a certain time without collapsing.
Heat capacity - the ability of the material to retain heat under conditions of frequent temperature changes.
There are several more important characteristics:
- Density;
- Humidity;
- Temperature resistance;
- Frost resistance;
- Flexural strength;
- Fire safety indicators: flammability, flammability, smoke generation, toxicity of combustion products, etc.
Insulation for warm floor
When choosing insulation for the "warm floor" system, you need to pay attention to the ability of the material to redirect heat in the right direction and block its spread in the undesirable one.
To reduce heating costs, while not heating the ceiling to neighbors or the basement in a private house, it is advisable to choose a heater with a foil or laminated layer. Such material will prevent the penetration of cold from below and direct the heat coming from the "warm floor" system up.
For the "warm floor" system, the insulation must have a foil structure
It can be found under different names and trade marks: Izolon, Penofol, Isoflex, Energoflex. The material is produced in rolls 90-120 cm wide, 2-3 mm thick. It copes with the task perfectly, despite such a thin layer.
Extruded polystyrene foam is one of the most durable, durable and moisture resistant insulation
Produced in slabs that are easy to cut into the necessary pieces, easy to install and use. It has a very dense structure that does not deform or break. The cellular structure is filled with gas, the cells themselves are impermeable, due to which this material is not affected by moisture: it does not swell, does not absorb moisture. Extruded polystyrene foam is resistant to acids, alkalis or alcohols. Fungi and bacteria do not take root on its structure. It is durable, as it does not deteriorate under the influence of precipitation and the sun and does not react with most substances. Despite the indisputable advantages, extruded polystyrene foam has a number of significant disadvantages: it "does not breathe", which means that it makes no sense to use it to insulate a wooden floor, and it is flammable. Although this material is normally non-toxic, it emits poisonous gas when it burns. In the "warm floor" system, it will be completely isolated from the environment by a concrete screed, so it can be safely used.
Cork material is the most environmentally friendly and natural insulation
Made from cork oak bark. This material is the most environmentally friendly and natural. It does not rot, does not "shrink", is inert, resistant to bending and compression loads. In addition, the cork is easy to cut, which affects the speed of working with it. Lifetime cork backing may be about 50 years old. The cork material does not burn, and during smoldering does not emit harmful substances. Withstands temperatures up to 120 ° C. It is produced in the form of plates with a thickness of 25-50 mm.
Insulation for the floor under the screed
It is better to insulate the concrete floor in several stages, since it is the coldest.
It is convenient to fill expanded clay under a concrete screed or add to concrete instead of gravel
- the ideal option for insulating floors on the ground. It is a rounded granule made from clay by firing it with the addition of peat, sawdust and other additives. The sizes of granules can be different, the heat-conducting characteristics of the material also depend on it. Expanded clay is resistant to temperature and humidity changes, lightweight and does not create a large load on the foundation. Due to the porous structure, in addition to thermal insulation properties, it has good sound insulation characteristics. The indisputable advantage of expanded clay is its environmental friendliness and naturalness.
Solid slabs of basalt wool are laid under the concrete screed
- one of the varieties of mineral wool, is a hard insulation in slabs. It is laid on the floor in a checkerboard pattern under a concrete screed, which must be at least 4 cm thick. This material does not burn, is resistant to deformation and vapor permeable. Basalt wool has high thermal insulation characteristics and withstands high temperatures.
Also used for insulation of concrete floors under screed.
Polyfoam is one of the most common insulation materials due to its low cost
You can also use. Its main advantage is its low cost and ubiquity. It is durable, easy to use, absorbs little moisture and has high thermal insulation properties. Among the disadvantages can be distinguished: it is flammable, exposed to sunlight, "does not breathe". When using foam as insulation under the screed, these disadvantages are insignificant and can be neglected.
Correctly selected floor insulation will create high-quality and durable thermal insulation. Compare the characteristics of insulation, weigh all the advantages and disadvantages, find a balance and be sure to take into account the operating conditions.
All produced modern manufacturers finishing and building materials are aimed at saving. Many may be surprised by this conclusion, especially when you think about the price of them.
Let's try to explain our point of view: the topic of our article is material for insulating walls inside the house, and they are designed to save heat in the room. Heat loss directly depends on the quality of the insulation, and we will talk about how to choose it correctly today.
Thermal conductivity of walls made of different materials can differ significantly, which is why it is so important to choose the right insulation (see), for example, walls made of light warm material, do not need a radical approach, unlike a tree, which has a habit of freezing in winter.
The factor of choice is especially important for owners of old buildings, houses that eventually lose their energy-saving properties can also be remodeled so that it will be like new. So how do you choose the right insulation?
First of all, it is necessary to understand what the main criteria should be present in its quality characteristics:
- Thermal insulation level. The choice of insulation is not a situation to which the adage that butter cannot spoil porridge is applicable. If your walls are built of thick ceramic bricks, then the use of strong heaters does not make sense, you just spend extra money on them, and energy savings will remain the same.
- Steam permeability... The factor is especially important for wooden houses, or for old buildings. The fact is that it is on them that condensate most often accumulates, which over time can develop into fungus or mold. The insulation in this situation must have a high degree of steam transmission.
- Safety. Since we are talking about materials for insulating walls from the inside of the house, it is very important that they are completely safe. This applies to both fire safety, the insulation should not support combustion, and about environmental cleanliness, it is impossible that the composition of the insulation contains harmful chemical compounds that can harm human health.
- Heat capacity... Often, the quality of the insulation directly depends on its thickness, and this is very bad, inside the house, every centimeter is important, and when using such materials, you can lose up to 15 centimeters from each wall, and when all four walls are taken into account, the loss in area becomes very noticeable ...
These are the main selection criteria, and in addition, ease of installation can be attributed, especially if the repair is done by hand, and you do not have a huge set of tools. Running a little ahead, we note that not all heaters you can install yourself.
Important! The most important thing when choosing a heater is an accurate calculation of the heat capacity, the final result will depend on it, and in some cases, such a calculation helps to significantly save material costs, which is also important.
So, we figured out the main criteria, but what material does all of them have? To one degree or another, any, but in different proportions, therefore, below we will take a closer look at the main and most popular types of insulation that can be used inside the house.
Soft insulation based on cotton wool
Who among us does not remember the notorious glass wool, after touching which, you could get a serious burn. Modern cotton wool is no longer the same, and you can even sleep on it without getting any unpleasant sensations. all that the manufacturers needed was to exclude ground glass from its composition, and it turned out to be one of the most popular materials for wall insulation today.
Two factors can be attributed to the main advantages of this material:
- A light weight. Cotton wool does not create any load on walls and partitions, and this is especially important for houses built from lightweight materials, or on a weak foundation, where every kilogram is important.
- Ease of installation... In some cases, it is generally unnecessary to attach cotton wool to the base; it is simply fixed between the crate guides.
An interesting fact is that the second point often becomes a disadvantage, since with constant contact with moisture, cotton wool collects it in itself and, becoming heavier, simply falls into lumps. Something similar happens with cheap synthetic winter jackets, which after washing dump all the insulation into the base.
If your walls do not have contact with water, then you do not need to worry about this, but in some rooms in the house, such contact simply cannot be avoided, therefore it is advisable to make additional fastening of the material to the wall using glue or special plastic dowels with wide hats.
Important! Choose mineral wool only from reliable and trusted manufacturers, since some unscrupulous "firms" use formaldehyde in it to reduce the cost of production, which, accumulating, can cause significant harm to health. The price of such dangerous cotton wool may be lower, but is it worth the spent health? Surely, the answer to this question is unequivocal.
Basalt wool
Many people ask themselves what material to insulate the walls of the bathhouse, and so, basalt wool is best suited for these purposes. Unlike mineral wool (see), it contains natural volcanic basalt, which, in addition to heat-conducting qualities, has the highest resistance to temperature.
Such cotton wool can be used to insulate not only walls, but also a stove, and even a chimney. It is completely insensitive to high temperatures and open flames, and when heated, it does not emit harmful substances, which is also important for baths and saunas.
Basalt wool is more expensive than mineral wool, but also quality characteristics it has much higher, therefore, if your budget for repairs can afford it, then the choice does not even arise. Often, its qualities may seem excessive, but it is worth noting that basalt is much more resistant to contact with water, and in addition to the fact that it does not support combustion on its own, in the event of a fire, it can even prevent the spread of fire along walls and partitions.
As you can see, roll material for wall insulation is very convenient and practical, but you shouldn't dwell on it without appreciating all the advantages of other heaters, which will be discussed below.
Styrene-based solid insulation
Many are frightened off by the word styrene, from it directly emanates from chemical formulas and harmful production. But this is a common misconception that has come to us from the distant past.
We all remember polystyrene (see), which was previously used to transport fragile items. Today it is also used as a heater, and very good insulation, which perfectly retains heat, and at the same time does not deform over time.
There is an opinion that polystyrene is harmful to health, and this is also a delusion, chemical reagents are used in its production, but they are completely safe. To note at least the fact that in the walls insulated with this material, rodents very often start up, which, as you know, are very picky in elections building materials for their homes.
The presence of rodents, of course, can be attributed to the disadvantages of this insulation, but it is very easy to get rid of them even at the stage of construction or finishing the wall, it is enough just to treat the surface with special fluids, and the mice will bypass your house.
It is also believed that polystyrene is a hazardous material, since it is highly flammable, and during combustion it emits harmful corrosive substances, which, in case of danger, can become a significant obstacle to evacuation.
But here it should be noted that this is only relevant for cheap materials, and high-quality foam contains special flame retardants that make it immune to high temperatures. And even in the presence of an open flame, it simply loses its shape, but does not ignite.
Penoplex
One of the modern varieties of styrene insulation, which differs from foam in its higher density and the ability to retain its shape under the most intense loads. Choosing which material to use for insulation brick wall, it is best to give preference to this particular material, since with the same thermal conductivity with foam, it will be much thinner, but at the same time stronger.
This effect is achieved due to deep pressing in production, as a result of which, significantly more raw materials are consumed per cubic meter. The result of this is density, and the ability to keep warm even in severe frosts outside.
The hardness and resistance of the foam to stress and mechanical stress, allow it to be used not only as a heater for walls, but also in under the roofing space, and even for sealing floors.
Moreover, in some cases, penoplex is used as a substrate for the road surface, in those situations when it is necessary to get rid of the constantly forming ice on the surface.
There should also be no problems with fixing this insulation, since it is fixed on glue or on the same dowels as mineral wool. And besides this, each foam panel is equipped with grooves and ridges that improve the adhesion of the segments to each other and eliminate cold bridges at the joints.
Advice! Despite the fact that the plates are tightly connected to each other, it will not be superfluous to go through all the joints with penoizol, for more reliable insulation.
Polyurethane foam
The more common name for this truly unique insulation is penoizol, and most of us are accustomed to perceive it as a gap insulator that is used when installing doors or windows. Such foam is sold in cylinders, and if you imagine how many of them are needed to cover an entire wall, you can be horrified at the final cost. But with polyurethane foam for insulation, things are a little different.
In this case, it is produced in the form of two separate substances, which, when mixed, form that very foam. For spraying, special expensive equipment is used, so you will not be able to insulate yourself. Of course, you can buy a foam sprayer, but this is unlikely to be cost effective.
In order to better understand the whole process, we suggest watching the video in this article. This is not a manual for work, but rather just a video that will help you understand that without experience and certain knowledge, it is better not to take on this business, but entrust it to specialists who are familiar with all the subtleties.
If you are looking for non-combustible materials for wall insulation, then foam is exactly what you need. Upon contact with an open flame, it simply loses its shape, but at the same time it does not support combustion and does not emit harmful toxins.
An interesting fact is that penoizol can be used not only as a material for insulating walls from the inside, but also outside the house. Moreover, there is a technology for injecting insulation into already built walls, in which there are voids. This practically does not exert a load on the foundation, and the walls become not only warmer, but also stronger, since the foam reliably holds the partitions together and makes them a real monolith.
Drawing a conclusion from all of the above, it can be noted that polyurethane foam is one of the highest quality and most reliable heaters, which has unique qualities that no one else has:
- A light weight. Can be used fearlessly for insulating wooden and plasterboard partitions.
- Safety. After hardening, the foam does not emit harmful substances.
- Reliability. The absence of joints completely excludes the formation of cold bridges.
- Durability. Foam is not afraid of temperature drops and high humidity.
Of the disadvantages of this material, one can single out the relatively high cost, and the impossibility of self-application, but given the positive aspects, you can no longer pay attention to these nuances. So, we told you about best materials insulating walls, and which one to choose is up to you, the most important thing is to strictly follow the rules and recommendations for choosing, as well as to calculate in detail the heat capacity of the walls and insulation.