Wall formwork may be needed when erecting concrete vertical partitions. For its manufacture, metal or strong wood is used so that deformation does not occur when the hardened concrete expands. The construction of such a frame on your own will help not only to significantly save money, but also to easily install the formwork with your own hands next time.
- removable;
- non-removable.
Removable structures can be used many times. They are ideal for low-rise buildings. Any such form is a kind of constructor. When assembling, nuts, washers and bolts are used.
The fixed form is most often used in the construction of insulated walls. It is built from plastic or expanded clay concrete - materials that retain heat.
For the manufacture of both types, the following materials are used:
- Wood. Suitable for all types of structures. The lightest and cheapest option. It is best to use moisture resistant species: spruce, cedar or alder. Insofar as wooden frame can be disassembled at the end of the work, and then used again, then these expensive rocks will pay off over time, and the erected walls will last a long time.
- Metal. It is relevant for large-scale construction. Such a frame is welded from 2 rows of metal. The resulting metal structure is particularly durable, but not suitable for DIY construction.
- Plywood, corners and fittings. Since plywood is a flexible material, the formwork from it must be reinforced with reinforcement.
- Styrofoam or plastic. It is used for non-removable structures. Differs in ease of installation and dismantling, does not require special temperature conditions during storage, does not deform even after 50 uses. The maximum wall thickness for plastic formwork is 40 cm, but this is quite enough for individual construction.
Assembly of movable and removable elements
Movable (sliding) formwork requires less material, but its manufacturing technology requires more time. For a movable version, you will need the following materials:
- transverse and longitudinal shields with stiffeners;
- spacers;
- bolts;
- nuts;
- cutting pipes.
The work consists of the following stages:
- Installation of formwork at the corner of the foundation.
- Sheathing of the frame with transverse shields.
- Pouring concrete.
- After the solution has completely frozen, the formwork is disassembled.
- The structure is moved to a new place, fixing it on the already erected fragment of the wall.
- Then the process is repeated.
In order to save time, several sliding structures can be made to erect all the walls at once. For the installation of the simplest removable formwork, boards of the same length with a thickness of 2.5 to 5 cm are suitable.The assembly is as follows:
- Long beams are driven in at the corners of the foundation and in the middle of the planned wall. Shorter boards are nailed every 1 m. The boards prepared for shields are knocked down with slats. In this case, the length of the resulting shield will depend on the length of the boards, and the height should slightly exceed the height of the wall being built. Here it should be borne in mind that the nails need to be driven not into the stitching strips, but into the boards themselves, then the hats will turn out to be on the flat side of the shield.
- Shields are nailed to each other with connecting strips. Internal shields are nailed to the supports. Next, the supports for the inner shield are installed. External shields and props are nailed to them.
The formwork is ready for pouring the walls.
The construction of modern buildings and structures is carried out mainly according to special projects. Structures of complex configuration are erected from monolithic reinforced concrete. Monolithic structures are formed by pouring concrete into a system of enclosing planes - formwork, which can be made of various materials.
Wall formwork, as a type of retaining systems, allows you to accurately erect the load-bearing elements of the structure without loss of quality. In this article we will look at what and how to make a formwork for monolithic wall.
Wall formwork is a panel system different sizes
The purpose of wall formwork is to keep the liquid mass of concrete in the desired shape and volume until it solidifies completely.
Materials for fencing must have sufficient strength and reliability to withstand the pressure of the poured concrete mass without deformation. The made frame of the fences must be a sealed structure that does not allow leakage of the solution.
Wall formwork is a system of panels of various configurations and sizes. Materials for wall formwork determine the names of the types of fences:
- wooden shields;
- construction plywood;
- metal shields;
- plastic panels;
- aluminum shields;
- non-removable blocks;
- auxiliary material.
A frame made of wooden panels for the formation of a monolithic concrete wall is assembled from hardwood planks.
When building a low-rise small house the formwork for the walls is assembled from boards and timber with your own hands.
As materials for formwork, as a rule, dry edged boards with a smooth surface with a thickness of 25 mm to 30 mm are used. The main fastening elements of the formwork are beams with a cross-section of 50 x 50 mm and 70 x 70 mm.
Wood is a fairly strong building material that can be easily processed. When installing fasteners for wooden panels, it is always possible to make the necessary parts from the available lumber.
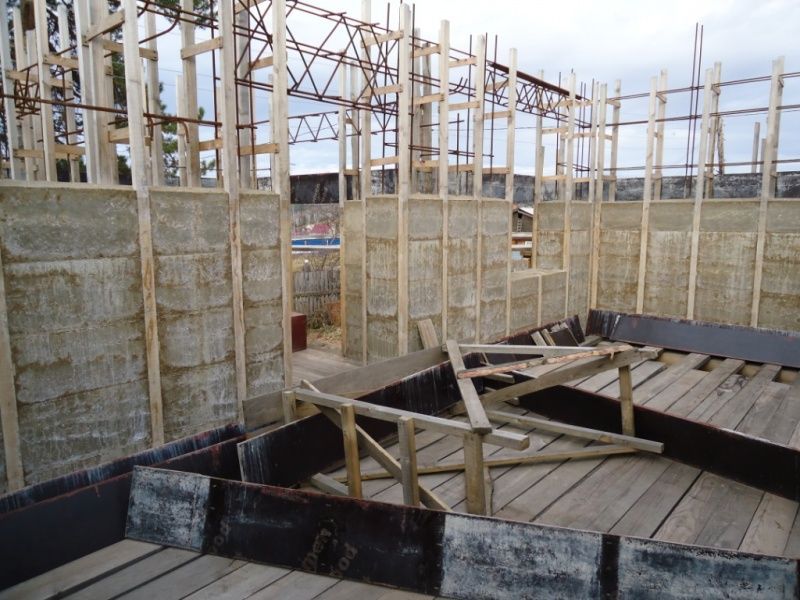
The removable formwork made of wooden panels for walls must be dismantled after the concrete monolith has hardened.
During assembly, all formwork elements are fastened with nails that fit well into the body of the tree and firmly fasten the structural parts. Doing these works with your own hands will not cause much difficulty.
The walls of the house will be smooth if the inner surface of the boards is covered with a polymer film.
When disassembling the fences, the shields will be easily separated from the monolith without damaging the concrete surface.
For the construction of monolithic walls of large objects, wooden shields are not used.
Construction plywood
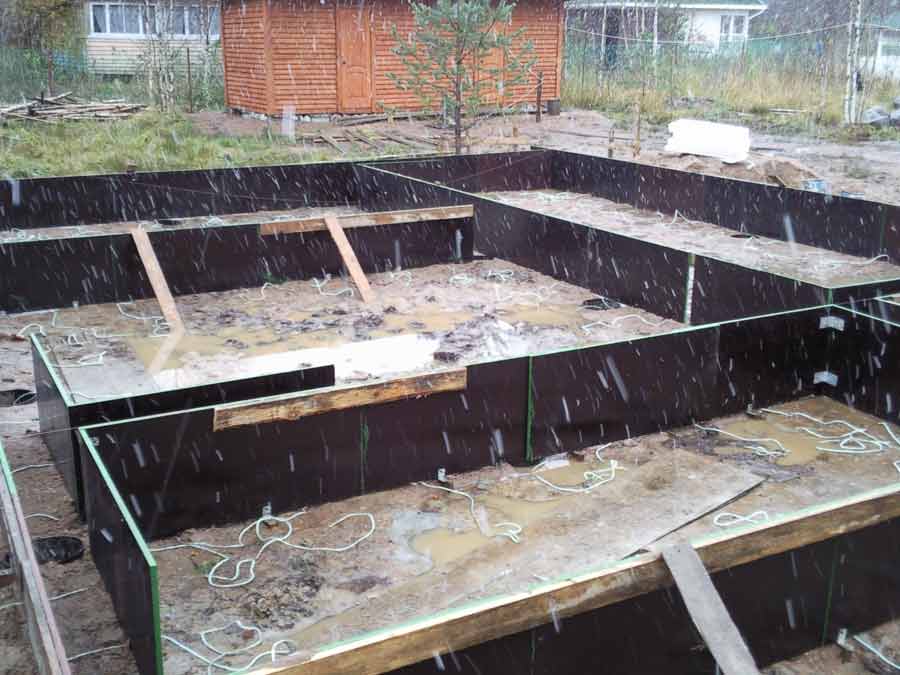
The plywood used for formwork consists of several layers of hardwood veneer glued together. Veneer sheets are held together under strong heat and pressure. Thanks to this, construction plywood has excellent performance characteristics.
The absolutely smooth surface allows for perfectly flat walls. can be reused. Fencing system installation technology from of this material practically no different from the installation of a frame made of wooden panels. A significant difference is that screws are used instead of nails as fastening hardware.
If you have experience in construction, it is quite possible to build your house from monolithic walls using self-assembled formwork from construction plywood.
Metal shields
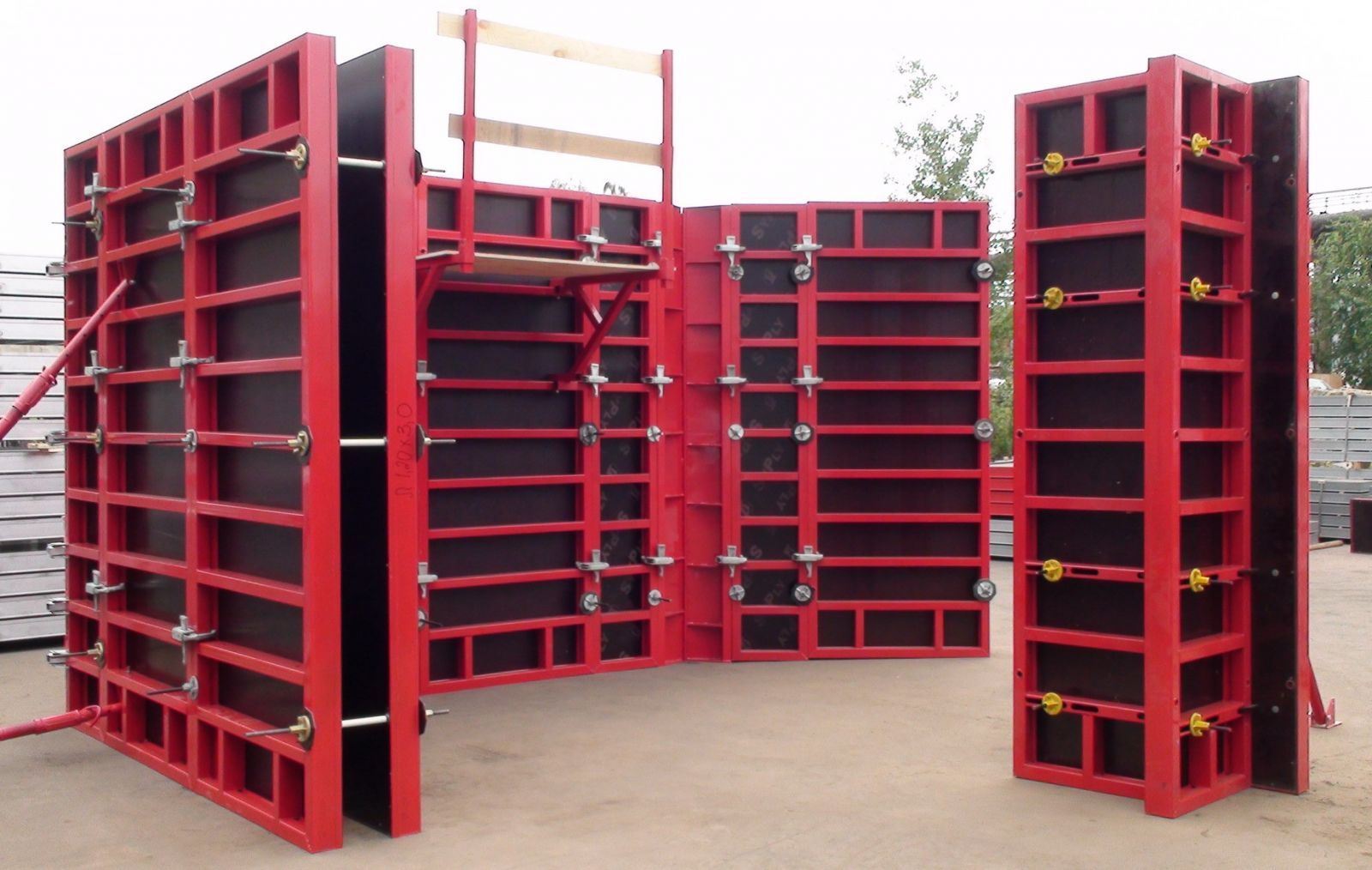
Metal sheets with stiffening ribs are produced in various sizes. Steel panel kits include a complete set of elements for fixing the boundary planes in design position... Locking devices provide sealed joints between steel panels.
Steel shields are used for the construction of walls in large industrial and civil buildings. Large-sized panels are heavy. Removable formwork made of metal panels is mounted using lifting mechanisms (tower cranes and truck cranes).
There are two types of metal fences:
Movable shields
The climbing formwork made of steel panels allows the erection of high walls in a short time. At a time when the lower tier of the monolith has gained strength, the steel panels are dismantled and installed at a new level.
Metal shields can be rearranged only with the help of hoisting machines and mechanisms.
The sliding panel system is a complex mechanized set of enclosing structures, consisting of a set of steel elements, lifting devices and rigging devices.
The technology of forming a monolithic wall using is that during the layer-by-layer formation of a monolith, a number of shields move in the necessary direction to fill the next level of a monolithic wall.
The main disadvantage of steel shields is metal corrosion. However, with timely care of the metal, the fences will last for many years.
Due to the high bearing capacity metal shields are used to fill retaining walls that support massive building elements. For information on how to work with sliding formwork, see this video:
Often, in order to eliminate the threat of destruction of a house, they erect close to its walls monolithic structures in the form of a triangular figure with a right angle at the base of the retaining wall.
To erect monolithic walls of his house, a developer can rent small metal shields from a construction organization. Do-it-yourself installation of a rented small-panel metal formwork will save time and money.
Plastic panels
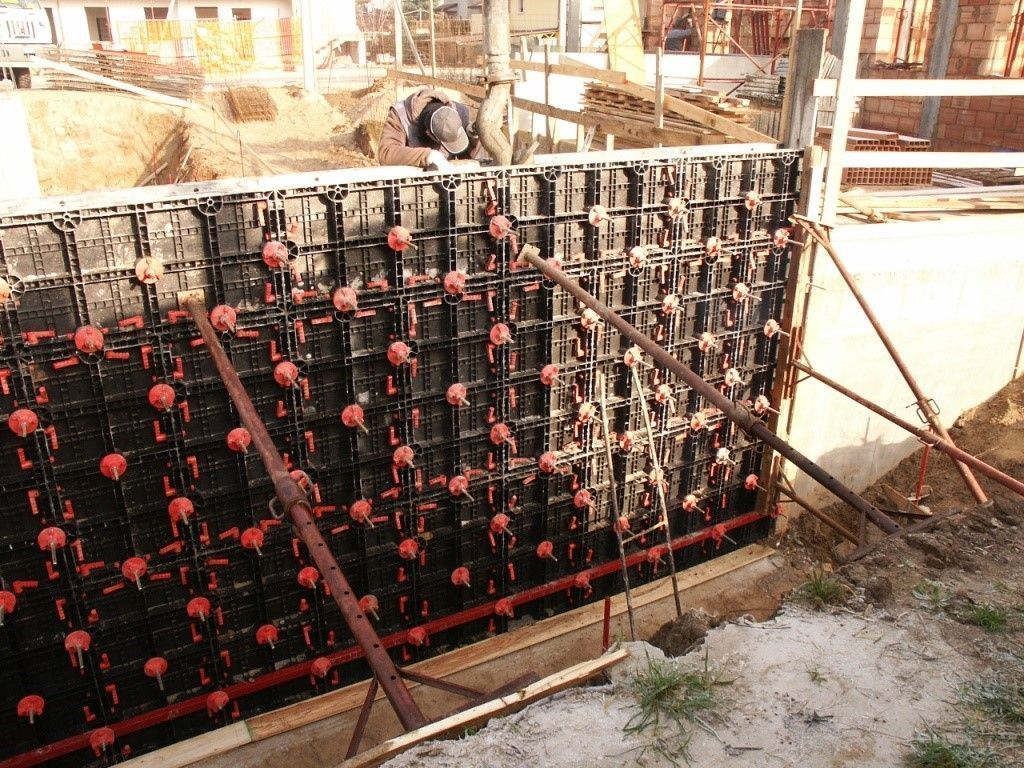
Polymer panels compare favorably with metal shields by their low weight. Shields are reusable structures.
Plastic fences can be easily rearranged by hand. They are used to fill monolithic walls of low height.
The outer surfaces of the panels are easily deformed from accidental impacts.
During installation and disassembly of the plastic frame, you need to be extremely careful with the panels.
Plastic panels are not cheap, so it is also profitable to rent them.
Aluminum fences
By the way of application, aluminum panels are similar to metal formwork. Fences made of non-ferrous metal practically do not corrode and are lightweight. For the construction of walls, the developer can install vertical aluminum fences with his own hands. An example of the application of aluminum formwork, see this video:
The disadvantage of the panels is their high cost. Aluminum structures require careful handling, since they are easily deformed even from small accidental force effects.
Fixed blocks
Recently, non-removable fences, which are made in the form of volumetric blocks of foamed polymer (polyurethane), have gained wide popularity.
The inner cavity of the polymer blocks is poured with a concrete mixture. The polyurethane surface becomes part of the walls. The side surfaces of the walls are painted or covered with decorative facing material.
Polyurethane itself is an excellent thermal insulator. Walls with such polymer coating keep indoor temperature well in winter.
Auxiliary material
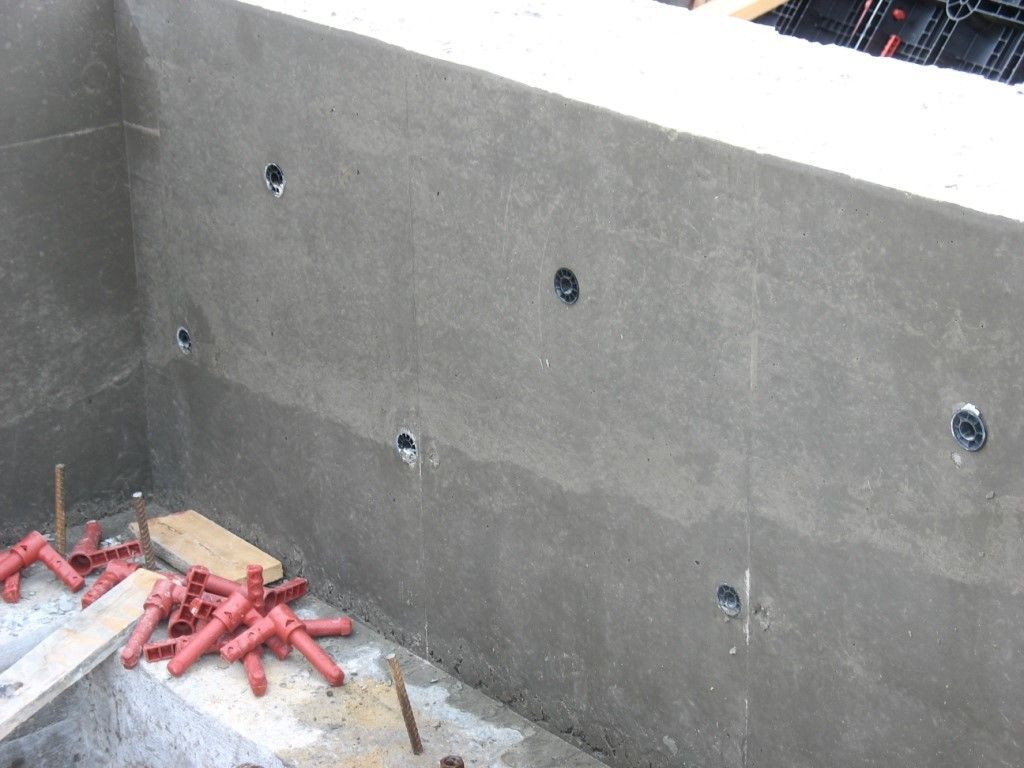
In the household, there is often a need for the construction of small courtyard buildings.
For the construction of monolithic walls of small thickness, the owner of the house prepares formwork from auxiliary material.
It can be slate, sheets of asbestos cement, scraps of corrugated board, plywood or any moisture-resistant sheet material.
Summarizing the above, we will summarize in the table brief characteristics and the scope of application of the most popular types of formwork.
№ | Types of fences for monolithic walls | Scope of application | Frequency of use |
---|---|---|---|
1 | Low-rise buildings | Disposable | |
2 | Construction plywood | Low-rise buildings | Disposable |
3 | Metal shields | Large multi-storey buildings | Reusable |
4 | Plastic panels | Large multi-storey buildings | Reusable |
5 | Aluminum fences | Large multi-storey buildings | Reusable |
6 | Fixed blocks | Civil objects | Disposable |
7 | Handy material | Light outbuildings | Disposable |
From the data presented, it is seen that under the same conditions, formwork of different types can be used. On final choice the enclosing structures are influenced by the technical and economic indicators of the building project.
In areas where metallurgical enterprises are located, you can always purchase production waste - boiler slag. This is a very cheap building material that is used in the construction of summer cottages and small private houses. For more information on the material, see this video:
Slag concrete is prepared from a mixture of slag and cement in a ratio of 5: 1. Sometimes lime and clay are used instead of cement.
For the construction of monolithic walls, a special reversible one is made of cinder concrete. The fence is a collapsible structure made of wooden shields and clamps.
Slag concrete is poured into the formwork in layers with a thickness of each layer of 200 mm. Each fill is tamped, carefully distributing the material along the corners and perimeter of the formwork at the junction of the walls. As the next layer of the mixture hardens, the formwork is moved up.
Building a house from monolithic slag concrete will cost much less than erecting a similar structure from monolithic reinforced concrete.
- Types of formwork when building a concrete house
- How to make a brick from concrete
Concrete houses are renowned for their strength and durability. The quality of such a building is significantly superior to that of any other building material, be it brick or wood. In the past, only industrial buildings or multi-storey residential complexes were erected on a concrete base. Most people building today own house, more and more are turning to this technology of homebuilding.
A house made of concrete is a solid, warm structure that does not require the purchase of expensive equipment and materials.
At the moment, the idea of \u200b\u200bbuilding a house from concrete has gained wide popularity in our country. For this reason, land owners planning to build private house or a cottage, they want to get acquainted with the construction technology in more detail in order to build a concrete house with their own hands. In addition to strength and durability, such a structure does not require expensive building materials. The erection of a concrete building is not laborious when compared to structures for which brick is used.
A concrete house can be finished and decorated with any material, and its walls can be insulated with a heat-insulating layer during the construction process. This is due to special technology permanent formwork... Below are several methods of building a house from concrete with your own hands, which include the above technology.
Pros and Cons of Concrete Buildings
Technical characteristics of concrete of different grades.
A concrete building has both advantages and disadvantages. Among the advantages, a high-strength cast frame can be noted, which increases the durability of the structure in the event of exposure to such phenomena as seismic activity, proximity groundwater and atmospheric precipitation, which has a devastating effect on the structure of the structure.
The structure is devoid of joints, which are ubiquitous in buildings erected from a different material. Heat energy is released through the joints, which leads to an increase in material costs during the cold season. The monolithic structure is devoid of this drawback.
A concrete house can be built on any type of soil and soil layer, in addition, the construction of a building can be carried out in any weather conditions. The construction of such a house can be completed in a short time, concrete will be much cheaper than other building materials, for example, such as brick.
The concrete structure does not impair reliability if the structure is uneven. When sawdust, expanded clay and perlite are added to the solution, there is no need to pour a massive foundation, since the walls of the house become lightweight.
If the house will be built using the permanent formwork method, there is no need for a separate arrangement of the heat-insulating layer. In addition, this will reduce the thickness of the walls.
A number of tools are required to work with concrete.
Concrete walls are characterized by high sound insulation, which is achieved due to solidity. And the overlap between floors can be constructed from various building materials.
Since the building is evenly spaced, micro cracks and cracks will never appear in it.
Concrete houses have their drawbacks, but there are much fewer of them. When erecting the upper levels of the house, it is impossible to do without a special pump for concrete mortar... Laying concrete slabs as floor slabs is a rather laborious process. This procedure will require high strength scaffolding.
If the method of permanent formwork was chosen, in the future it will be necessary to equip the supply and exhaust air exchange. Otherwise, there is a possibility of increased humidity, which will lead to the formation of mold and wear of building materials. The formwork must be plastered, as it is a flammable material that emits harmful substances during combustion.
The concrete structure must be grounded without fail. This is due to the fact that in the structure monolithic slabs there are iron pins.
Back to the table of contents
Tools and equipment for work
To build a concrete house, you will need the following tools, accessories and equipment:
To build walls, you need to build a formwork.
- construction mixer and concrete mixer;
- shovels and container (when mixing the solution by hand);
- a cart or stretcher for transporting the solution;
- construction hair dryer;
- reinforcing network;
- nippers or scissors;
- a knife for cutting foam;
- hammer and nails;
- roulette and level;
- steel and wood supports;
- wire hook for knitting;
- puncher;
- set of industrial tools.
Self-construction of a concrete house will not require building materials that are not included in the above list.
Back to the table of contents
Do-it-yourself concrete house construction
Scheme of removable formwork for the construction of walls.
As mentioned above, construction concrete house can be carried out in two ways: fixed and removable formwork. Each construction method has its own characteristics, both during construction and in the process of servicing walls and other elements of the building.
The removable type of formwork is calculated individually for each layout. The purpose of its arrangement is to perfectly repeat all the contours of the planned building. The main material for formwork is wood, metal or plastic.
The opening in the middle of the formwork walls is the actual volume of the final wall of the structure. It is calculated by determining the lowest possible temperature in the existing region. The calculation also depends on the thermal conductivity of the monolithic wall. The walls of the formwork are fixed with nuts, pins and washers. To simplify the dismantling of the shields, after pouring the concrete solution, corrugated tubes must be put on the studs. This will help protect them from direct contact with the mixture.
This formwork method allows the casting of concrete mortars with low thermal conductivity. Walls made in this way will be able to store more heat energy inside the structure, but the degree of their strength may decrease.
It is worth paying special attention to the reinforcing layer. For this, either steel or plastic reinforcing nets are placed in the formwork. To increase the strength of the walls, you can add reinforcing lathing to the structure.
The solution is poured in several passes. For 1 cycle, it is necessary to pour no more than 0.5 m of concrete. The next approach is done after the previous mixture has hardened. The concrete solution must be tamped with a deep vibrator, paying special attention to the end parts. As soon as the mortar hardens, it is necessary to move the formwork upwards. Pouring is carried out in this way until the required height of the walls to be erected is reached.
For the strength of the structure, the wall is reinforced.
Finishing work and installation thermal insulation material can be carried out only after 1-1.5 months after pouring concrete, since the structure must finally be strengthened.
Materials such as mineral wool, polystyrene foam, warm plaster and extruded polystyrene foam can be used as thermal insulation.
In some cases, an insulating layer is created on the basis of a well facade. To do this, you need to step back a little from concrete base and lay out another wall with hollow brick or stone. The resulting gap can be covered with any insulation material. It is worth remembering that this method of insulation has less durability compared to expanded polystyrene and brick.
Back to the table of contents
Such formwork can have a variety of designs: longitudinal, window-sill, above-window, angular. Not removable formwork has a similar structure to the children's Lego constructor.
This method of wall construction is very popular due to the built-in thermal insulation layer. Indeed, when arranging fixed formwork, you can save a lot of money.
The advantage of permanent formwork is that it has built-in reinforcement and an insulating layer.
After posting waterproofing material at the base of the structure, there is a foam formwork on it, which is fixed with the help of special guides in the thorn and in the groove. This ensures that the concrete is poured reliably, preventing any leaks at the mating points.
The volumes of the foam formwork come in various sizes. If necessary, it is possible to order the required amount of material from a factory that specializes in the production of expanded polystyrene. The slabs have a standard width of 15 cm, where 5-8 cm is a foam layer. This thickness allows you to keep the room temperature indoors at 5 ° C outdoors without using a heating system.
In the process of pouring such a formwork, it is forbidden to use any warm solutions. It is recommended to use only concrete mixes. This is due to the fact that warm solutions have an increased sensitivity to vapor permeability. This causes excessive condensation to form, leading to increased levels of humidity inside the house.
Upon completion of construction, there is no need to take care of the thermal insulation layer. You only need to cover the polystyrene boards decorative trim or sheathe the building with composite panels.
The construction of a capital structure with a minimum budget has its own characteristics. The main feature is that the maximum possible number of processes will need to be performed independently. Taking into account the fact that no capital construction is complete without the construction of formwork. this technology it will be advisable to master. Do-it-yourself formwork - the technology is not complicated, but in many ways even interesting.
Depending on the purpose, the formwork can be for slabs, for load-bearing walls, as well as for mines and columns. Almost all of them are removable. All kinds of screed elements are used as components of the formwork: studs, bolts. nuts, as well as the limiting plane itself - plywood, wood, steel planes (types of formwork). Do-it-yourself removable plywood formwork (see Fig. 1) is the most correct solution in case of existing financial constraints. Firstly, such formwork can be purchased relatively inexpensively, and secondly, its installation is extremely simple, you will not need to apply for paid help from specialists. Considering the surface quality of the plywood formwork, the appearance of the resulting concrete elements is close to ideal. Thus, further revision of the walls will be characterized by minimal labor intensity. Similar results can be achieved wooden formwork, however, it is more expensive than plywood.
The plywood sheets are positioned so that the resulting internal cavity is identical in shape to the desired concrete element. After that, the plywood is fixed with screeds, and concrete is poured into the cavity. If, in the process of pouring concrete into the formwork, the plywood elements begin to deform under the generated load, it is advisable to install additional spacers (pegs). After pouring, the concrete is allowed to stand for about two weeks before removing the formwork.
Fig. 1. Plywood formwork
Construction technology from fixed formwork SOTA
Description of video material:
The technology of building a house from a fixed formwork reinforced polystyrene foam panel SOTA. Perhaps the best construction technology worldwide ($ 100 / m2). We build cheaply with our own hands. www.opalubka-info.ru
Formwork for monolithic expanded clay concrete from plywood
Expensive construction Materials many cannot afford it now. In these conditions, it is economical to erect walls of capital structures using monolithic concrete... In this case, the formwork design plays an important role.
To reduce material costs and physical efforts, I use the formwork of my own design. Its peculiarity, firstly, is that the formwork panels are mounted directly on the walls, and secondly, in the way they move upward as the wall grows.
Reusable formwork panels - wooden, frame construction (races 1). I made the frames of the panels from bars with a cross section of 50X50 mm, sheathed them with sheets of plywood 10 mm thick, soaked in hot drying oil, and painted them. The holes in the panel with a diameter of 14 mm are used for the installation of ties. All wall panels have the same dimensions. I do not advise increasing the height of the boards, because when the thickness of the cast concrete layer is more than 40 cm, its setting is slower.
Along the side edges, the shields are connected to each other with M8 tie bolts (Fig. 2) passing through holes with a diameter of 10 mm in the corners, when attached to the shields with screws. The diameter of the screws is at least 5 mm.
The number of shields is determined by the length of the perimeter of the building. Experience shows that the strength of the shields of the accepted dimensions is quite sufficient for the construction concrete walls thickness up to 25 cm. Corner boards are structurally similar to wall boards, differ only in size and method of attachment at the corner ends (see Fig. 2).
I made ties from steel rods with a diameter of 12 mm, cut M12 threads at the ends. Picked up washers and nuts. Each pair of shields requires 6 ties. The wall thickness is determined by the length of the spacer. I cut the sleeves from half-inch water pipes... In the process of work, they remain walled up in the wall, their number is determined by the height of the walls.
For a building made of monolithic concrete, a reliable strip foundation... Its top must be carefully aligned horizontally. I placed formwork panels on the foundation (Fig. 3) and fixed them with ties. Bolted the shields along the side edges. At the corners of the foundation, it is advisable to vertically install the lighthouse poles, pulling a wire "cast-off" between them, with which you can more accurately set the shields along the length of the wall.
To control the verticality of the walls, I used a plumb line, and checked the linearity visually - "by eye". Embedded parts, for example, doorway pillars, were placed on the foundation in advance, before the installation of formwork panels on this section of the wall.
The concrete mixture was poured into the formwork only up to the level of the upper screeds. Reinforcement of walls with steel reinforcement is required. To reduce the consumption of cement in the formwork, I laid aggregate: broken bricks, chipped stones and fragments of concrete blocks. I do not recommend overusing the placeholder. The cast part of the wall was covered from above with a plastic wrap, which protects the concrete from dehydration and cracking during setting.
After a couple of days, the concrete set, and I began to rearrange the formwork. I unscrewed the upper middle tie by the thickness of the shield, and removed the rest, loosened the bolts at the ends of the boards and turned the boards 180º around the tie like around an axis. I installed the other five ties, and a pair of shields was clearly fixed on the wall. I did the same with the rest of the wall shields. Connecting them with bolts at the ends, as a result, he mounted almost the entire formwork of the next tier of the wall. I didn't have to lower the wall boards to the ground.
With corner shields, this trick did not work, and it was more difficult to put them. It's good that my garage only had four corners!
Before pouring the next portion, I always cleaned the surface of the formwork panels from adhered concrete - the surface of the wall turned out to be smooth. I sealed the holes from the screeds with mortar. My partner and I erected the walls of the garage in 10 days; I used a concrete mixer to prepare the concrete mixture.
Editorial note... For the manufacture of shields, we should use a conductor template, according to which it is easier to control the outer dimensions of the shield and accurately drill the mounting holes.
The adhesion of concrete to the shields will be significantly weakened by the application of a release agent to the surface of the shield - a mixture of solid oil with diesel fuel. Concrete can be compacted by tapping on the walls of the panels with a hammer with a rubber nozzle.
In the construction of buildings more solid than a garage, the holes from the screeds can be used by hammering wooden plugs into them with a seal. This will significantly speed up the work on the installation of heating pipes, water supply and electrical wiring cables, hanging shelves, installing racks, fastenings for staircases, etc.
Formwork of this type can be used when concreting the walls of basements, cellars, wells and other structures buried in the ground, especially when they are arranged in cramped conditions, for example, in a garage or in the basement of an already rebuilt building. The formwork will be effective when installed only from the inside of the foundation pits.
Author O. Kalabugin
DIY plywood formwork
In one-story construction, when pouring foundations and making other concrete parts, plywood formwork is often used. The choice of this material for formwork is explained by the fact that the plywood sheets have a smooth and even surface, which is ideal for pouring concrete. In addition, plywood has good moisture resistance. If laminated plywood was used for the manufacture of the formwork, then this formwork can be used several times. Moreover, do-it-yourself plywood formwork is quite easy to assemble.
Do-it-yourself plywood formwork If the do-it-yourself plywood formwork has already been planned completely and irrevocably, some features should be taken into account.
First, you should carefully choose the thickness of the plywood sheets. In this case, it is necessary to take into account the regularity that the thicker the foundation or other future concrete part, the thicker the plywood sheet used to make the formwork for it should be.
Secondly, the distance between the shields must strictly correspond to the expected thickness of the foundation; wooden blocks must be installed between the shields. The shields should be fastened together with nails, screws and wire.
Thirdly, the inside surface must be smooth, so all fasteners should be installed only from the outside. Nails must be hammered in with caps, and sharp ends on the outside must be bent with a hammer.
Fourthly, there should be no gaps between the plywood boards. If they do exist, then they need to be repaired.
Fifthly, so that the plywood formwork panels do not disperse under the pressure of the poured concrete mass, it is necessary to support them with pegs driven into the ground below from the outside. If the height of the designed foundation is more than 20 centimeters, then it is necessary to reinforce the formwork with special struts. To protect the structure from the pressure of concrete from the inside, metal or wooden clamps can be put on the formwork.
As noted above, making plywood formwork yourself is quite simple. To do this, you do not need anything except tools, a small amount of money to buy material and fasteners, a head, skillful hands, and, most importantly, desire.
Plywood for formwork
Understanding the possibilities
You cannot make sense of different types plywood formwork used today? Do you know which plywood will provide the best surface? Do you understand which plywood will provide lower costs for a given amount of work?
Not everyone can answer these questions. But keep in mind that labor and material costs, which make up a significant proportion of the cost of monolithic work, are critical to the prospects for long-term success in your business.
In this article, we provide information that will help you make more informed decisions by answering many questions regarding the use of plywood in monolithic works. It will also help you know exactly what questions to ask in order to be sure of the right choice.
What do I need to know before purchasing formwork plywood?
To confidently assess the effectiveness of the purchase of material, you must have answers to the following 6 questions:
What type of concrete will be used? The most important indicator of the alkali content in the concrete mixture. High PH is destructive to plywood and requires a protective coating.
What concrete surface quality is required?
Will plywood be used in a wall or floor formwork system?
What strength is required from plywood?
See also:
Any structure is impossible without a foundation. And a reliable and even foundation can be created only if strong and geometrically correct formwork is built. Despite the development of technical progress, traditional panel formwork continues to be an indispensable element. Recently, more and more often, wood is gradually being replaced by plywood. Do-it-yourself plywood formwork not only reduces construction time, but also allows you to significantly reduce costs.
The main advantages of using
One of the main reasons for replacing structures with plywood in the construction of formwork was the deformation of the tree under the action of mortar. Over time, the cost of timber and plywood formwork became almost the same, which only facilitated the replacement process.
In addition, the use of plywood has additional advantages:
- The smooth surface allows you to create the perfect shape.
- The installation process and assembly can be carried out in-house.
- The possibility of extrusion of individual elements under the action of the solution is minimized.
- Manufacturing time is extremely reduced.
- The use of separate macros allows you to withstand several fill cycles.
Important! If the structure is to be reused, the elements can be lubricated to facilitate subsequent dismantling.
The manufacturing procedure includes the main steps inherent in the traditional design, but has its own differences. To make plywood formwork for the foundation with your own hands, you must adhere to the recommendations:
Acquisition of the necessary material
Before starting work, you should purchase:
- Components for concrete (cement, sand, water, crushed stone).
- Armature and knitting wire.
- A bar for fasteners with a section of 50 to 50 mm.
- Fastening for plywood (studs and nuts).
- Fasteners (staples, screws, nails).
- Plywood.
- For a one-time construction, pine needles sheets are enough. To prevent delamination, it can be treated with linseed oil.
- For repeated use, moisture-resistant or laminated boards are suitable.
- To increase the service life, the ends of the plates can be treated with waterproof glue.
You will also need a concrete mixer, jigsaw, screwdriver, hammer and wrench.
After preparing the material, it is necessary to clear the area where the foundation will be poured, and mark it out using fishing line. First, the outer perimeter is beaten off, checked with diagonal measurements, after which the internal dimensions are marked taking into account the thickness of the foundation.
Installation
Trenches are dug along the markings. Sand is poured to the bottom, after which it is compacted.
Installation takes place in this order:
- Plywood sheets are placed on the outside of the trench, on each side.
- So that there is no displacement from the outside, beams, lintels and wedges (braces) are attached.
- Steel pins are used to securely fix the sheets. For this, holes are drilled in the attachment points equal to the diameter of the fastener. Before installation, a plastic tube is laid between the walls, where a hairpin is then inserted, which is fastened with nuts from the outside.
How to install the pin correctly when installing plywood formwork with your own hands, the video below will clearly demonstrate.
- To fix the distance between the sheets, wooden beams are placed inside, equal to the width of the fill.
Important! All drilled holes are treated with linseed oil to prevent moisture from escaping.
- To increase the reliability, the fasteners are installed in several rows. Fasteners are placed below and above the structure along the installed plywood sheets.
Important! If the height is too high, it is allowed to install fasteners in the middle of the sheet.
- Corner connections are secured with staples.
Important! All fasteners are carried out only from the outside. If nails are used, they are hammered from the inside and folded over from the outside. This is done to preserve the surface of the foundation.
- In the finished structure, holes and crevices are closed or puttyed, otherwise concrete leakage may occur. To reduce the concrete pressure along the perimeter of the formwork, reinforcement bars are driven into the ground, which are additionally fixed with a knitting wire. Clamps can also be used.
- If uncoated plywood is used, for easy dismantling of the structure, the inner walls can be treated with linseed oil, special solution or ordinary film.
- The foundation can be insulated. For this, polystyrene slabs can be placed between the formwork and the foundation.
- For the final completion of the installation, reinforcement must be carried out. For this, reinforcement is used, which is attached both along the foundation and across, after which it must be fixed with wire.
The formwork is ready!
Important! If the building has communications, in the process of preparing the formwork, it is necessary to provide for the laying of pipes along the perimeter of the foundation. This will greatly simplify the process of supplying communications at the stage of construction and installation work.
Laminated plywood
If the budget allows, formwork made of laminated plywood, with your own hands, will be an excellent solution. ... Unlike the usual one, it has its advantages:
- Increased strength to easily carry heavy loads.
- Possibility of installing fasteners with a step several times larger than for ordinary plywood, which is a consequence of its strength.
- Perfectly smooth and even surface even without additional sanding.
- Easy to install.
- Long service life, withstands up to 100 fillings.
In the end, you need to pay attention to the peculiarities of assembling the formwork for plywood walls with your own hands. The procedure is fundamentally no different from the described process. It is recommended to pay attention to the following points:
- For wall formwork, it is better to use new materials, since the old ones will leave marks on the surface.
- The skirting boards must be at an angle of 30 to 45 °, otherwise the structure may collapse.
- Plasticizers must be added to the concrete for the fortress before pouring the walls.
Using these tips, you can assemble the formwork without outside help with minimal costs.